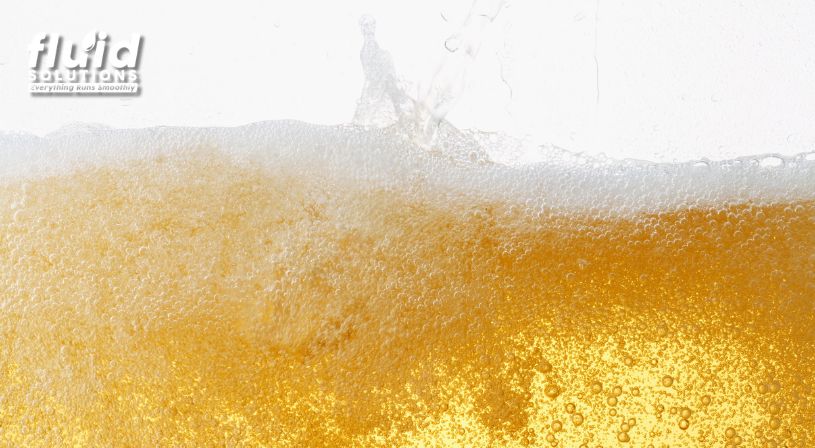
Source: Aflo Images
Hydraulic fluid foaming affects system performance and leads to unplanned downtimes. In the worst cases, a hydraulic fluid flush may be necessary. Considering the fluid replacement cost, finding a product that minimizes the risk of this issue will help in saving costs on expensive repairs and component replacement.
This article tackles common causes of foaming in hydraulic oils and prevention tips to minimize the risks.
Key Takeaways:
- Foaming in hydraulic fluids can lead to poor lubrication, pump damage, and costly machine downtimes.
- Air contamination, fluid agitation, incompatible or degraded fluids, and suction-side issues are common causes of hydraulic fluid foaming.
- Foam reduces system efficiency, increases wear, and raises the risk of unplanned system failure due to overheating and oxidation.
- Prevention includes using anti-foam additives, proper reservoir design, regular maintenance, and fluid analysis.
- Choose hydraulic fluids with strong air release, oxidation stability, and foam resistance to protect your investment and maintain productivity.
Effects of Foaming on Hydraulic Systems
Hydraulic fluid foaming is a minor problem that can lead to costly repairs if left unattended. It can negatively impact your machinery by causing:
- Loss of system efficiency and pressure instability. Hydraulic fluids are designed to resist volume reduction even when subjected to pressure. Foam affects the compressibility of this fluid, disrupting system performance and precision.
- Poor lubrication and increases wear. Hydraulic fluids lubricate machinery components to reduce friction. Foam decreases the lubrication efficiency of this oil, affecting the durability of components . It also increases the frequency of machine maintenance.
- Cavitation and pump damage. When air bubbles from foam move to higher-pressure areas and become exposed to pressure drops, they explode and create localized temperature increases that cause physical damage to valves.
- Temperature rise and fluid oxidation. Foam also traps heat, which accelerates oxidation and hastens the breakdown of additives in the lubricant. It further reduces the performance efficiency of machinery.
- Risk of system failure and unplanned downtime. The trapped heat causes unexpected machine failure, leading to sudden downtimes. Hence, hydraulic fluid foaming can halt production and impact manufacturing and industrial operations.
Causes of Foaming in Hydraulic Fluids
Foaming occurs when bubbles accumulate near or on the surface of the hydraulic fluids. There are several reasons for its formation. The most common causes include:
Air contamination
There are two main types of air contamination: entrained and dissolved air.
When air enters the hydraulic reservoir during maintenance or installation, it forms small bubbles below the hydraulic fluid surface. It happens because air becomes mechanically introduced into the hydraulic fluid. Air can also enter the hydraulic pump due to air leaks.
In contrast, dissolved air is visually unnoticeable because it occurs on a molecular level. Air dissolves in the hydraulic fluid and only appears foamy once the fluid experiences a pressure drop or a temperature increase. This contamination typically occurs because of temperature fluctuations, so bubbles can also appear even in enclosed systems.
Fluid agitation and aeration
Rapid fluid movement or splashing traps air in the hydraulic fluid, causing aeration or the process of air mixing into the hydraulic fluid. The trapped air in the fluid leads to an increase in foam formation and even entrained air.
