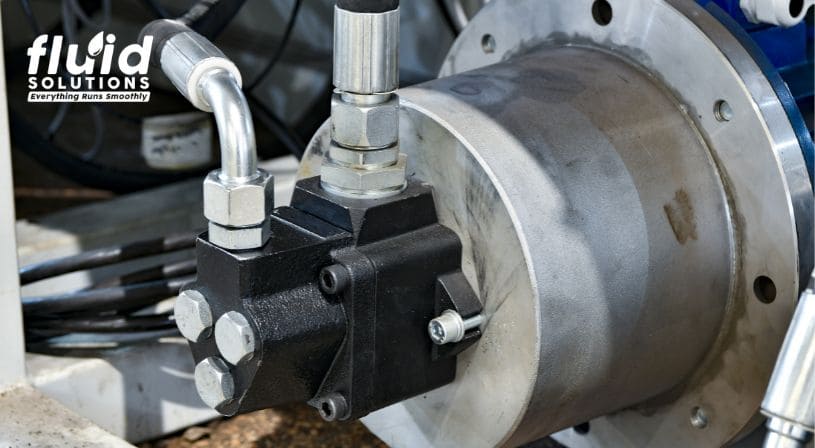
Source: https://www.dreamstime.com/hydraulic-pump-production-oil-station-image215970552
High-pressure die cast machines (HPDCMs) are integral to various industries, and the role of hydraulic oils in their operation cannot be overstated. These machines rely on hydraulic oils to function efficiently, and any disruption in the lubrication process can lead to significant issues. This article explores the critical role of hydraulic oils in HPDCMs, identifies key factors that can cause pump troubles, and highlights the importance of consulting with lubrication experts to maintain optimal machine performance. We will touch on factors like hydraulic fluid price and the importance of choosing the right lubrication equipment.
Use of Hydraulic Oils for High-Pressure Die Casting Machines
Hydraulic oils are the lifeblood of high-pressure die casting machines, ensuring their smooth and efficient operation. These specialized lubricants serve several crucial functions in HPDCMs, including generating the force for clamping die molds and lubricating the lubrication pump.
Generate Force for Clamping Die Molds
In the high-pressure die casting process, precision and accuracy are paramount. Hydraulic oils generate the force required to securely clamp the die molds, ensuring that the casting process proceeds without issues. The ability of hydraulic oils to maintain consistent pressure is essential for producing high-quality cast products, making them a key component in the overall success of the manufacturing process. When selecting hydraulic oils, it’s important to consider not only their performance but also the hydraulic fluid price to balance cost-effectiveness with efficiency.
Lubrication of the Hydraulic Pump
The hydraulic pump is another critical element of the HPDCM. Lubricating the lubrication pump reduces friction between moving components, preventing wear and tear that can lead to pump failures. Proper lubrication is crucial in maintaining the efficiency and reliability of the equipment, preventing costly downtime and repairs. When sourcing lubrication equipment, it’s important to consider the compatibility with your hydraulic oils to ensure optimal performance.
Factors Causing Pump Troubles
Despite the correct specification of hydraulic oils, pump troubles can still occur in high-pressure die casting machines. Two primary factors that contribute to these issues are contaminated and degraded lubricants.
Contaminated Lubricant
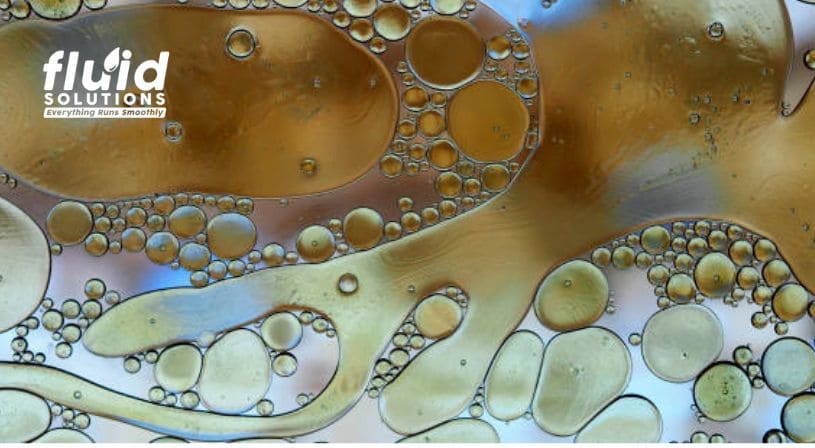
Source: https://www.gettyimages.com/detail/photo/full-frame-of-bubbles-and-drops-of-olive-oil-royalty-free-image/1332881285?adppopup=true
One of the most common causes of pump troubles in HPDCMs is the contamination of hydraulic oils. Contaminants such as dirt, debris, and metal particles can compromise the lubricating properties of the oil. This leads to increased friction, accelerated wear on pump components, and the potential for system failures. The NAS Class 9 contamination grade is the maximum allowable level for hydraulic oil in HPDCMs, and water contamination should be kept to a minimum—ideally, only 0.1%. Proper control of the filtration system and regular monitoring for system leaks are essential to prevent contamination and ensure the continued performance of the lubrication pump.
Degraded Lubricant
Over time, hydraulic oils can degrade because of high temperatures and extended usage. Degraded lubricants lose their viscosity and lubricating properties, exposing pump components to increased friction and the risk of overheating. This degradation can cause pump malfunctions and reduced machine efficiency. It’s crucial to adhere to recommended oil usage intervals, with a good rule-of-thumb being to drain and change the fluid once every 12 months. Failing to do so can lead to the circulation of oxidized, out-of-spec fluids within the pump, causing wear, rust, and corrosion of the metal components in the die cast machines.
Consult with Lubrication Consultants
For businesses that rely on the optimal performance of high-pressure die casting machines, consulting with lubrication experts is essential. Fluid Solutions is a leading provider of hydraulic oils, lubrication pumps, and lubrication equipment, offering valuable insights and expertise to enhance the performance of your HPDCMs.
Lubrication consultants can assess the unique operational conditions of your equipment, recommend the most suitable hydraulic oils, and provide guidance on preventive maintenance practices. By partnering with experts, businesses can make informed decisions that ensure the longevity and efficiency of their die cast machines, ultimately reducing downtime and improving productivity.
Achieve Superior Results with Fluid Solutions’ Lubrication Expertise
Enhance your high-pressure die casting processes with our industry-leading hydraulic oils and lubrication equipment. Whether you need help with selecting the right hydraulic fluids, maintaining your lubrication equipment, or addressing pump troubles, our team is here to help.
Discover our complete range of hydraulic oils, lubrication pumps, and equipment at fluidsolutions.com.ph. For personalized help, contact Fluid Solutions today at (02) 8370 5928 or (0917) 894 9156 or email us at inquiry@fluidsolutions.com.ph. Our experts are here to ensure your operations run smoothly and efficiently.