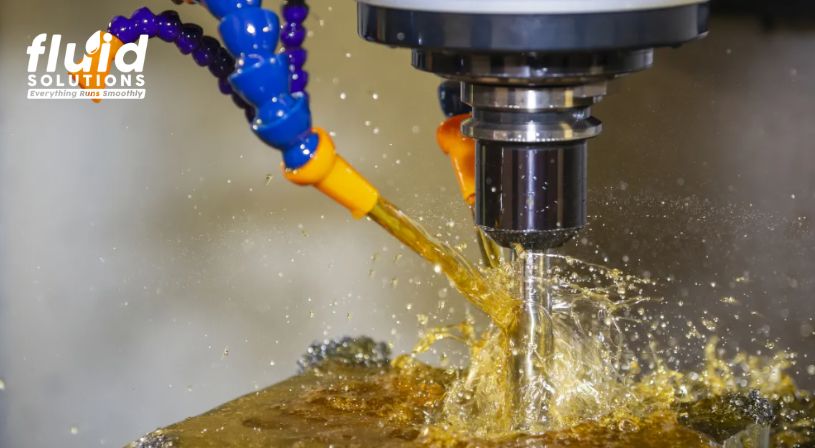
Straight-cutting oils are non-water-miscible lubricants used in metalworking processes, particularly cutting and grinding. These oils are formulated from base oils and performance-enhancing additives to ensure superior lubrication and cooling during machining. Whether you source them from cutting oil manufacturers or a trusted industrial lubricants supplier, understanding their components is crucial for selecting the best product.
In this blog, we’ll dive deep into the components of straight-cutting oils and explore how they achieve optimal performance.
Base Oils
Straight-cutting oils are blended utilizing base oils and performance-enhancing additives. The most common base oils used are paraffinic mineral oils, though there is a preference for naphthenic mineral oils in some cases. In any case, both types of mineral oils are widely used due to their availability in various viscosities, which is the primary factor in neat oil selection.
Here are the common base oils used in straight-cutting oils:
1. Paraffinic Mineral Oils
Paraffinic oils are widely preferred by cutting oil suppliers due to their availability and cost-effectiveness. These oils are known for their high viscosity index, providing stability at varying temperatures, making them ideal for various metalworking applications. They also offer excellent oxidative stability and longer fluid life.
2. Naphthenic Mineral Oils
Naphthenic oils, while less common than paraffinic oils, are favored in specific applications for their lower viscosity and superior solvency. They are better suited for low-temperature environments due to their ability to remain fluid at colder temperatures, ensuring that metalworking processes can continue uninterrupted.
3. Esters
Esters, sometimes used as base oils or added to mineral oils, provide exceptional lubrication, especially in high-stress environments. Esters adhere to metal surfaces and reduce friction more effectively than mineral oils. The addition of esters increases the overall cost of the cutting oils, but offers significant benefits such as improved parts finish, reduced oxidation rates, and lower smoke generation.
Read more about base oils: Base Oils Decoded: Navigating the World of Mineral-Based Lubricants
Additives
Additives are vital to the performance of straight-cutting oils. These compounds enhance the base oils’ natural properties, providing additional benefits to meet the specific demands of metalworking operations. Common additives include:
1. Extreme Pressure (EP) Additives
EP additives are essential for high load cutting operations. Made from sulfur, chlorine, or phosphorus, these additives react with metal surfaces under extreme heat, forming a protective layer on the tool surfaces reducing tool wear and friction. Cutting oil manufacturers carefully formulate EP additives to ensure compatibility with various metals, and care must be taken with non-ferrous metals like aluminum and brass, as these additives can cause staining.
2. Anti-Mist Additives
In high-speed machining, oil mist can become a problem. Anti-mist additives are included to minimize mist formation, creating a safer and cleaner working environment for operators.
3. Anti-Rust Additives
Prolonged exposure to moisture can lead to rust and corrosion on both workpieces and machinery. Anti-rust additives prevent rust formation, ensuring that machined parts remain free of rust and corrosion and extending the lifespan of the equipment.
4. Non-Ferrous Corrosion Inhibitors
To protect non-ferrous metals such as aluminum and copper, non-ferrous corrosion inhibitors are added to cutting oils. These inhibitors prevent chemical reactions that can damage or stain the surfaces of these metals.
5. Colorants
Though they do not influence the performance of cutting oils, colorants are added for easy identification. They help operators distinguish between different types of lubricants used in various machines or processes.
The Synergy Between Base Oils and Additives
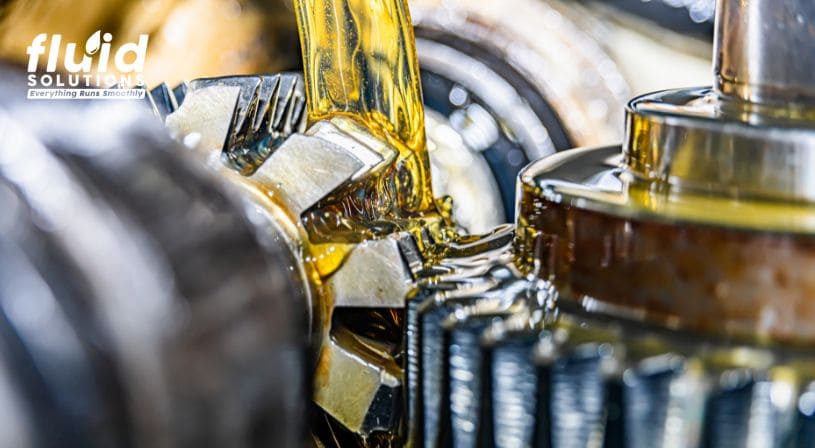
Cutting oil manufacturers and suppliers aim to create products that offer the perfect synergy between the base oils and additives, ensuring that the cutting oil can meet the demands of different metalworking operations.
Metalworking Fluids Manufacturers: A Closer Look at Cutting Oil Suppliers
When selecting the right cutting oil for your operations, partnering with a reputable cutting oil or metalworking fluids manufacturer ensures you receive tailored solutions for optimal performance. An experienced industrial lubricants supplier, like Fluid Solutions, provides high-quality products designed for durability and efficiency, including hydraulic oils, gear oils, synthetic lubricants, and high-temperature greases. With a comprehensive range of lubrication solutions, Fluid Solutions supports your industrial needs. Contact us today at (02) 8370 5928 / (0917) 894 9156 or via email at inquiry@fluidsolutions.com.ph.