Other causes of fluid agitation include overfilled reservoirs, poorly designed tanks which lead to oil falling straight into the reservoir, and air leaks.
Use of incompatible or degraded fluids
Mixing different hydraulic fluids can cause foaming because dissimilar brands have different additives that may be incompatible.
Similarly, cheap and degraded hydraulic fluids can lead to foaming. It usually happens should the anti-foam additives lose their efficacy due to use.
Leaks and suction-side issues
As mentioned, leaks are a common reason for air contamination, leading to hydraulic fluid foaming. This happens due to damaged or worn seals, hoses, or connectors.
How to Prevent and Eliminate Foaming
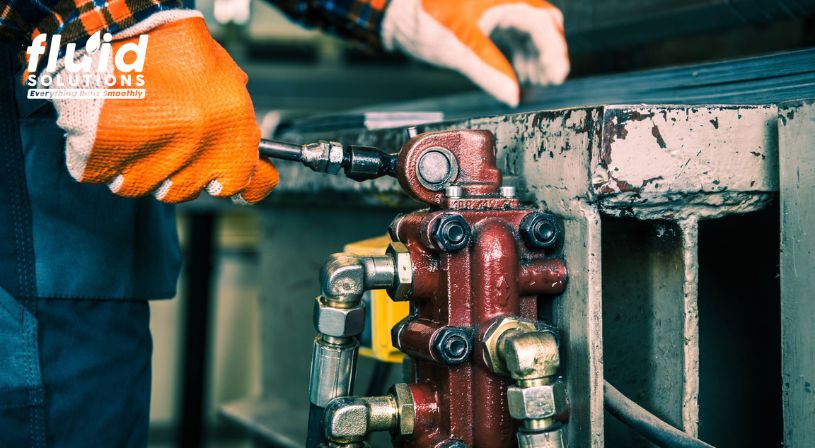
Source: https://www.bioblend.com/wp-content/uploads/What-Causes-Hydraulic-Fluid-to-Foam.jpg
Hydraulic fluid foaming affects the efficiency of your machine systems and leads to expensive repairs. Hence, knowing how to prevent it is important to keep your machinery working efficiently and for a long time.
Here are different ways to prevent hydraulic fluid foaming problems.
- Use of anti-foam additives. Anti-foam additives minimize the risk of foam forming on the oil surface. These additives in hydraulic fluid work by breaking up surface bubbles before they worsen. Common anti-foam additives include ester and silicone oils.
- Ensure proper reservoir design. Poorly designed tanks cause fluid agitation and foaming. A well-designed reservoir allows air to separate from the oil before it circulates. It also helps prevent air contaminants from entering the system.
- Keep consistent maintenance practices. Regular hydraulic system maintenance helps prevent this problem from worsening by addressing them before they negatively affect system performance. As a reminder, remember to:
- Vent the system to remove trapped air
- Inspect and replace worn seals to prevent leaks
- Degas the fluid if foaming is detected
- Monitoring for contamination and oxidation. Use fluid analysis programs to check for contamination and oxidation. Then, address problems immediately once they arise by changing filters, flushing fluids, or replacing worn parts.
- Selecting fluids with appropriate air release and demulsibility. Since the hydraulic fluid price is more costly, it is essential to choose the best product that suits your machine’s needs . Always pick the lubricant with strong air-release properties and higher demulsifying properties to prevent air and water contamination.Â
Protect Your Equipment with the Right Hydraulic Fluid
Hydraulic fluid foaming can be a costly problem. So, choose the right hydraulic fluid to protect your equipment from expensive repairs and increase its lifespan.
Get expert guidance from our team at Fluid Solutions to find the right hydraulic fluid for your operations. Our hydraulic oil has foam-resistant properties that completely protect your machine, ensuring consistent performance for a long time.
Minimize downtime and maximize system performance today! Contact Fluid Solutions today to find the best lubrication for your hydraulic systems. Call us today at (02) 8370 5928 / (0917) 8​9​4 9156 or via email at inquiry@fluidsolutions.com.ph.
Social Media Links:
Facebook: https://www.facebook.com/fluidsolutionsinc
LinkedIn: https://www.linkedin.com/company/fluid-solutions-inc