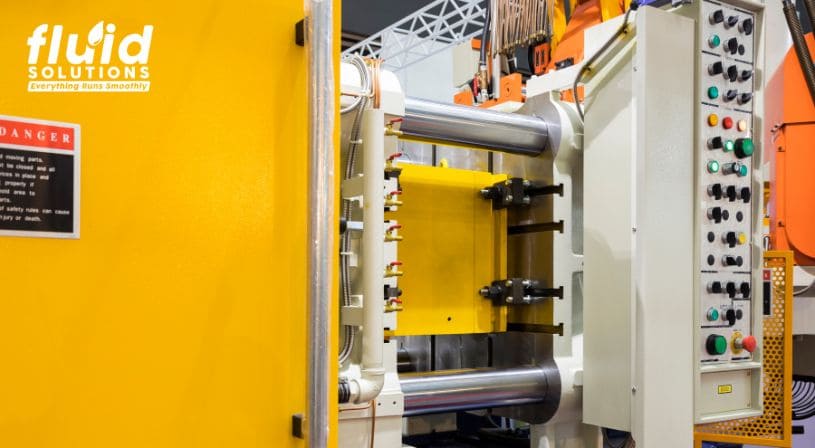
Dry plunger lubricants have been available for High-Pressure Die Cast Machines (HPDCM) for decades. However, their adoption in the die-casting industry, despite the efforts of metalworking fluids manufacturers, has been slower compared to traditional mineral oils. This blog delves into the reasons behind this slower adoption, the working mechanisms of dry plunger lubricants, and their benefits, and introduces Fluid Solutions’ advanced lubrication technologies as a promising alternative.
Challenges with the Adoption of Dry Plunger Lubricants
A. Investment in Specific Equipment
One of the primary challenges in adopting dry plunger lubricants is the need for a dedicated dispensing unit. Unlike conventional lubricants, which can be applied using standard equipment, dry lubricants require specific systems to be effective. This initial investment can be a significant barrier for many die-casters, particularly those who are already set up for mineral oil-based systems.
B. Operator Resistance
Another hurdle is operator resistance. The shift from familiar mineral oil lubricants to dry lubricants involves new procedures and maintenance routines. Operators, accustomed to the old systems, may be reluctant to adopt these new practices, viewing them as more complex or time-consuming.
C. Effectiveness Concerns
Finally, there are concerns about the effectiveness of dry lubricants. Die casters often doubt whether solid lubricants, such as dry graphite lube, can match the friction reduction properties of liquid lubricants. These doubts can hinder the willingness to transition to dry plunger lubrication technologies.
How do dry plunger lubricants work?
- Form and Composition
Dry plunger lubricants typically come in the form of pellets or beads, usually measuring 2-3 mm in diameter. These pellets are composed mainly of waxes and sometimes include additives like graphite to enhance their lubrication properties.
- Melting Point and Lubrication Process
One of the key features of these pellets is their low melting point, typically below 80°C. When the pellets are dispensed into the sleeve hole of a high-pressure die-casting machine, the heat from the molten aluminum causes them to liquefy. This liquefied lubricant then provides the necessary friction and wear reduction between the plunger tip and the sleeve, ensuring smooth operation.
Dispensing Mechanism
The dispensing of dry plunger lubricants is done using a specialized applicator. This applicator is connected to an air line and synchronized with the plunger-return limit switch of the HPDCM. As the plunger tip retracts, the applicator dispenses a pre-measured quantity of pellets into the sleeve. This process repeats with each cycle, ensuring consistent lubrication.
Benefits of Dry Plunger Lubricants
A. Reduced Lubricant Quantity
Dry lubricants require significantly lower quantities per casting shot compared to liquid lubricants. This reduction is due to the efficient application process and the fact that there is less waste from dripping, as is common with mineral oils. This leads to cost savings and reduced environmental impact.
B. Cleaner Work Environment
One of the standout benefits of dry plunger lubricants is the cleaner work environment they create. With less lubricant being used and virtually no dripping, workspaces remain dry and free from oil spills. This reduces the risk of accidents and contributes to a more environmentally friendly operation.
C. Improved Aluminum Dross Recyclability
The reduction in oil usage also benefits the recyclability of aluminum dross. Since the dross remains cleaner and less contaminated, it can be more easily re-used and re-melted, improving the overall efficiency of the die-casting process.
D. Enhanced Casting Quality
​​D​ry plunger lubricants help reduce casting defects such as oil stains and porosity. This results in better-quality castings, which is crucial for maintaining high standards in the die-casting industry.
While the adoption of dry plunger lubricants in High-Pressure Die Cast Machines faces challenges, the benefits they offer make them a viable option for the future. From reduced lubricant waste to a cleaner working environment and improved casting quality, dry lubricants present a compelling case for consideration by die casters.
Discover Advanced Lubrication Solutions with Fluid Solutions
Fluid Solutions is a leader in providing innovative lubrication technologies for the die-casting industry. Our range of products includes advanced dry plunger lubricants, designed to meet the specific needs of HPDCMs.
With expertise in cutting-edge lubrication technologies, we offer tailored solutions to help die casters optimize their operations. For more information and to explore our range of products, contact Fluid Solutions today and take the first step towards more efficient and sustainable die casting. Contact Fluid Solutions today at (02) 8370 5928 / (0917) 894 9156 or via email at inquiry@fluidsolutions.com.ph to learn more.