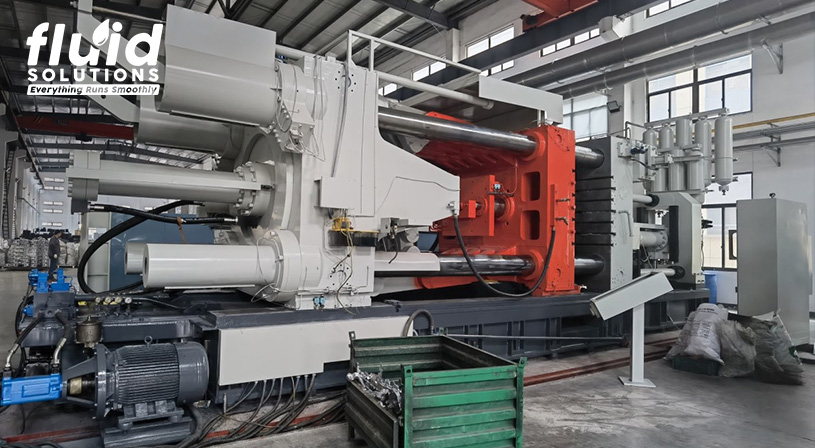
Source: https://depositphotos.com/photo/industrial-landscape-factory-view-dashboard-control-panel-metal-cutting-machine-360331970.html
Reducing scrap rates in die casting is crucial for cost efficiency and quality. Choosing the right die casting lubricants from reputable metalworking fluids manufacturers is ​one of the important factors​​ to avoid errors and ensure smooth mold release. This directly lowers scrap rates and enhances production ​quality and quantity​, resulting ​to a​ more efficient manufacturing​ process​.
Die casting often faces scrap issues because of defects and poor mold release. Using effective ​and quality ​die casting lubricants helps address these issues, leading to better quality, reduced scrap rates, and more efficient production.
Lubricants Impacting Scrap Rates
The Role of Lubricants in Machining
Lubricants serve several essential functions in machining:
- Reducing Friction: By forming a thin film between the tool and workpiece, lubricants decrease the friction, resulting in smoother operations and less tool wear.
- Cooling: Lubricants help dissipate the heat generated during machining, preventing thermal damage to both the tool and the workpiece.
- Removing Debris: Effective lubricants facilitate the removal of metal chips and other debris from the cutting area, maintaining a clean interface for precision machining.
Impact on Scrap Rates
The quality of lubrication can significantly influence scrap rates in manufacturing processes:
- Improved Surface Finish: Adequate lubrication leads to a better surface finish by minimizing friction and preventing surface defects. This reduces the likelihood of parts being rejected due to poor finish.
- Tool Life Extension: Proper lubrication extends the life of cutting tools by reducing wear and thermal degradation. Longer tool life translates to more consistent part quality and fewer instances of tool-related scrap.
- Dimensional Accuracy: Consistent lubrication ensures stable machining conditions, which helps maintain tight tolerances and dimensional accuracy. Parts are less likely to be scrapped due to dimensional discrepancies.
Role of Die Casting Lubricants
There are different die casting lubricants, namely Die Cast Machine Lubricant, Die Cast Release Agents, Plunger Lubricants, Auxiliary Lubricants and Coating.
- Die cast machine lubricant is a special oil that reduces friction between moving parts, keeping die casting machines running smoothly.
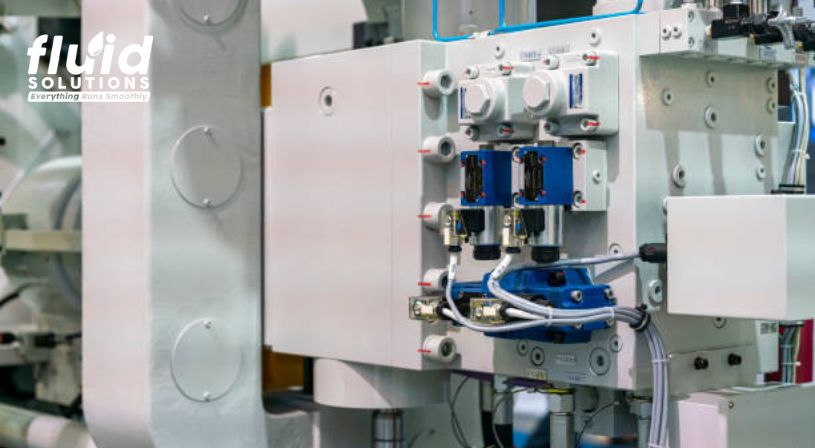
Source: https://depositphotos.com/photo/close-electric-solenoid-valve-hydraulic-system-control-high-pressure-die-395100410.html
- Die last release agents are compounds applied to mold surfaces to make it easier to remove castings, reduce sticking, and improve production efficiency.
