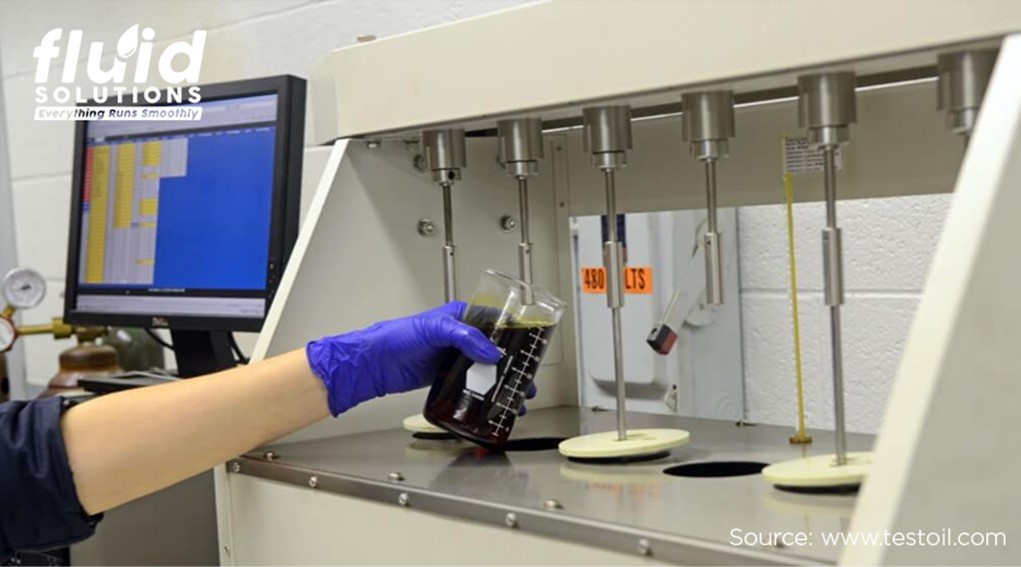
Rust, the arch-nemesis of machinery, can wreak havoc on industrial equipment, leading to costly repairs and downtime. In this article, we delve into the world of rust protection testing and explore how lubricants play a crucial role in combating corrosion.
What is a Rust Protection Test?
Before delving into the specifics of the ASTM D665 method, let’s understand the purpose of rust protection testing. This test serves as a litmus test for a lubricant’s ability to shield steel materials from rust formation, ensuring the longevity of machinery components.
Importance of Rust Protection
Rust formation not only compromises the aesthetic appeal of machinery but also undermines its structural integrity. By conducting rust protection tests, stakeholders in various industries can proactively address corrosion issues, thereby extending the lifespan of equipment and reducing maintenance costs.
Advancements in Rust Protection Technology
With advancements in lubricant formulation and additive technology, manufacturers are continually striving to enhance rust protection capabilities. Cutting-edge lubricants are engineered to provide superior protection against corrosion, even in harsh operating environments, thereby prolonging machinery lifespan and improving performance.
Application Across Industries
Rust protection testing finds application across diverse industries, including automotive, manufacturing, aerospace, and marine sectors. By ensuring effective rust prevention measures, businesses can safeguard their assets, minimize downtime, and maintain operational efficiency.
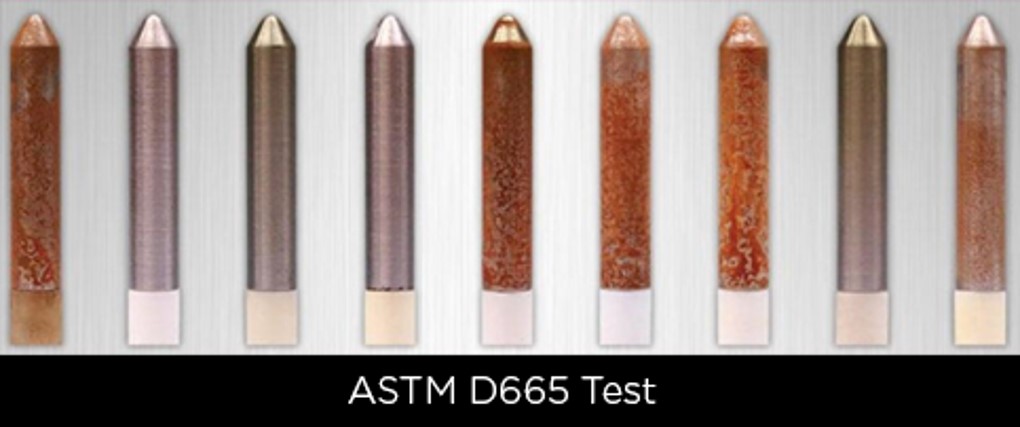
The ASTM D665 Test Process
Various rust protection tests are performed on ferrous or steel materials, to provide guidance on a lubricant’s capability to retard rust formation. A common test based on ASTM* D665 calls for the immersion of cylindrical steel specimens into a bath with the test lubricant. Over 4 or 24 hours, seawater is introduced to the bath to accelerate rust formation. The steel specimen should exhibit no rust formation whatsoever after the test, to gain a “pass” rating.
As almost all machinery components contain steel, this test is a very useful guide to the maintenance or lubrication practitioner.
*American Society for Testing and Materials
Interpreting the Results
Discover the criteria for passing the rust protection test and gain insights into the pass/fail rating system. A thorough understanding of the test results empowers maintenance and lubrication practitioners to make informed decisions regarding lubricant selection.
Effective Application Methods for Rust Preventive Oils (RPO)
DID YOU KNOW that the application method for Rust Preventives Oils (RPO) can affect rust protection performance?
Application methods can significantly impact the performance of Rust Preventive Oils (RPO). While brushing and spraying are effective means to apply RPO’s, the dipping or bath method is deemed most effective as it endures full coverage on the workpiece. In addition, a dip or bath system provides the thinnest possible effective film on the metal surface, as one can suspend the workpiece for a few seconds after dipping, allowing excess film to drip back into the tank.
Partnering with Fluid Solutions for Rust Protection
Rust protection testing is not merely a checkbox; it’s a vital aspect of machinery maintenance and longevity. In the quest for optimal rust protection solutions, partnering with trusted lubrication experts is paramount. Metalworking fluids manufacturers like Fluid Solutions offer a comprehensive range of industrial lubricants and tailored solutions designed to meet specific rust prevention needs. By partnering with Fluid Solutions, an industry leader in lubrication solutions, you can ensure superior rust protection and optimal machinery performance. Contact Fluid Solutions today at (02) 8370 5928 / (0917) 894 9156 or via email at inquiry@fluidsolutions.com.ph today for expert advice and a wide range of rust-preventive lubricants tailored to your specific needs. We offer various industrial lubrication products like Food Grade Oils and Greases, High-Performance Greases, Specialty Lubrication, Maintenace Equipment, and Metalworking Fluids.