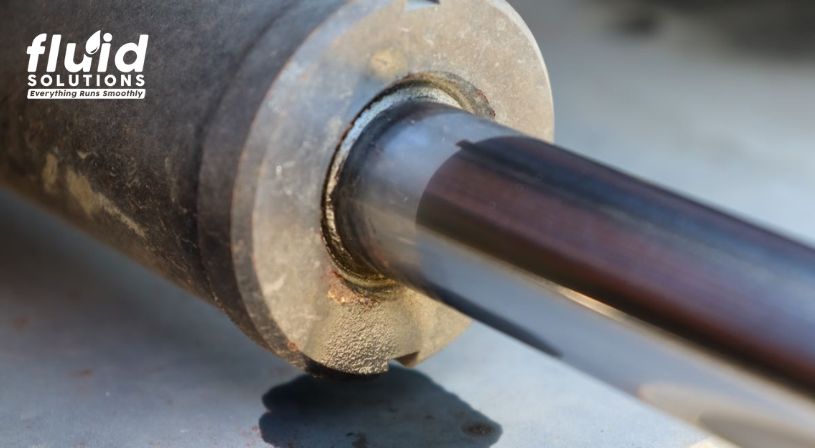
Image Source: https://www.primaryfp.co.uk/wp-content/uploads/2022/11/hydraulic-leak.jpeg
Hydraulic seals play a critical role in maintaining pressure, preventing fluid leaks, and ensuring the smooth operation of hydraulic machinery. These components are often overlooked until a failure occurs, resulting in costly downtime and repairs. To ensure optimal hydraulic system maintenance, it’s essential to understand the common causes of seal failures and implement strategies to prevent them.
Key Takeaways
- Seal failure is a major cause of hydraulic leaks and downtime.
- Common causes include material wear, chemical incompatibility, temperature extremes, contamination, and poor installation.
- Use compatible hydraulic fluids and select seal materials suited to your system’s pressure and temperature range.
- Ensure cleanliness, routine inspections, and proper installation techniques to extend seal life.
- Staff training on seal handling can significantly reduce installation-related failures.
Common Causes of Seal Failures in Hydraulic Systems
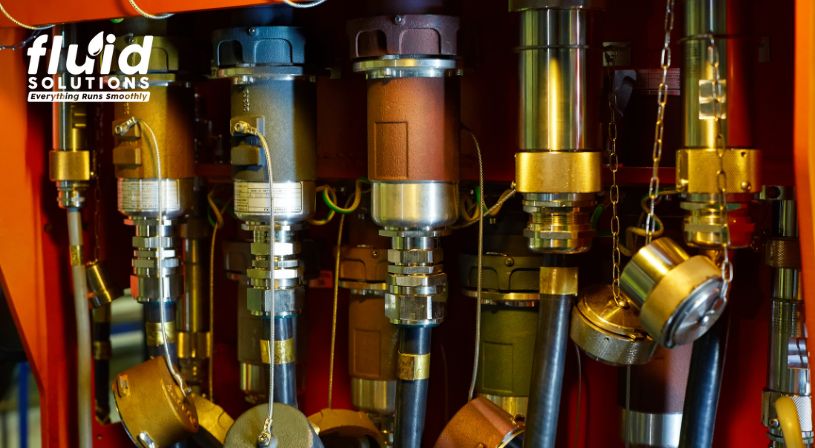
Image Source: https://www.freepik.com/premium-photo/hydraulic-oil-drive_6246852.htm#from_view=detail_alsolike
 1. Material Degradation and Wear
Over time, hydraulic oil seals naturally degrade due to exposure to pressure, heat, and contaminants. Common signs of wear include:
- Cracking or hardening
- Loss of elasticity
- Surface erosion or pitting
Most seals are made from materials like polyurethane, nitrile rubber (NBR), fluorocarbon (FKM), or PTFE. These must be carefully selected based on system pressure, temperature, and the hydraulic fluid compatibility.
2. Chemical Incompatibility
Seal degradation often stems from exposure to hydraulic fluids that contain incompatible additives. Even high-quality hydraulic oils can damage seals if their chemical formulations are not compatible. Incompatible oils can cause seals to:
- Swell excessively
- Shrink or crack
- Become brittle or soft
To avoid this, always ensure hydraulic fluid compatibility by consulting seal manufacturers and fluid spec sheets. This ensures your hydraulic oil seals last longer and perform reliably.
3. Extreme Temperatures
Hydraulic seals are highly sensitive to temperature variations. Excessive heat can cause:
- Hardening or glazing of seal surfaces
- Accelerated aging and deformation
Cold temperatures can reduce seal flexibility, leading to cracking and loss of sealing efficiency. Systems that operate in extreme environments require seals rated for a broad temperature range—and compatible hydraulic fluids to support them.
4. Contamination and Abrasive Wear
Foreign particles such as dust, metal shavings, or moisture can severely damage hydraulic oil seals. Contamination typically enters through:
- Damaged wipers or rod seals
- Inadequate filtration
- Poorly sealed reservoirs
Microscopic debris can score sealing surfaces and lead to premature failure. Cleanliness is key to successful hydraulic system maintenance.
5. Improper Installation
Seal damage frequently occurs during installation due to:
- Incorrect sizing or alignment
- Use of sharp tools
- Over-tightened components
Proper training, tools, and techniques are crucial to ensure seal integrity and avoid early leaks.
Best Practices to Maximize Seal Life
Implementing these best practices plays a vital role in extending the lifespan of hydraulic seals and maintaining overall system efficiency. By using compatible hydraulic fluids, monitoring operating conditions, ensuring proper installation, and keeping the system clean, you can significantly reduce the risk of seal failure. These measures not only help prevent costly leaks and unplanned downtime but also contribute to the long-term reliability and performance of your hydraulic equipment.
Use Seal-Compatible Hydraulic Fluids
Choose oils that meet the required hydraulic fluid compatibility standards for your seal materials. Using the wrong type can drastically reduce seal performance and life span.
Monitor Temperature and Pressure Ranges
Maintain operating conditions within the recommended limits. For extreme systems, opt for advanced hydraulic oil seals and oils with high thermal stability.
Implement Routine Seal Inspections
Proactive checks can prevent unexpected downtime. Replace seals when early signs of degradation are found.
Maintain Cleanliness
A clean environment reduces the chance of abrasive wear. Effective filtration and sealed storage practices go a long way in supporting overall hydraulic system maintenance.
Train Staff on Proper Seal Handling
Educating your maintenance team on best practices for handling and installing hydraulic seals helps prevent installation-related failures.
Conclusion
Your hydraulic system’s performance hinges on the reliability of its hydraulic seals. By selecting quality seals, ensuring hydraulic fluid compatibility, and enforcing strong maintenance practices, you can prevent leaks and extend your equipment’s service life.
If you’re unsure what type of seal or fluid suits your system—or are concerned about hydraulic fluid price and compatibility—Fluid Solutions can help.
Need Expert Help with Hydraulic Seal Performance?
Fluid Solutions offers expert advice and a wide selection of sealing components for all types of hydraulic applications. Whether you need help choosing the right hydraulic seals or identifying the most cost-effective hydraulic fluid price, our team is ready to assist.
For more information, you may contact us through the website or call (02) 8370 5928 / (0917) 894 9156. Alternatively, you may also email your concerns to inquiry@fluidsolutions.com.ph.
Social Media Links: 

Facebook Page: https://www.facebook.com/fluidsolutionsinc
LinkedIn: https://www.linkedin.com/company/fluid-solutions-inc