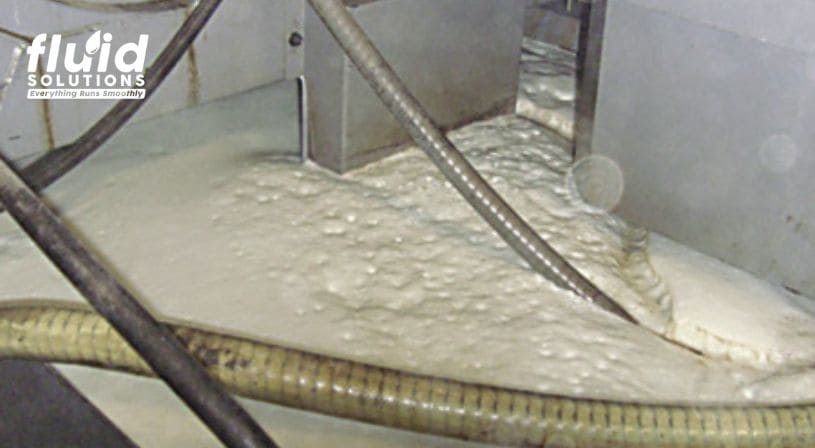
Foaming in metalworking fluids (coolants) is a common ​yet​ frustrating issue faced by many machine shops. Whether you are using water-soluble coolants, emulsions, synthetics, or semi-synthetics, the incidence of foam can negatively impact the cooling process, reduce tool life, and compromise surface finishes. In extreme cases, excessive foaming can cause coolant overflow, creating a hazardous working condition, and leading to equipment damage.
In this blog, we’ll explore the causes of foaming in coolants, discuss troubleshooting tips, and highlight the importance of partnering with reputable ​machining and grinding ​fluids manufacturers.
Understanding Foaming in Coolants
Foaming occurs when air becomes trapped in the coolant and forms bubbles. This is often exacerbated by mechanical agitation, contamination, or improper coolant maintenance. While some amount of foaming can be inevitable due to the nature of coolants, excessive or persistent foaming requires immediate attention as it can lead to performance issues. Machine operators and maintenance teams need to understand the causes of foaming to minimize its occurrence.
The Causes of Foaming
To effectively troubleshoot foaming, you must identify the root cause. Here are several factors that can lead to foaming in coolants:
- Water QualityÂ
Water quality plays a crucial role in preventing foam formation. If the water used to mix the coolant is too soft (0 to >100 ppm CaCO3), it can result in excessive foaming. Soft water doesn’t contain enough minerals to prevent foam, causing the coolant to behave unpredictably. If changing the water source isn’t feasible, consider selecting a ​machine ​fluid specifically designed for use with soft water. Additionally, before purchasing coolants, perform comparative tests using test tubes or graduated cylinders to gauge foaming behavior with different water sources. - Low Fluid Levels in the Coolant SumpÂ
When coolant levels in the sump are too low, the pump’s suction inlet may not be fully submerged, causing air to be introduced into the system. This introduces bubbles into the circulation, leading to foam. To correct this, ensure that the coolant sump is always at least 80% full. Maintaining optimal fluid levels will help minimize air intake and prevent foaming issues. - Excessive Coolant Flow or Improper AgitationÂ
Excessive coolant flow rates or improperly agitated fluids can result in air being mixed into the coolant. If the return fluid splashes or spills directly into the sump, air bubbles can form, causing foaming. To prevent this, reduce coolant flow rates and pressures. Additionally, you can install deflectors to soften the landing of return fluid, which helps reduce turbulence and minimizes foaming. - Coolant ContaminationÂ
Cross-contamination between different fluids can lead to foaming. In cases where machine sumps are filled manually, topping up with the incorrect coolant can introduce foam. Another common issue arises when ​one​ uses multiple products from the same supplier, such as coolants and degreasers. Accidentally charging degreasers, which have high detergency properties, into the sump instead of coolant can trigger excessive foaming. To avoid this, implement proper labeling and handling systems to ensure the correct fluids are used. - Incorrect Coolant Concentration
Using coolant at the wrong concentration level can also cause foaming. Concentrations that exceed 10% can lead to foam formation, particularly in water-soluble coolants. To avoid this, always follow the coolant manufacturer’s recommended concentration range. Use refractometers to regularly check concentration levels and assign a designated person to monitor coolant concentration as part of your standard operating procedures. Maintaining the right concentration levels will reduce foaming and improve overall coolant performance. - Temporary Fixes: Tank-Side Defoamers
If foaming persists despite troubleshooting efforts, tank-side defoamers can be used as a temporary solution. However, this is only a stop-gap measure and does not address the root cause of the foaming issue. Defoamers break down existing foam but won’t prevent future foam from forming. It is important to investigate and resolve the underlying problem to achieve long-term results.
Metalworking Fluids Manufacturers and Coolant Troubleshooting
Partnering with reputable ​machining and grinding ​fluids manufacturers is essential for maintaining coolant performance and minimizing issues like foaming. A high-quality coolant designed to handle your specific machining processes can significantly reduce the likelihood of coolant problems. Leading manufacturers, such as Fluid Solutions, provide a wide range of metalworking fluids that are engineered to perform effectively while minimizing foam.
Contact us today at (02) 8370 5928 / (0917) 894 9156 or via email at inquiry@fluidsolutions.com.ph.