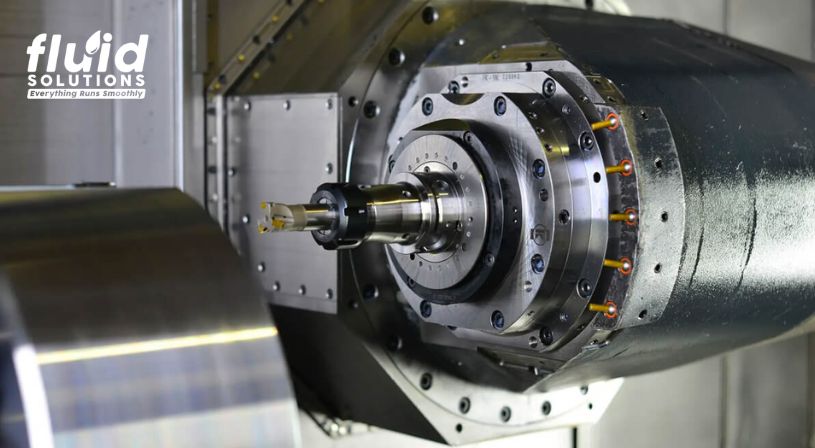
In precision machinery, using the correct lubricant is crucial for maintaining efficiency, minimizing wear, and extending equipment lifespan. The incorrect oil can lead to increased friction, overheating, and premature failure of critical components. This is especially true for high-speed equipment, where even minor inconsistencies in lubrication can significantly impact performance.
One of the essential industrial lubricants are spindle oils. In this article, we will explore what spindle oils are, their key properties, and why selecting the right formulation is vital for maintaining machine efficiency and longevity.
Key Takeaways:
- Spindle oils are low viscosity lubricants designed for high-speed spindles and precision bearings.
- It reduces friction, dissipates heat, and protects against corrosion and contamination.
- These are commonly used in CNC machines, textile equipment, and precision instruments.
- Key properties include low viscosity, high thermal stability, and anti-foaming capabilities.
- Factors in selecting the right spindle oil include viscosity grade, additives, and manufacturer recommendations.
- High-quality spindle oils improve efficiency, prevent overheating, and extend machine’s lifespan.
What are Spindle Oils?
Spindle oils are low-viscosity, highly refined lubricants specifically designed for high-speed spindles and precision bearings. Unlike general-purpose lubricants, spindle oils are formulated to provide excellent fluidity, thermal stability, and anti-foaming properties, making it ideal for applications where excessive friction and overheating can lead to equipment failure.
Primary Functions of Spindle Oils:
- Lubrication: Reduces friction between moving parts, preventing wear and tear.
- Heat Dissipation: Helps regulate operating temperatures by efficiently transferring heat away from critical components.
- Corrosion Protection: Forms a protective layer on metal surfaces, reducing oxidation and extending machine lifespan.
- Contamination Control: Keeps fine dust and debris from accumulating in sensitive areas, preserving machine performance.
Key Features of Spindle Oils:
- Low Viscosity: Provides smooth flow and reduces drag, making it ideal for high-speed applications.
- High Thermal Stability: Maintains performance even under elevated temperatures, preventing oil breakdown.
- Anti-Foaming Properties: Prevents air bubbles from forming, ensuring consistent lubrication, and reducing the risk of machine malfunction.
Spindle Oil Uses
Spindle oils are essential for various industries because of their ability to minimize friction and support smooth operation. Below are some of its uses.
1. High-Speed Spindles in CNC Machines and Lathes
CNC machines, lathes, and other machine tools operate at extremely high speeds, often exceeding 10,000 RPM. These spindles require a lubricant that can:
- Reduce friction to prevent overheating and premature wear.
- Maintain stability at high temperatures to ensure precision cutting.
- Prevent oxidation and corrosion, which can affect spindle performance.
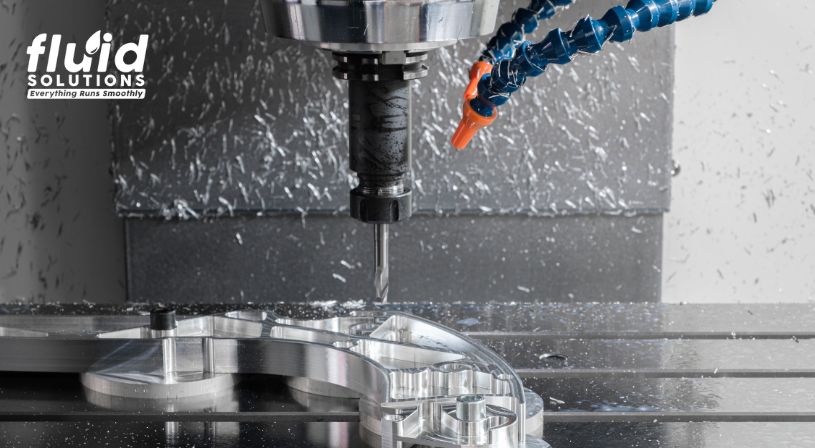
2. Textile and Sewing Machines
Spindle oils are widely used in the textile industry for lubricating sewing machines, looms, and knitting machines. These machines operate continuously at high speeds, requiring a clean, non-staining lubricant that won’t degrade fabric or cause buildup in delicate components. Spindle oils ensure:
- Smooth needle movement and reduced friction in sewing machines.
