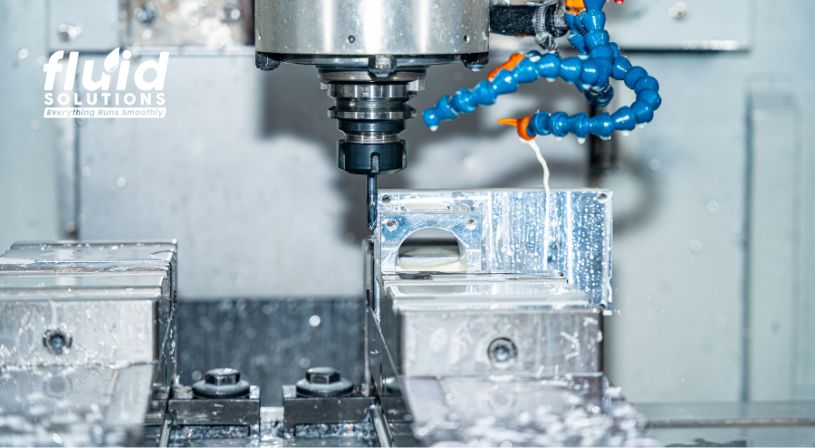
Every six to twelve months, or whenever the water-soluble coolant in the CNC machine sump emits foul odors or shows signs of declining performance, a sump cleanout is typically required. While an uninformed machine operator might be tempted to simply drain the used coolant and refill the system with a fresh mix, this approach can be counterproductive. Without a proper cleaning process, the new coolant can quickly become contaminated with coolant bacteria, fungi, and residues left in the system, drastically shortening its effectiveness.
Importance of Proper Machine Sump Cleaning
To ensure the longevity and performance of the fresh coolant, it is critical to follow a proper machine cleaning process. This involves thoroughly flushing the machine sump after the old coolant has been removed and before refilling with a new charge. Flushing eliminates harmful biological organisms, such as bacteria and fungi, while also removing accumulated metal sludge, slime, and gear oil residues that can cling to the walls, pipes, and sump of the CNC machine.
A clean machine sump is essential to maintaining the operational efficiency of the CNC machine and preventing contamination of the new coolant, which can help to reduce the transmission of bacteria and other harmful substances that degrade the performance of metalworking fluids.
The Flushing Procedure
After draining the old coolant, the following steps outline an effective flushing procedure to prepare the machine sump for a fresh coolant charge:
- Circulate a Flushing Solution. A slightly mild alkaline detergent is recommended for flushing. Used at a 1-2% concentration with water, this solution should be circulated through the sump for two to three hours. The alkaline detergent will loosen trapped soils, metal particles, and other residues while eradicating bacteria and fungi that may have contaminated the system. Some examples of mild alkaline detergents include products planned specifically for industrial applications, which are available through specialized suppliers.
- Hose Down the Machining Area. During the circulation process, it is advisable to use the same detergent solution to hose down the insides of the CNC machining area, preferably with the use of a pressure washer. This ensures that any debris or biological contaminants on the machine walls or within the system’s piping are also removed. The flushing solution’s alkaline properties help dissolve oils and metal sludge that could otherwise lead to system blockages or contamination.
- Alternative Solutions. In the absence of a mild alkaline detergent, the machine operator can use the metalworking fluid itself, diluted to 1-2%, as a substitute. Where the system is severely contaminated, adding 0.01-0.02% biocide to the solution can further enhance its cleaning properties. This additional step ensures that any stubborn bacteria or fungi are effectively neutralized.
- Remove the Flushing Solution. After two to three hours of circulation, drain the flushing solution to ensure that all floating debris and contaminants are removed. This final step is critical for preparing the sump for a fresh charge of water-soluble coolant, as it guarantees that the machine is free from harmful residues that could affect coolant performance.
Charging with Fresh Coolants
Once the sump has been cleaned and flushed, it is ready to be charged with a new mix of water-soluble coolant. Always pre-mix the coolant concentrates with water in a separate container before filling the CNC sump. This pre-mixing step ensures that the coolant reaches the correct concentration and is evenly distributed throughout the system.
By maintaining a clean machine sump and properly charging it with fresh coolant, operators can maximize the coolant’s sump life, reduce contamination risks, and optimize the machine’s overall performance.
Why Machine Cleaning and Maintenance Matter
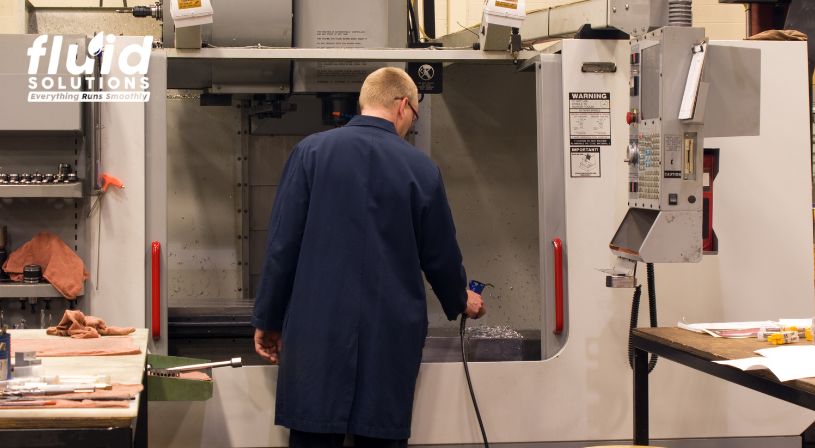
Source: https://www.istockphoto.com/photo/cnc-machine-operator-gm157419351-8408641
Regular machine cleaning and proper sump maintenance not only prolong the lifespan of cutting coolants but also protect the CNC machine from potential damage caused by contaminated fluids. Poor coolant maintenance can lead to excessive bacterial growth, oil separation, and the buildup of residues that can clog or damage the system.
Fluid Solutions: Your Go-To Source for CNC Machine Coolants and Lubricants
Looking for a cutting coolant supplier in the Philippines? Fluid Solutions offer a wide range of lubrication solutions, including water-soluble coolants, gear oils, hydraulic oils, high-temperature greases, and anti-rust oils, designed to meet your business’s needs. Our products are designed to optimize machine performance and help maintain a clean and efficient workspace.
Contact Fluid Solutions today at (02) 8370 5928 / (0917) 894 9156 or via email at inquiry@fluidsolutions.com.ph for expert advice on maintaining your CNC machines and ensuring long-lasting sump life for your cutting coolants.