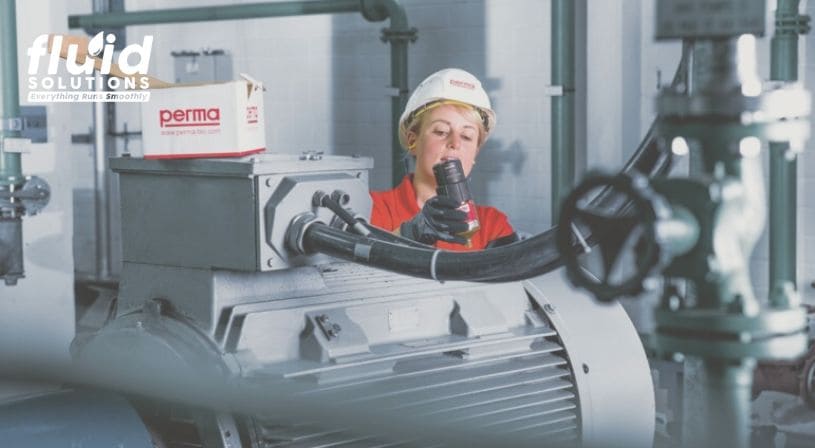
Image Source: https://perma-tec.becdn.net/_Resources/Persistent/7/b/7/7/7b77c098214313a7d3d5b6f2fb4a85a927ec5e92/_31Q6232_MIN-771×578.jpg
In recent years, the automatic grease dispensing system has gained significant traction among maintenance professionals across various industries. This method provides a more efficient, reliable alternative to manual greasing with a grease-gun, which often leads to several maintenance challenges. As the need for higher equipment reliability grows, particularly in industries like manufacturing, mining, and transportation, maintenance teams are turning to automatic greasing systems to improve equipment performance and reduce costs.
The benefits of switching to automatic lubrication are many, especially when compared to the drawbacks of traditional manual lubrication methods. With grease suppliers in the Philippines and other countries offering advanced solutions, it’s becoming easier for companies to transition to automatic systems. In this article, we’ll discuss the benefits of automatic​ lubrication​ systems​ over manual lubrication​, and​ the​ important considerations for those looking to upgrade their maintenance practices.
Key Takeaways
- Automatic lubrication systems deliver consistent, precise grease application, eliminating over- and under-lubrication.
- They reduce contamination risks by using sealed systems, preserving lubricant integrity.
- Enhance safety by allowing remote lubrication in hard-to-reach or hazardous areas.
- Minimize the risk of using incorrect grease, protecting equipment from failure.
- Though initial investment is required, they offer long-term savings through reduced downtime and extended equipment life.
Disadvantages of Manual Lubrication
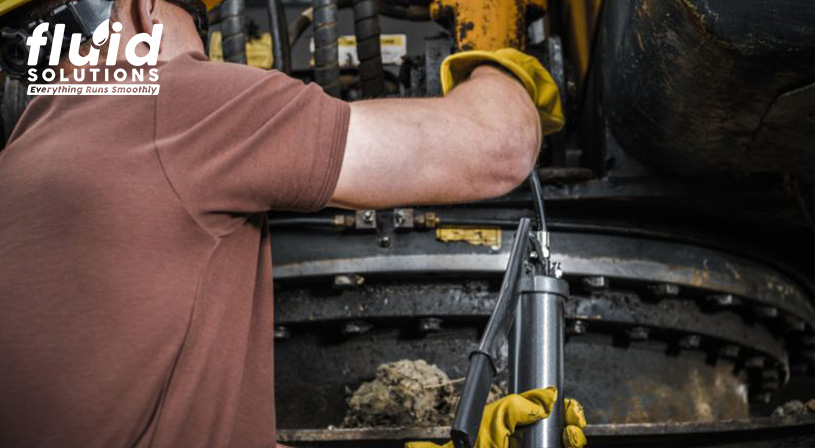
​​​ ​Image Source: https://www.vecteezy.com/photo/24528442-industrial-machine-technician-pumping-in-the-grease​
Despite being a common practice, manual lubrication has several drawbacks that can lead to equipment failure, increased maintenance costs, and production downtime.
Over-Lubrication and Lubricant Starvation
One of the key issues with manual lubrication is the difficulty in maintaining the correct amount of grease in bearings. Maintenance personnel often must rely on experience or guesswork to determine the right quantity of lubricant. This can lead to over-lubrication or lubricant starvation, both of which can have detrimental effects on equipment. Over-greasing creates excess heat, leading to the degradation of the grease, while under-greasing results in insufficient lubrication, causing premature bearing failures. Both scenarios can cause equipment malfunctions and costly downtime.
