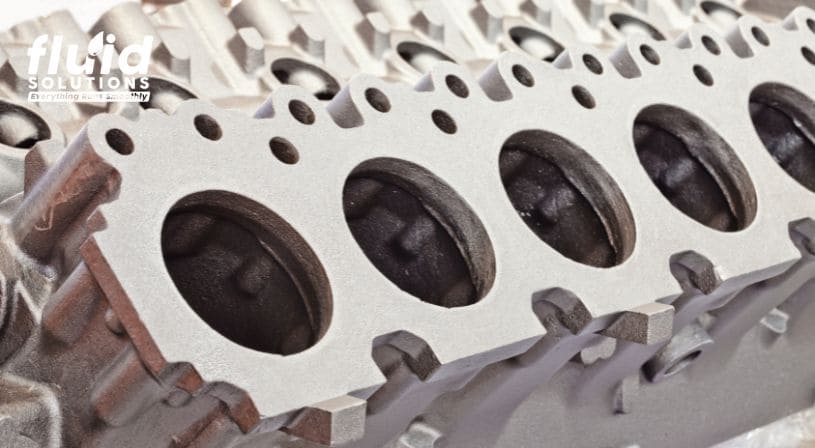
In high-pressure die casting, the role of release agents, or die lubes, extends far beyond their cooling function. These essential die-casting agents, are critical in forming a protective barrier that ensures the smooth release of cast products while enhancing their appearance. This blog explores how release agents form this barrier at the wetting temperature and the factors that influence their effectiveness in producing high-quality, defect-free castings.
Formation of the Barrier at Wetting Temperature
A. Wetting Temperature
The wetting temperature, typically below 400˚C, is the critical range where release agents effectively adhere to the die surface. When the die reaches this temperature, the water component of the die lube vaporizes, leaving behind the lubricating agents. These agents then form a thin, uniform film on the die surface, which plays a vital role in the casting process.
B. Barrier Function
The barrier created by the release agent is crucial in preventing soldering, a common defect where the casting sticks to the die. This thin film acts as a protective layer between the molten metal and the die, ensuring that the casting can be easily released without causing damage or distortion. Achieving a consistent and uniform film is challenging, as several factors can influence the barrier’s effectiveness.
Factors Affecting Film Formation
- Die Cavity Geometry
The geometry of the die cavity significantly impacts film formation. Complex shapes and varying surface contours can make it difficult to achieve a uniform barrier across the entire die surface.
- Surface Temperature Variations
Different areas of the die may have varying temperatures, affecting how well the release agent adheres. These temperature variations can lead to uneven film formation, which can compromise the casting quality.
- Spray Consistency
Consistency in the application of the release agent is essential. The volume, time, and position of the spray must be carefully controlled to ensure that the entire die surface is covered evenly.
- Die Lube Quality and Dilution Ratios
The quality of the die lube, its chemical composition, and the dilution ratios used during application are critical factors in film formation. Properly balanced emulsions ensure that the lubricating agents can form a reliable barrier.
- Metal Alloy Characteristics
Different metal alloys behave differently during the casting process, which can affect how well the release agent works. Understanding these characteristics is key to optimizing the release function.
Impact on Casting Appearance and Structural Integrity
A. Enhancing Appearance
When the barrier film is formed correctly, it can significantly enhance the appearance of the casting. A well-formed barrier leads to bright, shiny, and stain-free castings, which are highly desirable in the metal casting industry. This not only improves the aesthetic quality of the cast products but also adds value to the finished goods.
B. Structural Integrity
While the primary focus of the barrier is on release and appearance, it also has a minor impact on the structural integrity of the casting. A consistent barrier helps prevent defects that could weaken the casting, thereby contributing to the overall durability of the final product.
Enhance Your Die-Casting Process with Fluid Solutions
Fluid Solutions is a leading provider of advanced die-casting lubricants and release agents tailored to the high-pressure die-casting industry. With expertise in innovative solutions, we offer a comprehensive range of release agents designed to meet the specific needs of your operation.
For more information and to explore our offerings, contact Fluid Solutions today at (02) 8370 5928 / (0917) 894 9156 or via email at inquiry@fluidsolutions.com.ph and take the first step toward perfecting your die-casting process.