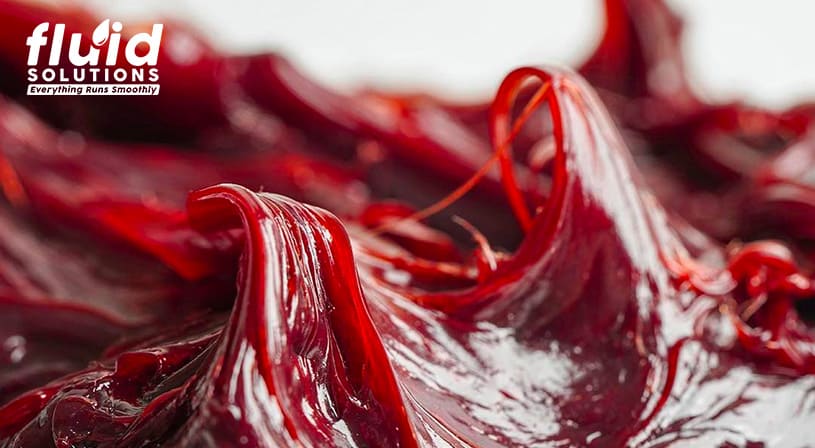
Grease is a lubricant comprising base oil, thickener, and additives, serving diverse applications from automotive engines to industrial machinery. ​Grease thickeners are substances added to lubricating greases to enhance their viscosity and consistency. These thickeners contribute to the overall stability of the grease, ensuring it stays in place and provides effective lubrication even under challenging operating conditions.​
This blog explores the role of grease thickeners, their impact on grease performance, and the various types used across different applications.
Impact of Thickeners on Grease Performance
Thickeners give greases their pasty, non-flowing consistency. Although they rarely reduce friction or provide lubrication, they contribute significantly to the overall performance of the grease. Grease thickeners can affect the following characteristics:
Consistency: Thickeners determine the grease’s stiffness, affecting its ability to adhere to surfaces versus its ease of pumpability. Higher-consistency grease is more resistant to releasing lubricating fluid under force, while lower-consistency grease releases fluid more readily.
Water and Steam Resistance: The type of thickener influences how well grease resists water washout and maintains integrity in high-moisture or steam-rich environments.
Temperature Performance: Thickeners dictate the dropping points and low-temperature behavior, ensuring operational reliability across a wide range of temperatures and resistance to steam.
Chemical Resistance: Grease thickened with suitable materials exhibits resistance to acids, alkalis, and other chemical agents, prolonging equipment life in chemically harsh environments.
Corrosion Protection: Effective thickeners contribute to the grease’s ability to protect metal surfaces from corrosion, which is critical for equipment longevity and performance.
Grease Stability: Thickeners play a vital role in maintaining grease stability over time, preventing undesirable changes in consistency and structure that could impair performance.
Get the correct lubrication solutions for your industry with Fluid Solutions. As a leading grease supplier in the Philippines, Fluid Solutions offers a diverse range of greases, providing industries with the right formulations for their specific needs.
Types of Grease Thickeners
Grease thickener types can broadly be categorized into two main types: soap and non-soap thickeners.
Simple Soaps
Commonly used for general-purpose greases, providing adequate performance for most industrial applications. A simple soap is created from the reaction of a single acid, typically 12-hydroxy stearic acid, with a metallic hydroxide such as lithium, aluminum, calcium, or sodium.
Calcium SoapsÂ
Calcium soap greases offer improved water resistance and shear stability compared to lithium greases. However, they lack good thermal resistance (dropping point: 135-145°C) and are used in applications operating up to 110°C.
Lithium SoapsÂ
Lithium 12-hydroxy stearate greases are the most used soap greases because of their efficiency as thickeners. They provide good lubricity, shear stability, thermal resistance (dropping point: 190-220°C), and low oil separation. Their oxidative resistance is enhanced with antioxidants. These greases, such as bearings, are typically used in automotive and industrial applications.
Sodium SoapsÂ
Sodium soap greases have high dropping points (175°C) but are limited to operating conditions below 120°C because of poor oxidative stability and high oil bleed. They also have poor water resistance but provide good shear stability and lubricity.
Aluminum SoapsÂ
Aluminum soap greases exhibit excellent oxidation and water resistance but have low thermal resistance (dropping point: 110-115°C), limiting their use to temperatures below 80°C. When overheated, they form stringy gels that increase torque, requiring more work to turn a bearing.
