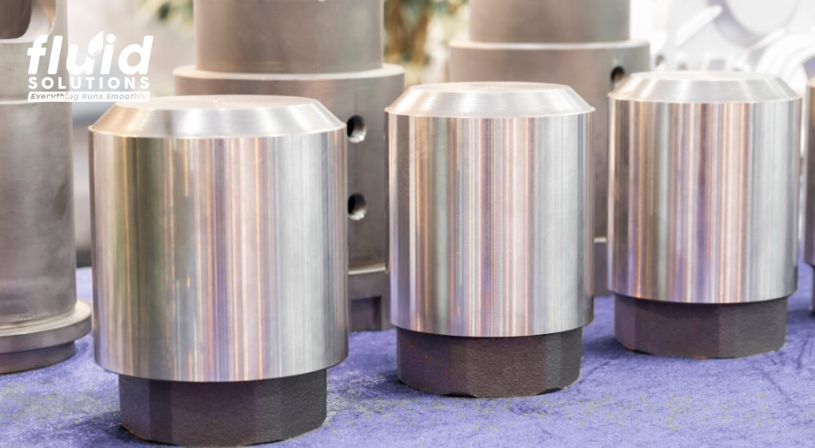
In high-pressure die-casting machines, the plunger tip and plunger sleeve are vital components that work in tandem to inject molten metal into the die cavity at extremely high speeds up to 10 meters per second and pressures as high as 10,000 psi. In this blog, we delve into how plunger lubrication is essential for reducing friction and wear, prolonging the life of plunger sleeves and tips, and sustaining the high pressures needed to produce quality castings.
Materials of Plunger Tips and Sleeves
A. Plunger Tips
Plunger tips are typically made from nitride steel or copper, both of which offer the durability needed to withstand the extreme pressures and temperatures involved in the die-casting process. The choice of material can influence the wear rate and overall performance of the plunger tip, making it a critical decision for die casters.
B. Plunger Sleeves
Plunger sleeves, which are usually made from nitrided steel, are designed to last longer than plunger tips—typically four to five times longer.
Importance of Plunger Lubrication
A. Reducing Friction and Wear
Plunger lubrication is vital in reducing the friction and wear that occurs at the interface between the plunger tip and the sleeve. The high speeds and pressures involved in the process can cause significant wear on these components if not properly lubricated. By minimizing friction, lubrication helps to optimize the lifespan of both the plunger tip and the sleeve, providing economic benefits for die casters by reducing the frequency of component replacement.
B. Maintaining High Pressures
Maintaining the high pressures required for sound casting is directly related to the condition of the plunger tip and sleeve. As these components wear, the diametrical clearance between them increases, which can lead to a drop in the pressure required to produce defect-free castings. Proper lubrication minimizes this wear, helping to maintain the necessary high pressures and ensuring consistent casting quality.
For more detailed information and resources, we invite you to visit Fluid Solutions’ website.
Optimize Your Plunger Lubrication with Fluid Solutions
Fluid Solutions is a leading provider of advanced lubrication solutions tailored for the die-casting industry. With a comprehensive range of products designed to meet the specific needs of high-pressure die-casting machines, we offer innovative technologies to optimize your plunger lubrication process. Contact Fluid Solutions today at (02) 8370 5928 / (0917) 894 9156 or via email at inquiry@fluidsolutions.com.ph to learn more about their offerings and to schedule a consultation with their experts.Â