Automated systems eliminate this guesswork, ensuring that the right amount of grease is applied at the right time. For example, in an automatic greasing system, lubricators can be programmed to release a precise amount of grease—such as 0.3 cc per day for a single bearing—ensuring that grease levels remain consistent and optimal.
Contamination Risks
Manual lubrication is also prone to contamination, which can significantly degrade the quality of the grease. In an industrial environment, solid contaminants such as dust, dirt, and metal particles, as well as moisture, can enter the lubricant during manual application. This contamination speeds up wear in bearings and other components, shortening their service life. Improper automation device maintenance can exacerbate contamination issues, leading to more frequent maintenance requirements and downtime.
Automatic systems use sealed grease lines that transport the lubricant directly from the pump to the bearing. These systems prevent external contaminants from entering the grease, reducing the risk of component wear, and extending the lifespan of the equipment.
Use of Incorrect Grease
Another common issue with manual lubrication is the use of the wrong type of grease. Maintenance personnel may inadvertently use the incorrect grease for a specific application, particularly when there is no organized system for classifying and identifying lubricants. This can cause catastrophic damage to components, leading to equipment failure, production delays, and expensive repairs. For instance, using the wrong lubricant could cause problems when comparing manual transmission fluid vs. automatic transmission fluid requirements, highlighting the need for proper lubrication management.
An automatic lubrication system eliminates this risk by ensuring that the correct grease is always delivered to the right component. With an automatic grease dispensing system, the possibility of using the wrong grease is minimized, as the system is programmed to apply the correct lubricant based on the machine’s specifications.
Benefits of Automatic Lubrication Systems
Consistent Lubrication
One of the most significant advantages of automatic lubrication is the consistency it provides. In manual lubrication, variability is common—some components may receive too much grease, while others may receive too little. In contrast, an automatic grease machine is designed to apply precise amounts of lubricant at fixed intervals, eliminating both over-lubrication and under-lubrication. This consistency helps prevent equipment failures and extends the lifespan of critical components.
Reduced Contamination
As mentioned earlier, contamination is a major concern in manual lubrication. However, automatic systems minimize this risk by using sealed grease lines protected from external contaminants. This reduces the likelihood of solid contaminants or moisture entering the grease and damaging the equipment. In doing so, the system not only preserves the integrity of the lubricant but also ensures that it is applied correctly, further improving the reliability of the machinery.
Improved Safety and Accessibility
In industrial environments, some lubrication points may be in hard-to-reach or hazardous areas. Manual lubrication in these situations can pose safety risks to maintenance personnel. An automatic greasing system solves this issue by allowing remote lubrication, reducing the need for workers to access dangerous locations. This is valuable for machines that cannot be stopped for maintenance because of high production demands. Automatic lubrication ensures that these machines receive consistent lubrication with no manual intervention, improving both safety and operational efficiency.
Considerations for Implementing Automatic Lubrication
While the benefits of an automatic grease machine are clear, it’s important to consider the initial investment required. Automatic lubrication systems often require upfront costs, but these are quickly offset by the long-term savings in reduced downtime, extended equipment life, and lower maintenance costs. Maintenance managers must calculate the return on investment (ROI) by considering factors such as the cost of repairs, production losses, and the potential safety risks associated with manual lubrication.
Proper planning is essential to ensure the system is tailored to the facility’s specific needs. This includes selecting the right type of automatic lubricator for the application and ensuring compatibility with existing equipment. Grease suppliers in the Philippines can offer expert advice on choosing the right solution for your facility.
Switching to an automatic greasing system can dramatically improve maintenance efficiency, reduce contamination risks, and enhance the overall reliability of your equipment. While there is an initial investment involved, the long-term benefits in terms of reduced maintenance costs, increased equipment lifespan, and improved safety make it a worthwhile investment for any industrial operation. Automatic lubrication provides consistent, precise lubrication that eliminates the guesswork and contamination risks associated with manual greasing, ensuring that your machinery operates at peak efficiency.
Discover the Right Automatic Lubrication Solution for Your Needs
Upgrade your lubrication methods today by exploring the various automatic grease dispensing systems available on the market. Visit our website at Fluid Solutions to learn more about our comprehensive range of lubrication solutions. As a trusted grease supplier in the Philippines, we can help you choose the best system for your needs.
Contact Fluid Solutions at (02) 8370 5928 / (0917) 894 9156, or via email at inquiry@fluidsolutions.com.ph today to improve your automation device maintenance and ensure the optimal performance of your equipment!