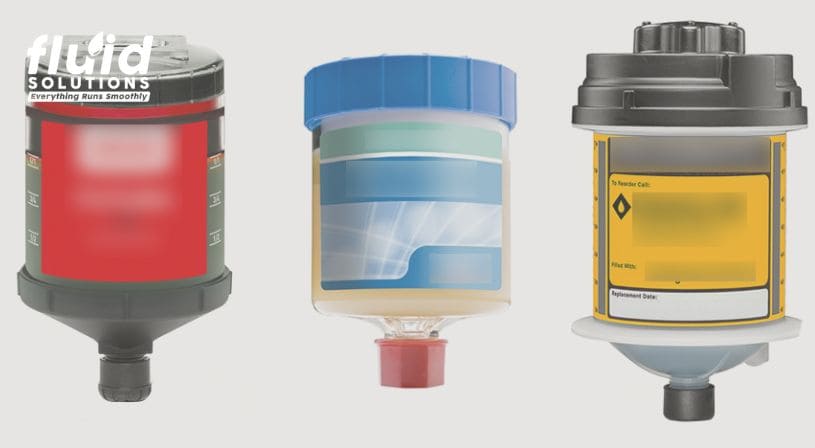
​​​In modern maintenance practices, ​​single point lubricators​​ have become a widely adopted technology in ​​automatic lubrication systems​​. Designed to lubricate a single bearing or mechanical component, these devices offer a more precise and convenient alternative to manual greasing. As industries continue to seek more efficient maintenance solutions, ​​automatic grease lubricators​​ are gaining popularity because of their ease of use and effectiveness. Whether in manufacturing, ​​automotive​​, or ​​heavy equipment maintenance​​, the demand for automated lubrication continues to grow, offering a reliable way to keep components running smoothly without constant manual intervention.​​
Key Takeaways:
- Single-point lubricators are compact, automatic devices for lubricating one bearing or component.
- Ideal for small, stable applications with low lubrication demands.
- Pre-programmable intervals ensure consistent and accurate grease delivery over 1–12 months.
- Benefits include easy installation and minimal manual intervention.
- Limitations: small reservoir size and low back pressure (3–5 bars) make them unsuitable for high-demand or harsh environments.
What are ​​Single Point Lubricators​​?​​
​​Single point lubricators​​ are compact devices, slightly larger than a soda can, designed to lubricate one specific bearing or component. They feature built-in grease reservoirs with volumes ranging from 120 cc to 250 cc. Plastic casings​​​ ​​protect these lubricators​​​ and use either expanding gas or batteries to power the downward motion of a piston, which dispenses grease through a small orifice directly into the bearing​​. Installation is straightforward, as they can easily be screwed into the bearing or mechanical component.​​ The back pressure generated by these devices is typically between 3-5 bars, making them suitable for less demanding applications.
One of the most appealing features of ​​single point lubricators​​ is their ability to pre-program lubrication intervals. These intervals can be set to deliver a precise amount of grease over a specific period, ranging from one month to as long as twelve months, allowing for consistent and accurate lubrication with minimal manual input.​​
​​​Benefits of ​​Single Point Lubricators​​​​
​​​Ease of Use and Installation​​
​​​The small size of single point lubricators makes them incredibly easy to handle and install. Their compact design allows for quick mounting, and the built-in reservoir eliminates the need for external grease cartridges or complicated setups. Maintenance teams can quickly integrate these ​​automatic grease lubricators​​ into their maintenance routines without requiring specialized training or tools.​​
​​​Pre-Programmable Lubrication Intervals​​
​​​One of the key benefits of automatic bearing lubrication with single-point lubricators is setting lubrication intervals in advance. This allows for consistent maintenance with no frequent manual greasing. For instance, if a maintenance team wants to ensure that a bearing receives 0.3 cc of grease per day, the lubricator can be programmed to deliver precise lubrication over a predetermined period of up to twelve months. This pre-programming feature ensures bearings receive the correct amount of lubricants, minimizing the risk of over-lubrication or lubricant starvation.​​
​​​Limitations of Single Point Lubricators​​
​​​Small Reservoir Size​​
​​​While single point lubricators offer many advantages, they have some limitations. One of the most notable is their small reservoir size, which limits their use to smaller bearings and less demanding applications. For larger components or systems that require more lubricants, a centralized lubrication system (CLS) for equipment may be needed more. The typical reservoir capacity of 120 to 250 cc means that frequent refilling or replacing may be required in high-demand environments.​​
​​​Low Backpressure​​
​​The low back pressure generated by single point lubricators, typically between 3-5 bars, limits their effectiveness in certain environments. For example, they may not be suitable for areas that experience extreme temperatures, high humidity, or excessive vibrations. In these conditions, the lubricator may struggle to deliver grease consistently, potentially leading to equipment failures. These devices may also have difficulty dispensing higher viscosity greases, such as ​​NLGI 3​​ or higher.
​​​Considerations for Use​​
When considering using single-point lubricators, maintenance professionals should evaluate the equipment’s specific needs. While these devices are ideal for certain applications, such as small bearings in relatively stable environments, they may not be appropriate for more challenging conditions. It’s important to assess factors like the size of the bearing, the viscosity of the grease required, and the environmental conditions in which the lubricator will be used.​​
​​​In summary, single point lubricators offer several advantages in ​​automatic lubrication systems​​, providing consistent and reliable lubrication for small bearings and components. Their ease of use, compact design, and pre-programmable lubrication intervals make them an attractive option for maintenance teams looking to improve their lubrication practices. However, it’s crucial to consider the limitations of these devices, particularly their small reservoir size and low back pressure, when deciding whether they are the right choice for your specific application.​​
​​Find the Right Lubrication Solution for Your Equipment​​
​​Are you looking for the ideal lubrication solution to keep your equipment running efficiently? Visit ​​our website​​ at ​​Fluid Solutions​​ to learn more about the different ​​automatic lubrication systems​​ and technologies available. As a trusted provider for ​​metalworking fluids manufacturers​​ and industrial operations, we offer a wide range of options, including automatic bearing lubrication and​​ automatic grease lubricators​​. ​​
​​​For more information, contact us at (​​02) 8370 5928 / (0917) 894 9156​​, or email us at ​​inquiry@fluidsolutions.com.ph​​. Our team of experts is ready to assist you in finding the best lubrication technology for your maintenance needs and enhancing the reliability of your equipment!​​