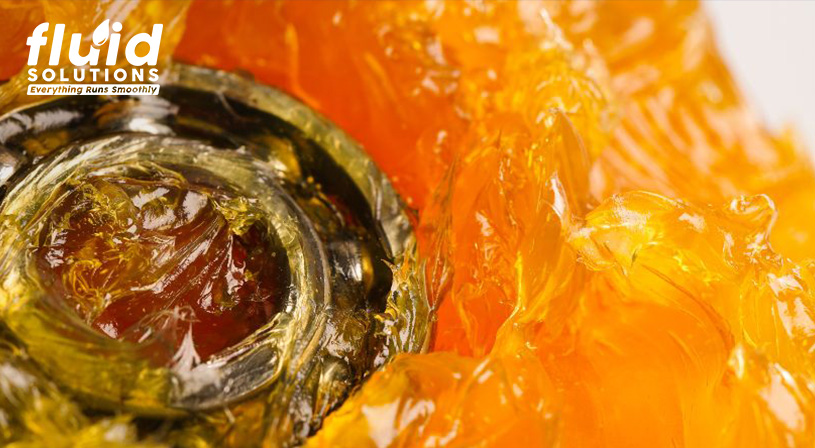
Understanding the principles of grease lubrication is crucial for maintaining industrial machinery and preventing premature bearing failures. Both over-lubrication and under-lubrication can significantly impact machinery performance and longevity. This blog explores these principles, the consequences of improper lubrication, and provides guidelines for determining the correct grease quantity for bearings.
What is Over-Lubrication?
Over-lubrication refers to the situation where an excessive amount of grease or lubricant is applied to machinery components, particularly bearings. This can occur due to factors such as too frequent greasing intervals, dispensing too much grease per application, or lacking mechanisms to allow old or excess grease to exit, such as relief ports
The consequences of over-lubrication include:
- Elevated Operating Temperatures: The surplus grease increases friction within the bearing, leading to higher temperatures. This heat can degrade the lubricant prematurely.
- Pressure Build-Up: Excessive grease can build up pressure inside the bearing housing, potentially causing seals to burst. This can allow contaminants to enter, accelerating wear and leading to premature bearing failure.
- Waste of Resources: Applying more grease than necessary not only increases operating costs but can also lead to environmental concerns if excess grease leaks or is disposed of improperly.
What is Under-Lubrication?
Under-lubrication occurs when machinery components, particularly bearings, do not receive an adequate amount of grease or lubricant necessary for proper operation. This can happen due to infrequent greasing intervals, insufficient grease quantities applied, or using lubricants that are not suitable for the operating conditions.
The consequences of under-lubrication include:
- Increased Friction and Heat: Insufficient lubrication leads to higher friction between moving parts, generating excessive heat. This heat accelerates the breakdown of the lubricant and can cause premature wear of the bearing surfaces.
- Component Wear: Without adequate lubrication, bearings are prone to increased wear and potential damage. This can lead to reduced operational efficiency and ultimately, machinery breakdown.
- Contamination Risk: Voids or gaps in the lubrication layer can allow contaminants such as dust, dirt, or moisture to enter the bearing. These contaminants can exacerbate wear and compromise the integrity of the bearing over time.
The Right Quantity
To begin with, it’s crucial to accurately assess the free bearing space in cubic centimeters (cc) for each specific bearing. If detailed reference materials are not available, the following steps can help estimate this space effectively:
- Identify Bearing Inner Diameter or Bore: Start by measuring or identifying the inner diameter (ID) or bore size of the bearing that requires lubrication.
- Determine Bearing Type or Code: Use the bearing type or code as a reference to select the appropriate “curves” from 1 to 9. These curves correspond to a table that provides estimates for the free bearing space.
- Calculate Grease Volume: Once the bearing characteristics are identified, refer to the table with “curves” and use the x-axis values to calculate the estimated grease volume in cubic centimeters (cc).
Ascertain Fill Quantity
After determining the free bearing space, the next step is to ascertain the fill quantity of grease as a percentage of this total space. This involves calculating the speed factor of the bearing, which is calculated as (OD + ID) / 2) x rpm).
- Higher Speed Factors: Bearings operating at higher speeds typically require less grease volume to maintain effective lubrication.
- Lower Speed Factors: Bearings operating at lower speeds may necessitate a fuller charge of grease to adequately lubricate the bearing surfaces.
Using these guidelines ensures that the right amount of grease is applied to each bearing, extending the lifespan of machinery components. It helps mitigate risks associated with both over and under-lubrication.
By following these practices, reliable and cost-effective lubrication management can be achieved.
Choose Fluid Solutions
Understanding the principles of grease lubrication and avoiding both over and under-lubrication are critical for maximizing the performance and lifespan of industrial bearings. Lubrication consultants, such as Fluid Solutions, offer specialized expertise in grease lubrication for specific operating conditions. Moreover, as a trusted grease supplier in the Philippines, Fluid Solutions offers a comprehensive range of greases for various industries.
Contact Fluid Solutions today at (02) 8370 5928 / (0917) 894 9156 or via email at inquiry@fluidsolutions.com.ph for expert advice and tailored lubrication solutions to meet your specific business needs. Ensure your machinery operates at peak efficiency with Fluid Solutions’ quality lubricants.