- Plunger lubricants are special lubricants designed for die casting machines. They lubricate the plunger tip and sleeve, ensuring smooth injection of metal into the mold cavity.
- Auxiliary lubricants and coatings are additional compounds that assist in die casting operations, mold release, and protecting tooling surfaces from wear and corrosion.
Reducing Scrap Rates with Die Casting Lubricants
Lubricants improve die casting by reducing friction, ensuring smooth mold release, and controlling temperatures, minimizing die casting defects. They prevent sticking, reduce wear on molds, aid in metal flow, and maintain consistent temperatures for quality castings and efficient production processes.
Die casting lubricants can help reduce high scrap rates in several ways, as listed below:
- Enhanced Mold Release: Die casting lubricants with enhanced mold release properties prevent sticking, lowering scrap rates by ensuring defect-free release of cast parts from molds.
- Temperature Regulation: Die casting lubricants help control temperature, preventing issues like porosity and thermal cracks, which reduces scrap rates.
- Improved Surface Quality: Die casting lubricants enhance surface quality, reducing scrap rates and the need for post-processing by creating smoother castings.
- Porosity Reduction: Die casting lubricants reduce porosity by minimizing gas entrapment, leading to lower scrap rates. Techniques include using lubricants with degassing agents, improving mold venting, and optimizing die temperature and pressure for smoother metal flow.
​​Best Practices for Lubricant Use​​​
​​​To recap, be reminded that using die casting lubricants is crucial for lowering scrap rates, ensuring cost efficiency, and high-quality products. Proper lubrication minimizes flaws, improves mold release, and maintains consistent temperatures, reducing waste and downtime. Best practices, such as selecting the right lubricants, optimizing application processes, and monitoring performance, lead to optimal industrial outcomes.​​
​​​Here are some of the best practices for using die casting lubricants:​​​​
- ​​​​Choosing Lubricants​​: Consider die material compatibility, operating conditions, and application method when selecting die casting lubricants. Opt for environmentally friendly options with high performance, minimal residue, and compatibility with post-casting processes. Cost-effectiveness, supplier support, and certifications are also important for optimal performance, longer tool life, and reduced scrap rates.​​​
- Application Techniques​​: Use controlled spraying, brushing, or dipping for even coverage on mold surfaces, ensuring consistent and effective lubrication. Properly dilute sprays and regularly inspect equipment to maintain optimal distribution and performance.​​​
- ​​​​Maintenance and Monitoring​​: Regularly clean and inspect molds to remove residue and ensure proper lubricant adherence. Monitor die temperatures, lubricant consumption, and mold release effectiveness for early issue detection. Scheduled replenishment and equipment calibration minimize downtime and maintain performance consistency.​​​
- ​​​​Innovative Solutions​​: Embrace eco-friendly lubricants and smart process controls to boost efficiency and sustainability in die casting operations, benefiting both businesses and the environment.​​​
Reduce Scrap Rates with Fluid Solutions’ High-Performance Die Casting Lubricants
Fluid Solutions High-Performance Die Casting Lubricants are crafted to significantly cut scrap rates and boost efficiency in die casting. Our lubricants are carefully formulated to minimize defects, ensure smooth mold release, and maintain stable temperatures, leading to better-quality castings with fewer flaws. Manufacturers benefit from our innovative lubricants that enhance metal flow and reduce downtime.
With our expertise in die casting lubrication, we tailor solutions to meet specific production needs, from selecting the right lubricants to optimizing application methods and troubleshooting. We provide comprehensive support to help manufacturers achieve their production goals effectively.
At Fluid Solutions, we prioritize innovation and sustainability by offering eco-friendly lubricants that meet environmental standards without compromising performance. Our focus on research and development ensures our lubricants stay ahead in industry advancements, helping firms stay competitive while reducing environmental impact.
Partnering with Fluid Solutions means gaining access to high-quality lubricants supported by experienced assistance. This allows manufacturers to streamline operations, cut scrap, and improve efficiency and profitability in their die casting processes.
Contact Fluid Solutions today  at (02) 8370 5928 / (0917) 8​9​4 9156 or via email at inquiry@fluidsolutions.com.ph
Social Media Links:
Facebook Page: https://www.facebook.com/fluidsolutionsinc
LinkedIn: https://www.linkedin.com/company/fluid-solutions-inc