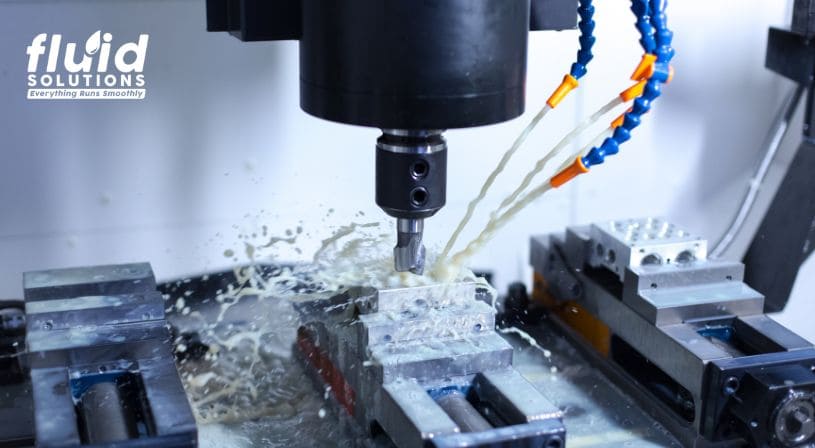
Metalworking fluids (MWFs), also known as coolants, are crucial for machining and grinding operations, offering lubrication, cooling, and efficient chip removal. Metalworking fluids manufacturers often emphasize that, unlike semi-synthetic and mineral oil-based fluids, fully synthetic MWFs are entirely petroleum-free. This unique formulation provides superior cooling, making it an optimal choice for high-speed operations
In addition, fully synthetic fluids reduce harmful residues, creating a cleaner work environment. Their durability in tough conditions makes them an excellent choice for industries focused on maximizing productivity while maintaining sustainable practices, especially when selecting the best grease for heavy equipment.
What are Fully Synthetic Metalworking Fluids?
Fully synthetic metalworking fluids (MWFs) are water-based compositions containing water, synthetic lubricants, and additives, which provide certain advantages over traditional fluids.
One of the primary advantages of fully synthetic MWFs is their ability to reduce residue, which results in a cleaner operation and reduced downtime for maintenance. Fully synthetic fluids usually outperform semi-synthetic and mineral oil-based fluids in terms of both performance and environmental effects. Semi-synthetic fluids may contain petroleum, resulting in greater residue and lower thermal stability. While mineral oil-based fluids are often cheaper, they typically have poor lubricating properties and can negatively impact the environment because of their petroleum content. In contrast, fully synthetic MWFs offer an excellent option for manufacturers seeking high performance with minimal environmental impact.
Machine Applications That Benefit from Fully Synthetic Metalworking Fluids
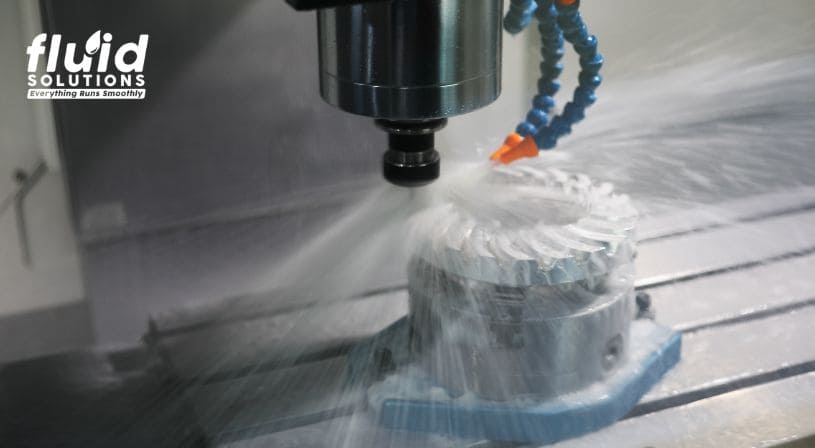
Fully synthetic metalworking fluids are ideal for high-speed machining and grinding tasks, particularly those that require high-performance lubrication, effective cooling, and low residue to maintain efficiency and extend tool life.
A. CNC Machining Centers
They are applicable for machining tasks like CNC milling, turning, and grinding. These applications demand high-performance lubrication, effective cooling, and low residue to maintain efficiency and extend tool life.
B. Grinding Operations
Fully synthetic metalworking fluids are well-suited for grinding processes like surface, cylindrical, and centerless grinding, where precision and high surface quality are essential. They offer excellent cooling and lubrication, which helps reduce thermal deformation and ensures part accuracy. This makes them especially valuable for industries producing high-precision components such as bearings, camshafts, and medical implants
C. Electro-Discharge Machining (EDM)
Lastly, they are valuable for electro-discharge machining (EDM), where precision is essential for working with hard metals and alloys. These fluids enhance conductivity and cooling, improving both precision and efficiency in the machining process. They are particularly beneficial in tool and die fabrication and mold manufacturing, where accurate machining of hard metals is necessary.
When Not to Use Fully Synthetic Metalworking Fluids
While fully synthetic metalworking fluids offer numerous benefits, there are situations where they may not be the best choice, particularly in applications requiring a fluid that requires higher lubrication. Knowing these scenarios can help ensure optimal machining performance.
A. Heavy-Duty Operations Requiring Extreme Lubricity
For heavy-duty machining applications that require extreme lubrication, such as slow-speed, high-torque operations, semi-synthetic fluids, or emulsions might be a better choice than fully synthetics. These fluids can create thicker films that reduce friction and wear under heavy loads. Their ability to adhere to surfaces ensures consistent lubrication, even in tough conditions, making them ideal for gearboxes and large hydraulic systems. It’s crucial to understand the specific needs of each operation, as selecting the right fluid can significantly affect equipment performance and longevity. Such arduous operations include drilling, broaching, and tapping
B. Certain Material Compatibility Issues
Certain materials, such as rubber and some plastics, may not react well to fully synthetic metalworking fluids, as these fluids can cause degradation. In processes involving these materials, semi-synthetic or mineral oil-based fluids are often more suitable due to their better compatibility and gentler nature.
Optimize Your Machining with Fluid Solutions’ Fully Synthetic Metalworking Fluids
Fully synthetic metalworking fluids have many benefits, such as better cooling, less residue, and improved lubrication. These advantages are especially significant for high-speed operations, grinding, and CNC machining, where efficiency and precision are vital.
Fluid Solutions offers high-performance fully synthetic, semi-synthetic, and emulsion fluids engineered for a wide range of machine applications. Our solutions are built to withstand the rigorous demands of industries such as automotive and aerospace, ensuring the smooth, efficient operation of your machinery. We put performance and dependability first with solutions made especially for CNC machining, grinding, and high-speed operations.
Reach out to Fluid Solutions. for expert advice and tailored product recommendations. Our experienced staff is prepared to help you identify the ideal fluid solution to fulfill your unique requirements, increasing output and extending the life of your machinery.
Contact us at (02) 8370 5928 / (0917) 894 9156 or via email at inquiry@fluidsolutions.com.ph.