
Wire ropes are essential components often used to move parts or carry loads in industrial settings. They are particularly common in machines with cranes used when lifting heavy objects. Moreover, wire ropes can also carry elevators and provide the support needed in suspension bridges.
Maintaining wire ropes at their peak performance is a complex task that demands expertise. Lubricating wire ropes, regardless of composition, is not simple, and selecting the right kind of wire rope lubricant needs careful consideration.
The right wire rope lubricant is not just a maintenance tool but also a safety measure. It reduces friction, protects from corrosion, prevents internal wear, and ensures work safety. The following sections delve into the importance of proper lubrication and its impact on wire rope performance.
Understanding Wire Rope Lubricants
What is a wire rope lubricant?
Wire rope lubricants have a long history of evolution from simple oils to complex synthetic compounds. Ultimately, wire rope lubricant is designed specifically to reduce friction and provide corrosion protection and lubrication in the core and inside wires and on the exterior surfaces; thereby enhancing the performance of wire ropes used in various industrial applications.
What makes a good wire rope lubricant?
Wire ropes often move against each other and are exposed to moisture and corrosive elements that reduce efficiency and raise safety concerns. To prevent these scenarios, consider the following key characteristics when selecting the right product for a wire rope lubrication system:
- Penetration ability: Prevent wire ropes from failing and breaking from the inside, with a high-quality lubricant that penetrates deep into the wire rope’s core. For this purpose, penetrating lubricants often contain petroleum solvents that evaporate upon application, leaving a protective film.
- Wear resistance: The right industrial lubricant for wire ropes should minimize strand wear. More specifically, it should have high four-ball extreme pressure (EP) test values, which indicates the lubricant’s ability to withstand high loads without breaking down.
- Water resistance: The lubricant must be water-repellent and water-resistant to protect the wire rope from moisture that leads to corrosion. In other words, the lubricant should not dissolve in water to ensure its protective properties even in wet conditions.
- Good covering properties: The wire rope lubricant should have excellent covering properties to ensure that it adheres well to the wire surface and provides consistent protection across all strands of the rope.
- No contaminants: Wire rope lubricants should be free from grit, abrasives, and other impurities. Moreover, it should not have additives that can degrade or form corrosive products upon contact with water.
- Tacky consistency: A tacky lubricant can adhere to the wire rope better, helping to seal out moisture and protect against wear. This characteristic is particularly beneficial in high-motion applications
- Corrosion resistance: Effective lubricants protect against corrosive elements like salt water, humidity, and other environmental factors. Look for lubricants with high corrosion resistance, as indicated by tests like salt spray and humidity cabinet tests.
Types of Wire Rope Lubricants
- Penetrating lubricants: This type is designed to reach the core of the wire rope, providing thorough lubrication and protection against internal wear.
- Coating lubricants: These provide a protective layer on the outer surface of the wire rope, sealing it against moisture and reducing external wear.
Ideally, a combination of both types is often recommended to ensure comprehensive protection. The penetrating lubricants must first saturate the core. Coating lubricants then follow this to seal the outer surface.
How to Apply Wire Rope Lubricants
Generally, there are two types of wire rope lubricant applications: manual and automated lubrication systems.
Manual application
The manual process would usually involve the following steps:
- Cleaning the wire rope: If the rope is dirty or has accumulated hardened lubricant or contaminants, clean it with a wire brush, petroleum solvent, compressed air, or steam cleaner before relubrication
- Drying the rope: After cleaning, ensure the wire rope is completely dry to prevent rusting before applying the new lubricant.
- Applying the lubricant: There are three main methods for manually applying lubricant to wire ropes: dripping, spraying, or brushing.
- Targeting the right areas: Apply the lubricant at the top of a bend, such as around a sheave, where the rope strands are spread and can be more easily penetrated.
The tools and equipment needed for the manual method include rags, gloves, a wire brush, a spray applicator or brush, and the appropriate wire rope lubricant. Moreover, manual methods risk excessive application, creating safety hazards and excessive waste.
Automatic lubrication systems
Unlike manual methods, automatic wire rope lubrication systems provide more consistent and effective results. These systems use a pump to force the lubricant into the core of the wire rope, ensuring even distribution and penetration. The following are the benefits of an automatic wire rope lubrication system:
- Reduced lubrication time by up to 90% compared to manual methods.
- Improved safety by minimizing worker exposure to the rope and lubricant.
- Consistent and thorough lubrication, reaching the core of the rope.
- Reduced waste and environmental contamination.
- Longer service life for wire ropes.
Automatic systems are particularly beneficial for large-scale operations with multiple ropes or hard-to-reach locations, such as cranes, drilling rigs, and mining equipment.
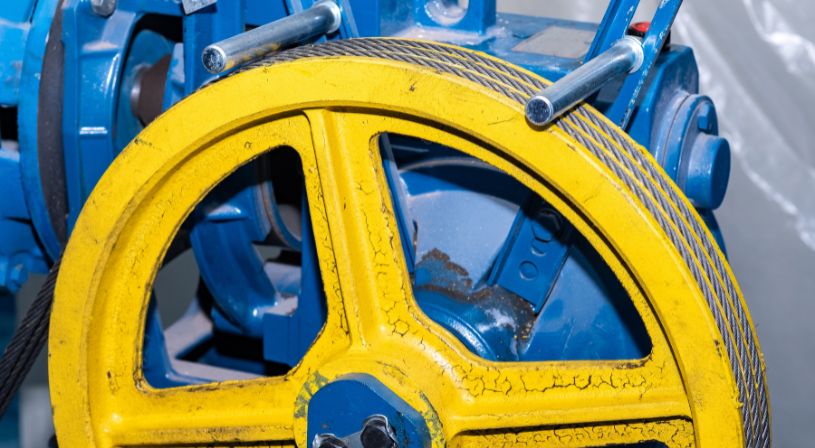
Ensure Maximum Efficiency with Premium Wire Rope Lubricants from Fluid Solutions
Specialty lubricants distributors like Fluid Solutions ensure that you get the best quality wire rope lubricants for specific applications. As a trusted lubrication partner in the industry, Fluid Solutions offers high-quality wire rope grease and coating compounds for your internal and external applications. These products suit transmissions, rollers, elevator chains, and forklifts. Our premium-grade wire rope coating also offers better protection for longer than ordinary wire rope lubricants.
Reach out to Fluid Solutions and let us help you find the right lubricants for your specific needs. Contact us at (02) 8370 5928 / (0917) 894 9156 or email inquiry@fluidsolutions.com.ph.
Social Media Links:
Facebook Page: https://www.facebook.com/fluidsolutionsinc
LinkedIn: https://www.linkedin.com/company/fluid-solutions-inc