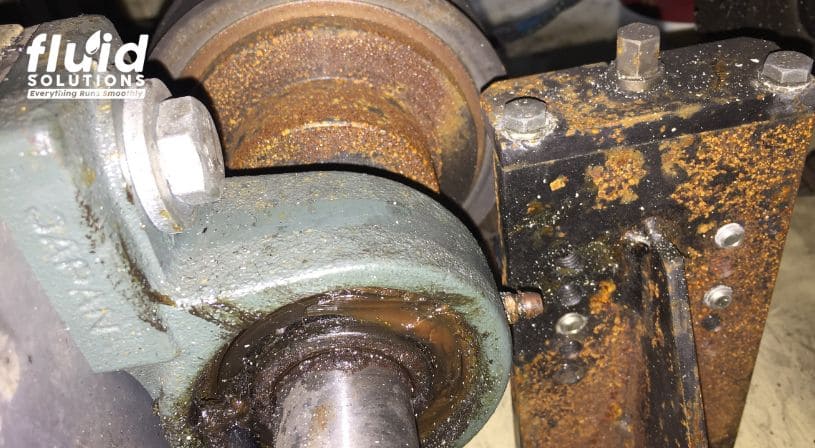
Rust in ferrous (iron-based, steel-type) metals after machining and grinding is a common and costly problem. Many companies invest significant working hours in reworking rusted parts, while others scrap rusted pieces entirely. Either way, rust costs businesses money and time. While there are many potential causes for part rust, this article will focus on those related to the use of water-based coolant for metal machining and grinding.
Common Causes of Rust in Machining and Grinding Fluids
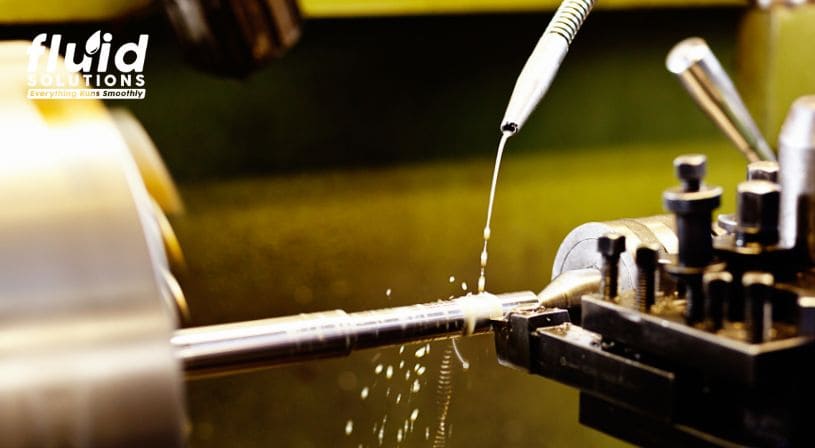
Here are the most common coolant-related factors that contribute to rust formation and how you can avoid them:
- Coolant Concentration
It may seem obvious, but running the coolant at too low a concentration is a common cause of rust. When the coolant’s concentration is too low, both the oil level and the anti-rust additives in the emulsion are proportionally reduced. Since oil inhibits rust, a low concentration will not provide sufficient protection for the workpieces.
Solution: Emulsions and semi-synthetics should ideally be run at concentrations greater than 5%, while synthetics for grinding should be at over 3%. By maintaining these concentration levels, you can ensure the coolant is doing its job to prevent rust.
- Low pH Levels
Coolants should have a pH level of 8.9 or higher to effectively deter rust and bacteria. If the pH drops below this threshold, the coolant becomes less effective at preventing rust, and bacterial growth can speed up.
Solution: Monitor pH levels regularly and top up the fluid as needed to boost pH. Consider adding a pH booster to maintain the desired alkaline environment, which helps prevent rust.
- Bacteria in the Coolant
Bacteria not only produce the unpleasant odors that operators dislike, but they can also cause rust by depleting the functional additives in the coolant, such as anti-rust agents. When bacteria proliferate, these essential additives are consumed, leaving the coolant less capable of protecting metal surfaces.
Solutions:
- Always run the coolant at the right concentrations to maintain sufficient levels of biocides that prevent bacterial growth.
- Keep the pH above 8.9 to deter bacteria.
- Remove metal chips and debris from the bottom of the sump regularly, as bacteria thrive in these areas.
- Use clean containers and fluid handling devices to avoid introducing bacteria into the system.
- Excessive Tramp Oil
Tramp oil, which leaks from slideways and hydraulic systems, can contaminate the workpiece and lead to rust formation. Although oil itself doesn’t directly cause rust, tramp oil is often oxidized and no longer provides protection against rust. Tramp oil can also create a barrier that prevents the coolant from doing its job effectively.
Solution: Regularly skim the tramp oil from the coolant. You can do this manually using a dipper or foam, or with an automatic belt skimmer to ensure efficient tramp oil removal.
Additional Factors Leading to Rust
Beyond coolant-related issues, there are other factors that can contribute to rust formation on metal parts:
- Acidic environments: Machining near pre-treatment processes that use acids can create an acidic atmosphere that contributes to rust.
- High humidity: Excessive moisture in the air can speed up rust formation, especially if parts are not protected with rust-preventive oils.
- Prolonged storage: Storing machined parts for too long without applying anti-rust oils can cause rust, particularly in humid environments.
- Water quality: Poor water quality, with high levels of dissolved solids, can also reduce the effectiveness of the coolant in preventing rust.
The Importance of Proper Coolant Management
By addressing these factors, you can reduce the risk of rust and ensure that your operations run smoothly. Monitoring coolant pH and concentration, as well as ensuring clean handling practices, will not only protect your metal parts but also prolong the life of your equipment.
Rust prevention in machining is an ongoing process, but with proper care and attention, rust-related downtime and scrap costs can be minimized.
Fluid Solutions: Your Partner in Rust Prevention and Coolant Optimization
Struggling with rust or coolant issues in your operations? Fluid Solutions has you covered. We offer a comprehensive range of high-performance lubrication products, from water-soluble cutting fluids to anti-rust oils, grease lubricants, and synthetic lubricants. Whether you’re looking to prevent rust, improve coolant efficiency, or extend the life of your equipment, our solutions are designed to keep your operations running smoothly.
Get in touch with Fluid Solutions today at (02) 8370 5928 / (0917) 894 9156 or email inquiry@fluidsolutions.com.ph to discuss how we can help optimize your machinery’s performance and safeguard against rust and corrosion.