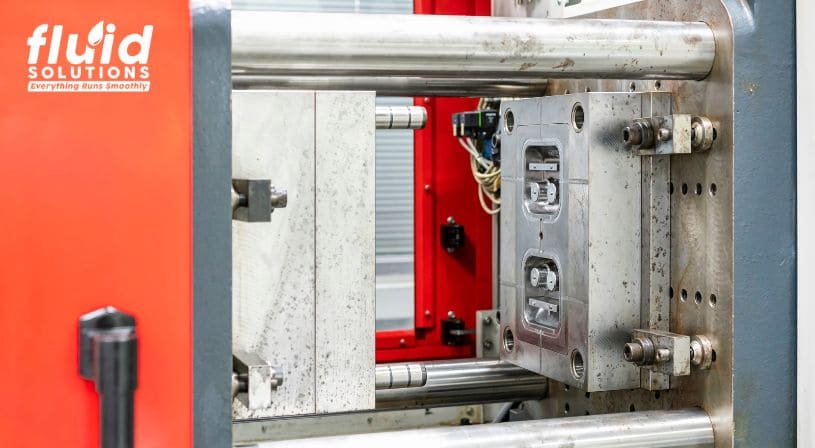
Release agents, commonly known as die lubes, are crucial in high-pressure die casting, serving multiple functions that ensure the quality and longevity of the casting process. Developed by leading, these agents play a vital role in cooling and protecting dies. This blog focuses on the composition of release agents, their essential cooling function, and how they promote the formation of a protective lubricating barrier on the die surface.
Composition of Release Agents
A. Emulsion FormÂ
Release agents used in high-pressure die casting are typically supplied as emulsions—a mixture of water, oils, and chemicals, often referred to as solids. The solids, which make up about 10% to 30% of the total emulsion, include various lubricating agents and additives essential for the die-casting process. This composition is carefully engineered by metalworking fluids manufacturers to meet the specific needs of die casters.
B. Dilution RatiosÂ
Before use, these emulsions, which are a type of water-based lubricants, are further diluted with water to achieve the desired concentration, with dilution ratios ranging from 1:20 to 1:250, depending on the application requirements. The water in the emulsion serves as a coolant, playing a critical role in protecting the die during the casting process.
Protecting the Die by Cooling
A. Cooling FunctionÂ
The primary cooling function of release agents comes from the water component, which absorbs heat from the die surface. When applied correctly and in appropriate volumes, the release agent can lower die temperatures from as high as 500ËšC to ​around​ 200ËšC. This cooling is crucial to prevent the die from overheating, which could lead to thermal stresses and premature wear. Other cooling mechanisms, such as the die’s internal cooling system and natural convection, also contribute to temperature reduction.
B. Preventing Thermal StressÂ
By effectively cooling the die, release agents help prevent thermal stress, which is a leading cause of die failure. Thermal stress occurs when there is a significant temperature difference across different parts of the die, leading to expansion and contraction that can cause cracks or deformities. In high-volume production environments where cost efficiency is paramount, preventing thermal stress is essential for extending the life of the die and reducing manufacturing costs.
Promoting Lubricant and Barrier Formation
A. Leidenfrost EffectÂ
At temperatures above 400ËšC, a phenomenon known as the Leidenfrost effect occurs. When release agents are sprayed onto the hot die, the particles, including the solids, may bounce off the surface rather than adhere to it. This effect can hinder the formation of a protective lubricating barrier, making it necessary to manage die temperatures carefully.
B. Wetting TemperatureÂ
To overcome the Leidenfrost effect and ensure that the solids in the release agent adhere properly to the die surface, the die must be cooled to the ‘wetting’ temperature range. This range typically falls between 150ËšC and 400ËšC. At these temperatures, the solids in the die lube can effectively form a thin, uniform lubricating and barrier film on the die cavity surface, which is essential for the smooth release of castings and the protection of the die.
Release agents play a pivotal role in high-pressure die casting by cooling the die, preventing thermal stress, and promoting the formation of a protective lubricating barrier. Understanding the composition and functionality of these agents is crucial for optimizing the die-casting process and extending the life of the die.
Optimize Your Die Casting Process with Fluid Solutions
Fluid Solutions is a leading provider of advanced die-casting lubricants and release agents tailored to the high-pressure die-casting industry. As one of the top metalworking fluids manufacturers, we offer cutting-edge formulations and expert solutions designed to enhance your die-casting process and improve operational efficiency.Â
For more information or to explore our range of release agents, contact us today at (02) 8370 5928 / (0917) 894 9156 or via email at inquiry@fluidsolutions.com.ph and take the first step toward optimizing your die-casting operations.Â