- Longer operational life for looms and other textile equipment.
- Protection against dust and fiber accumulation, which can affect machine performance.
3. Precision Instruments and Light Industrial Machinery
Precision instruments, such as microscopes, measuring devices, and laboratory equipment, benefit from spindle oils:
- Ultra-low viscosity, ensuring effortless motion and minimal resistance.
- Non-gumming properties, prevent buildup that can hinder movement.
- High purity, making it suitable for delicate applications.
Spindle Oils vs Hydraulic Oils
While both spindle oils and hydraulic oils serve lubrication purposes, they are formulated for different applications:
- Spindle Oils: Designed for high-speed, low-load applications such as precision spindles and bearings. It has low viscosity to ensure smooth operation and minimal friction.
- Hydraulic Oils: Used in hydraulic systems to transmit power and lubricate components under high pressure. It is typically more viscous and contains detergents and anti-wear additives.
Choosing the Right Spindle Oils for Your Machinery
Selecting the correct spindle oil is crucial for maintaining optimal machine performance and extending equipment lifespan. Several factors play a role in determining the best oil for a specific application.
1. Understanding Viscosity Grades and Operating Conditions
Viscosity refers to a lubricant’s resistance to flow, significantly impacting how well the oil can protect moving parts. Spindle oils typically have low viscosity (ISO 2 to ISO 22) to minimize drag and ensure high-speed operation.
- Low-viscosity spindle oils (ISO 2–ISO 10): Best for ultra-high-speed spindles in CNC machines, precision lathes, and textile equipment, where minimal resistance is required.
- Medium-viscosity spindle oils (ISO 15–ISO 22): Suitable for general industrial machinery, including printing presses and sewing machines, where a balance between lubrication and fluidity is needed.
2. The Role of Additives in Performance and Protection
While spindle oils are typically non-detergent and ashless, some formulations include performance-enhancing additives to improve efficiency and longevity:
- Anti-wear additives: Protect against metal-to-metal contact, reducing ear for high-speed spindles.
- Oxidation inhibitors: Prevent the oil from breaking down under continuous use, extending service life.
- Rust and corrosion inhibitors: Safeguard metal components from moisture damage, particularly in humid environments.
- Anti-foaming agents: Reduce air bubbles that can interfere with machinery lubrication and cause performance issues.
3. Manufacturer Recommendations and Industry Best Practices
To achieve optimal results, always follow:
- Manufacturer guidelines – Equipment manufacturers specify the ideal spindle oil type, viscosity, and change intervals. Using an incompatible oil can lead to premature wear, overheating, or equipment failure.
- Industry standards – Look for ISO, DIN, or ASTM certifications, which show high-quality formulations that meet industrial requirements.
- Routine maintenance schedules – Regularly check and replace spindle oil to prevent contamination and degradation, ensuring consistent performance.
Benefits of Using High-Quality Spindle Oils
Using high-quality spindle oil offers the following benefits:
1. Reduced Friction and Wear for Extended Equipment Life
Spindle oils minimize friction between moving parts, reducing wear and tear on critical components. Since spindle systems operate at high speeds, even minor friction can cause premature damage, increased maintenance costs, and reduced productivity.
2. Improved Efficiency in High-Speed Operations
Spindle oils are specially formulated to support high-speed machinery, textile machines, and light industrial equipment.
- Minimized energy loss – Low-viscosity oils reduce internal resistance, allowing machines to run efficiently with less power consumption.
- Optimized speed performance – Proper lubrication helps maintain consistent spindle speeds without drag or unnecessary resistance.
- Enhanced machine responsiveness – Smooth oil flow ensures precision, making it ideal for delicate operations requiring accuracy.
3. Enhanced Cooling and Thermal Stability
Temperature fluctuations in high-speed machinery can lead to oil degradation, viscosity changes, and overheating issues. High-quality spindle oils maintain thermal stability, preventing these problems.
- Prevents overheating – Effective heat dissipation reduces thermal buildup, keeping spindles cool.
- Maintains consistent viscosity – Thermal stability ensures that the oil remains fluid and effective at different temperatures.
- Reduces oxidation risks – High-quality formulations resist oxidation, preventing sludge formation and oil breakdown.
Partner with Fluid Solutions for Expert Spindle Oil Recommendations
Choosing the right spindle oil is essential for maximizing machine performance, longevity, and efficiency. At Fluid Solutions, we provide high-quality spindle oils designed to meet the demanding requirements of various machines and other high-speed applications.
Looking for the perfect spindle oil for your machinery? Contact our experts today at (02) 8370 5928 / (0917) 894 9156 or via email at inquiry@fluidsolutions.com.ph to learn more about our comprehensive products and services.
Social Media Links:
Facebook: https://www.facebook.com/fluidsolutionsinc
LinkedIn: https://www.linkedin.com/company/fluid-solutions-inc