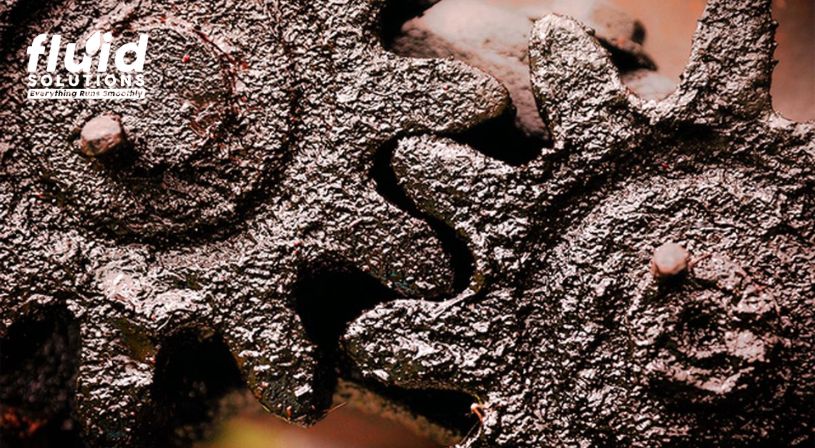
Greases play a crucial role in maintaining the efficiency and longevity of machinery components. High-quality greases ensure smooth operation, reduce friction and protect components from excessive wear, corrosion, and extreme heat. However, not all greases are equal.
Using low-quality greases can lead to severe consequences, including premature equipment failure, increased maintenance costs, and unexpected downtime. Inferior greases may have ineffective additives, degrade faster under high temperatures, or cannot provide adequate lubrication, leading to costly repairs and safety hazards.
In this article, we’ll explore the key characteristics and risks of using low-quality greases and essential tips to help you choose the right greases for your machinery. Making an informed decision can enhance equipment performance, extend service life, and prevent operational failures.
Key Takeaways:
- High-quality greases maintain machinery efficiency, prevent friction and corrosion, and extend equipment lifespan.
- Low-quality greases degrade rapidly under high temperatures, causing equipment damage, increased maintenance, and safety hazards.
- Quality greases exhibit heat stability, consistent texture, proper viscosity, effective additives, and neutral odor and appearance.
- Using inferior or counterfeit lubricants results in costly repairs, unexpected downtime, increased wear and tear, overheating, and operational disruptions.
- Prioritizing quality lubricants ultimately reduces maintenance costs, enhances safety, and ensures reliable machinery operation.
What are Low-Quality Greases?
Low-quality greases are lubricants that lack the necessary ingredients and properties required for effective lubrication. Their subpar performance results from factors such as inferior base oil, unstable thickener, poor oxidation resistance, low dropping point, or inappropriate viscosity for the intended application.
​​​Signs of Low-Quality Greases and What to Look For
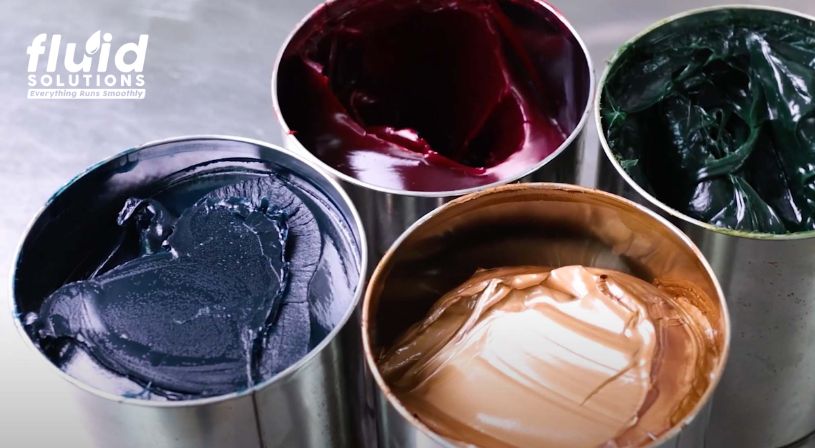
1. Inconsistent Texture and Separation
Low-quality grease often exhibits oil separation or an uneven texture, leading to poor lubrication and reduced effectiveness.
