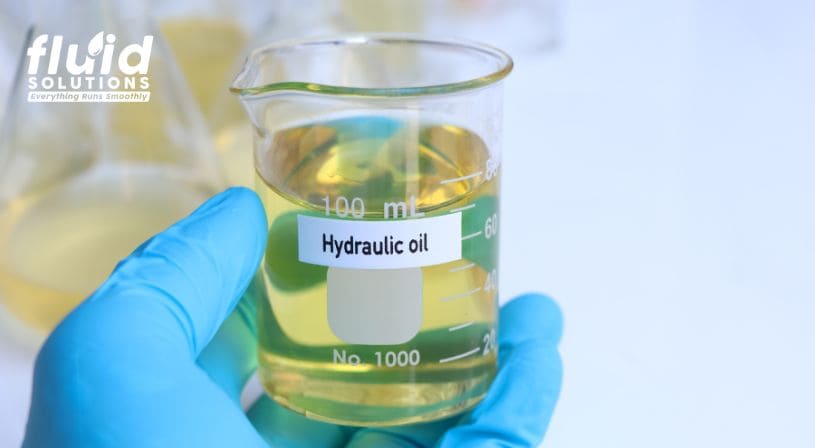
Image Source: https://www.shutterstock.com/image-photo/hydraulic-oil-container-science-experiment-concept-2303793865
Why Cleanliness Is Important in Hydraulic Oil Performance
- System efficiency
Clean hydraulic oil ensures the smooth operation of components by preventing excessive friction or wear. Contaminants like dirt, water, and metal particles can restrict oil flow, leading to increased energy consumption and reduced efficiency. Studies show that nearly 80% of hydraulic system problems are related to contaminated fluid, underscoring the importance of hydraulic oil cleanliness. - Wear reduction
Solid particles in hydraulic oil can lead to increased wear on system components. The size and quantity of these particles are also critical, as smaller particles can cause significant damage. Cleaner oil translates to lower wear rates, extending the service life of hydraulic components.
Key Takeaways:
- 80% of hydraulic failures are caused by contaminated oil—cleanliness is critical.
- ISO 4406 is the industry standard for measuring particle contamination in hydraulic fluids.
- Clean oil reduces wear, improves efficiency, and extends system life.
- NAS 1638 is another cleanliness standard still used in aerospace and legacy systems.
- Regular monitoring and maintenance help ensure compliance and system reliability.
Industry Standard for Oil Cleanliness
The International Organization for Standardization (ISO) has laid out a cleanliness code for industrial oil analysis reports that helps determine the overall cleanliness of the systems being monitored. These standards help in setting goals and target alarms for achieving and maintaining hydraulic oil cleanliness in various systems.
ISO 4406 Cleanliness Standard
ISO 4406 is a widely used international industry standard that shows the level of particle contamination of hydraulic fluid power systems. Under ISO 4406, cleanliness levels are measured by counting and classifying particles present in a known volume of hydraulic fluid.
ISO 4406 cleanliness is classified by a two or three-number code that represents the number of contaminant particles greater than 2 µm, 5 µm, and 15 µm, where µm represents microns.
This standardized method for determining and expressing particulate contamination in hydraulic fluids allows for effective communication of fluid cleanliness between manufacturers, suppliers, and end-users. The ISO 4406 standard is particularly used in industries where hydraulic systems are critical, such as manufacturing, aerospace, automotive, and construction.
Understanding the ISO 4406 Code System
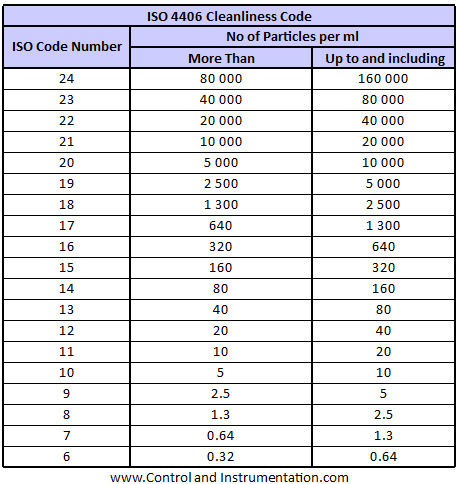
Image source: https://www.controlandinstrumentation.com/valves/hydraulic-cleanliness.htm
The ISO 4406 cleanliness code is usually expressed in three numbers, such as 18/16/13. Each of these numbers represents the contaminant level for a specific particle size range:
- The first number corresponds to particles larger than two (2) μm.
- The second number corresponds to particles larger than five (5) μm.
- The third number corresponds to particles larger than ​fifteen (​15​)​ μm.
Using the table above, an oil rating of 16/14/11 means it has:
- 320-640 particles greater than two (2) μm.
- 80-160 particles greater than five (5) μm.
- 10-20 particles greater than 15 μm.
Meeting ISO 4406 standards ensures the reliability and efficiency of hydraulic systems. It prevents component wear, enhances system performance, reduces downtime, ensures compliance, and extends fluid longevity. Hence, hydraulic system maintenance is an essential practice for any organization relying on their efficient functioning.
NAS 1638 Cleanliness Standard
The National Aerospace Standard (NAS) 1638 standard is another guideline for assessing hydraulic oil cleanliness. First implemented in the 1960s in the aircraft industry, this standard controlled the amount of contamination in aircraft hydraulic components.
Like ISO 4406, it is a particulate contamination coding system that simplifies the communication of data from particle counters. Unlike ISO 4406, however, it categorizes cleanliness into classes based on the number of particles present in a volume of fluid.
Classes Under NAS 1638
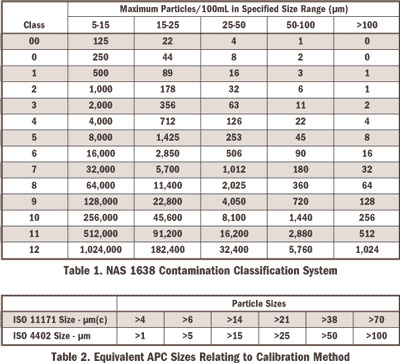
Image Source: https://www.machinerylubrication.com/Read/409/nas-1638
The classes range from Class 1 (very clean) to Class 12 (very dirty). While ISO 4406 is more commonly used today, NAS 1638 remains relevant in certain industries, particularly where specific cleanliness requirements are mandated. Understanding both standards allows for better alignment with industry practices and ensures that hydraulic systems operate effectively.
Conclusion
By adhering to established cleanliness standards like ISO 4406 and NAS 1638, operators can significantly reduce the risk of contamination-related failures, ensuring reliable system performance. Prioritizing hydraulic oil cleanliness contributes to the long-term health of hydraulic systems. Regular monitoring and proactive maintenance practices are key to achieving and maintaining optimal cleanliness levels.
Elevate Your Operations with Fluid Solutions—Secure Clean Hydraulic Oil with Our Expertise!
As a leading industrial lubricant supplier in the Philippines, Fluid Solutions’ comprehensive range of hydraulic oils keeps systems at peak cleanliness levels, ensuring maximum efficiency and longevity of your machinery.
For further help, visit our product page or contact us today. Let us help you find the right lubricants for your specific needs. Alternatively, you may also reach out to (02) 8370 5928 / (0917) 894 9156 or email inquiry@fluidsolutions.com.ph.
Social Media Links:
Facebook Page: https://www.facebook.com/fluidsolutionsinc
LinkedIn: https://www.linkedin.com/company/fluid-solutions-inc