Mixed Soaps
Mixed soap greases combine different soap greases to address the limitations of individual types. A typical example is lithium/calcium grease, where lithium enhances high temperature resistance and calcium improves water washout resistance and cost-effectiveness. Sodium/calcium combinations are also used to enhance water resistance without significantly reducing grease operating temperatures, while calcium helps refine sodium soap fibers for smoother texture.
Complex Soaps
Complex soap thickeners, made by reacting short-chain organic acids with metal hydroxides or carbonates like lithium hydroxide or calcium carbonate, offer superior high-temperature properties and shear stability compared to simple soap thickeners. They are commonly used in lithium complex grease and are known for their excellent shear stability and high-temperature performance.
Non-soap Thickeners
Also known as inorganic thickeners. These thickeners use substances like silica, clay, or calcium sulfonate to thicken base oils. Among them, calcium sulfonate greases are highly favored for their shear stability, high-temperature resilience, and corrosive conditions resistance.
Bentonite (Clay​)​
Bentonite grease, formulated with bentonite clay, is known as a non-melt lubricant because of its indefinite dropping point. It resists temperature changes, superior ​w​ear protection, exceptional water tolerance, good mechanical stability, and strong adhesion.
Polyurea
Polyurea grease is highly popular for its water resistance, oxidation stability, rust prevention, durability, versatility, mechanical strength, and high-temperature performance. It is recommended for long-life applications in various industries and is crucial for lubricating steel plants and electric motors.
Silica and PTFE (Polytetrafluoroethylene)
PTFE greases are high-temperature greases known for their thermal stability, water resistance, shear stability, and lubricity, typically with dropping points above 260°C. These inorganic thickeners provide specialized properties, such as extreme temperature resistance and enhanced lubricity, which are ideal for challenging industrial applications.
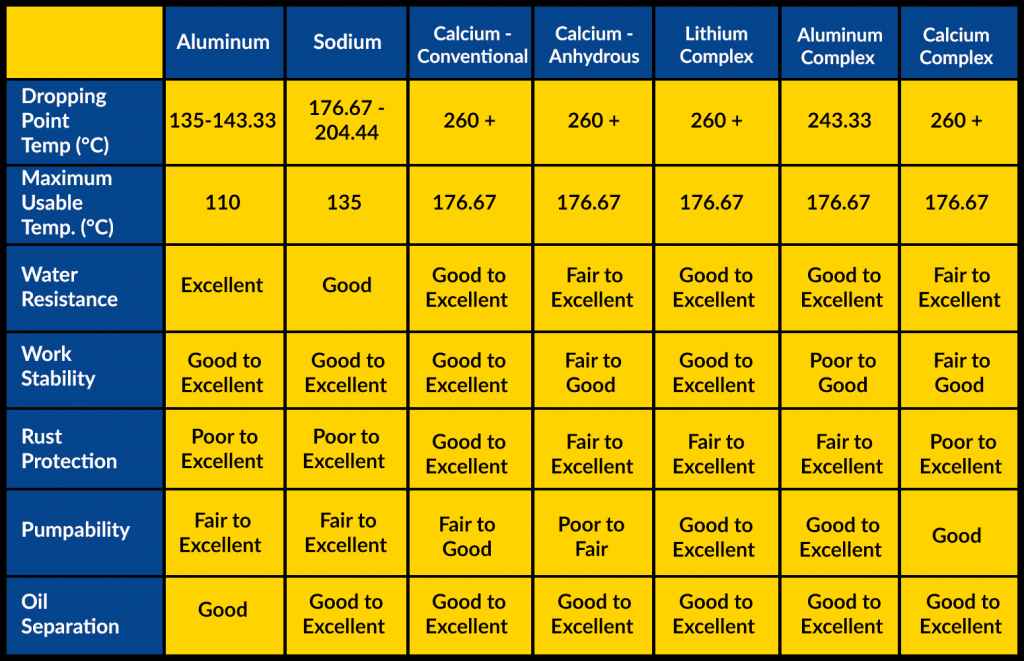
Fluid Solutions: Your go-to Grease Supplier in the Philippines
Fluid Solutions is a leading manufacturer of metalworking fluids and industrial lubrication solutions in the Philippines. We offer a wide range of products, including metalworking fluids, lubricating oil, food-grade oils, greases, and maintenance equipment, ensuring reliable solutions to optimize machinery performance.
Our lubrication consultants promptly address concerns and inquiries, guaranteeing expert guidance and support with a response within 24 hours.
Call us at (02) 8370 5928 / (0917) 8​9​4 9156 or email us inquiry@fluidsolutions.com.ph for tailored guidance in selecting suitable lubricants for your business needs. You can also reach us via our official website or social media pages to learn more about our products.