- What to Avoid:
- Grease that appears runny or has oil separation.
- The presence of lumps, clumps, or an uneven texture.
- Rapid thickening or hardening over time.
- What to Look For:
- A smooth and uniform consistency.
- Stable formulation that maintains its structure.
- Proper blending of thickener and base oil.
2. Poor Adhesion and Washout Resistance
If grease fails to stick to surfaces or gets washed away easily, it won’t provide reliable lubrication, increasing wear and tear.
- What to Avoid:
- Grease that easily drips, slings off, or washes away.
- Weak film formation, leading to frequent re-application.
- Poor performance in high-moisture or wet conditions.
- What to Look For:
- Strong adhesion to metal surfaces.
- High resistance to water washout.
- Formulated with additives for enhanced durability.
3. Inadequate High-Temperature Performance
Greases that break down under heat lose their lubricating properties, leading to overheating and equipment failure.
- What to Avoid:
- Grease that melts or liquefies at moderate heat levels.
- Formation of carbon deposits or hardened residue.
- Reduced lubricating properties under high loads.
- What to Look For:
- A high dropping point and thermal stability.
- Ability to withstand prolonged exposure to heat.
- Oxidation-resistant additives to prevent breakdown.
4. Excessive Wear and Component Damage
Poor-quality grease fails to protect metal surfaces, causing increased friction, wear, and costly equipment damage.
- What to Avoid:
- Increased metal-on-metal contact leading to wear.
- Insufficient lubrication causes friction and overheating.
- Presence of contaminants or abrasive particles.
- What to Look For:
- Grease with anti-wear and extreme pressure (EP) additives.
- Protective film formation for extended component life.
- Clean, contaminant-free formulation.
5. Shortened Service Life and Frequent Reapplication
Low-grade grease deteriorates quickly, requiring frequent reapplication, increasing maintenance costs and downtime.
- What to Avoid:
- Grease that breaks down or evaporates quickly.
- The need for frequent re-greasing due to poor retention.
- Increased maintenance costs and equipment downtime.
- What to Look For:
- Long-lasting lubrication with extended service intervals.
- Resistance to oxidation and degradation.
- Efficient performance under various operating conditions.
Temptations and Consequences of Using Low-Quality Greases
Below are the common reasons why users are tempted to choose low-quality greases, along with detailed explanations of how these seemingly convenient choices lead directly to significant negative outcomes.
1. Cost Savings
- Temptation: Low-quality greases often come at lower upfront costs, making them initially attractive for budget-sensitive users.
- Consequence: These greases are rapidly depleted, requiring frequent reapplications. This short lifespan increases maintenance frequency, downtime, and ultimately, costs far exceed initial savings due to increased equipment repairs and reapplications.
2. Short-term Focus
- Temptation: Customers looking for quick solutions may select lubricants without adequate research or evaluation, settling for any available grease without considering suitability or quality.
- Consequence: A quick fix can lead to inadequate lubrication, causing premature equipment wear, component failure, and significant operational interruptions. This short-sighted approach reduces equipment lifespan and reliability, driving up long-term maintenance and operational costs.
3. Lack of Awareness
- Temptation: Customers may unknowingly use counterfeit or low-quality greases, mistakenly believing they purchased genuine, reliable lubricants.
- Consequence: Counterfeit products lack proper formulation and certification, offering minimal protection and causing accelerated wear, overheating, and breakdowns. Customers face unexpected downtime, costly equipment repairs, and safety hazards due to poor-quality lubrication.
Trust Fluid Solutions for High-Quality Greases
Using high-quality greases is essential for maintaining the efficiency and longevity of your machinery. Contact Fluid Solutions today for premium, high-performance greases that ensure superior protection, reduced downtime, and maximum reliability.
Explore our product catalog or consult our lubrication experts today. Contact our experts today at (02) 8370 5928 / (0917) 894 9156 or via email at inquiry@fluidsolutions.com.ph to learn more about our comprehensive products and services. 
Social Media Links:   
Facebook: https://www.facebook.com/fluidsolutionsinc   
LinkedIn: https://www.linkedin.com/company/fluid-solutions-inc