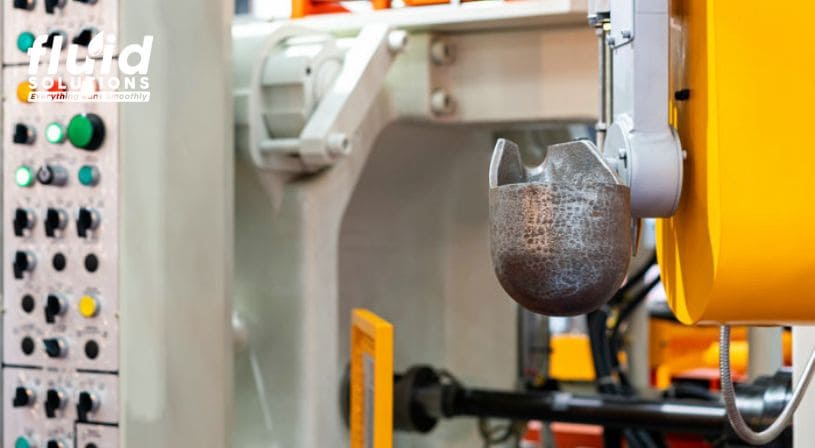
In metalworking, particularly in High-Pressure Die Cast Machines (HPDCM), plunger lubrication is essential for efficient and flawless operations. Proper lubrication is critical for extending the lifespan of tips and sleeves, which endure extreme conditions. This blog delves into the importance of effective plunger lubrication, the challenges encountered.
Challenges in Plunger Lubrication
- Boundary, Non-Film Lubricating Scenario
Plunger lubrication in HPDCM is uniquely challenging due to the boundary lubrication scenario it encounters. Unlike full-film lubrication, where a consistent layer of lubricant separates surfaces, boundary lubrication occurs when the lubricant film is thin or nearly absent. This scenario can lead to increased wear and tear on tips and sleeves, reducing their lifespan and the quality of the castings produced.
- High Pressures
In the plunger mechanism, pressures can soar to 10,000 psi, making lubrication challenging. Under such extreme pressures, maintaining a stable lubricant film is not possible. The lubricant must withstand these conditions and still provide protection for the tips and sleeves.
- High Temperatures
High temperatures, primarily influenced by molten aluminum, pose another significant challenge. The lubricant must not only maintain its properties under these extreme temperatures but also prevent the plunger tip from seizing or causing defects in the castings. The thermal stability of the lubricant is thus a key factor in its effectiveness.
Technologies for Plunger Lubrication
Mineral Oils
Mineral oils are the most used lubricants in HPDCMs due to their high viscosity, typically ranging from 1,000 cst to 5,000 cst at 40°C. This high viscosity helps these lubricants withstand the high pressures and temperatures encountered during the die-casting process. Additionally, mineral oils often contain extreme pressure additives similar to those found in gear oils, further enhancing their performance.
Premium formulations of mineral oils also include solid lubricants such as Graphite, Molybdenum Disulfide, and PTFE. These solid lubricants are known for their superior friction-reduction properties, making them ideal for applications, where reducing wear and extending the lifespan of tips and sleeves are critical.
Advantages of Mineral Oils
Mineral oils offer several advantages, including affordability and satisfactory wear protection for tips and sleeves. These oils are typically applied via a drip system, either into the sleeve hole or on a retracted tip immediately after casting ejection. This application method ensures that the lubricant is effectively distributed, providing adequate protection during the die-casting process.
Disadvantages of Mineral Oils
Despite their advantages, mineral oils come with certain drawbacks. The most notable is the tendency for excess lubricant to drip, leading to dirty and oily work areas. These drippings are difficult to control, especially given the open, hollow nature of the sleeve. This not only creates a safety and environmental hazard but can also result in the over-application of oil, potentially staining castings if the oil mixes with the solidified material.
Discover Superior Lubrication Solutions with Fluid Solutions
Fluid Solutions stands at the forefront of innovation in plunger lubrication oils for HPDCMs. As a leading provider of industrial lubricators and metalworking fluids, We offer a comprehensive range of products designed to meet the specific challenges of die-casting. This includes not only high-performance mineral oils but also advanced dry lubricants and water-based formulations, each tailored to provide superior lubrication, reduce environmental impact, and enhance the efficiency of the die-casting process.
For those looking to optimize their die-casting operations, Fluid Solutions provides expert consultation and a variety of products to ensure that your HPDCMs operate at peak performance. Explore their lubrication solutions today to experience the benefits of cutting-edge technology in metalworking. Contact Fluid Solutions today at (02) 8370 5928 / (0917) 894 9156 or via email at inquiry@fluidsolutions.com.ph to learn more.