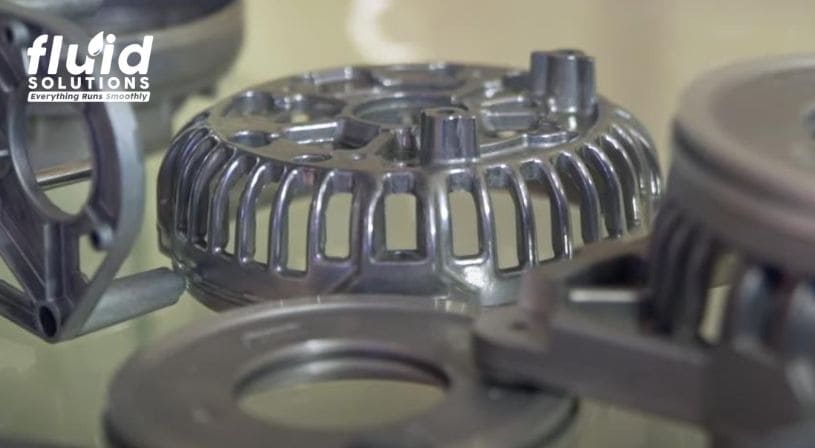
Lubrication is a significant component in the operation of High-Pressure Die Cast Machines (HPDCM). While traditional mineral-based oils and dry plunger pellets are being used, water-based plunger lubricants have also gained attention for their unique properties. This blog explores the advantages and disadvantages of water-based technology, providing a comparison with other lubrication options to help die-casters make informed decisions.
Benefits of Water-Based Plunger Lubricants
A. Improved Casting Quality
One of the significant advantages of water-based plunger oils is their ability to enhance casting quality. These lubricants are often cleaner than their oil-based counterparts, reducing the occurrence of stains and porosity in the final casted products. By minimizing contamination during the casting process, water-based lubricants help produce smoother, cleaner, and less porous castings.
B. Enhanced Safety
Safety is a paramount concern in any manufacturing setting, and water-based lubricants offer a distinct advantage in this regard. Unlike oil-based fluids, which pose a fire hazard, water-based plunger lubricants are significantly less flammable. This reduced risk makes them a safer choice, particularly in environments where high temperatures and molten materials are present.
C. Cleaner Work Environment
Another benefit of using water-based plunger lubricants is a cleaner work environment. Oil spills are a common issue with traditional lubricants, leading to slippery, hazardous work areas. Water-based plunger lubricants, by contrast, result in fewer spills, keeping the workspace cleaner and safer for operators.
Composition and Functionality of Water-Based Lubricants
A. Primary Components
Water-based plunger lubricants are primarily composed of water, which acts as a carrier for other essential functional components. These include emulsified mineral oils, extreme pressure additives, and suspended solid lubricants such as PTFE or graphite. While water itself does not reduce friction, it effectively delivers these lubricating substances to the plunger sleeve or tip, ensuring proper lubrication.
B. Carrier Function
The key function of water in these lubricants is to serve as a carrier medium. It delivers mineral oils, additives, and solid lubricants to the necessary lubrication points. This carrier function reduces spillage and waste, thereby minimizing the risk of casting contamination and contributing to a cleaner production environment.
Application Methods
A. Drip Method
Water-based plunger lubricants can be applied using the drip method, where the lubricant is gradually released either on the retracted tip or onto the sleeve. This method ensures a controlled application, reducing the risk of over-lubrication and the associated issues.
B. Atomization or Spraying
Another application method is by atomization or spraying, where the lubricant is dispersed in fine droplets over the lubrication points. This method allows for more even coverage, ensuring that all critical areas receive adequate lubrication.
Disadvantages of Water-Based Plunger Lubricants
A. Poor Wetting
One of the drawbacks of water-based plunger lubricants is their poor wetting ability. When the lubricant encounters hot surfaces, the water component tends to evaporate quickly, preventing it from spreading effectively into frictional areas. This issue can lead to inadequate lubrication and premature wear. However, using accurately aimed nozzles or multiple nozzles working in tandem can mitigate this problem.
B. Clogging of Nozzles or Lubrication Lines
Another potential issue with water-based plunger lubricants is the clogging of nozzles or lubrication lines. Over time, or under improper storage conditions, the oil phase of the emulsion may separate, forming gel-like substances that can block the lines. To avoid this, it is essential to store these lubricants in a controlled environment and implement an efficient FIFO (First-In, First-Out) inventory management system to maintain their homogeneity and freshness.
Water-based plunger lubricants offer several benefits, including improved casting quality, enhanced die-casting safety, and a cleaner work environment. However, they also come with challenges, such as poor wetting and potential clogging issues. Die casters must weigh these pros and cons when selecting a lubricant for their High-Pressure Die Cast Machines.
Discover Innovative Lubrication Solutions with Fluid Solutions
Fluid Solutions is at the forefront of developing advanced lubrication technologies for the die-casting industry. With a comprehensive range of products, including water-based lubricants, Fluid Solutions provides tailored solutions to meet the specific needs of your operation.
Our expertise in metalworking fluids ensures that you receive the best possible lubrication products for your machines. For more information and to explore our offerings, contact us at (02) 8370 5928 / (0917) 894 9156 or via email at inquiry@fluidsolutions.com.ph today and take the first step toward more efficient and safer die casting.