Regular quality checks help in identifying the best lubricants that offer superior protection against wear and tear. Among the various tests available, the 4 Ball Scar Test stands out as a pivotal method for determining the wear reduction properties of grease lubricants and​ oil​ lubricants. This blog delves into the significance of the 4 Ball Scar Test, its methodology, and how to interpret its results to make informed decisions about lubricant and grease quality.
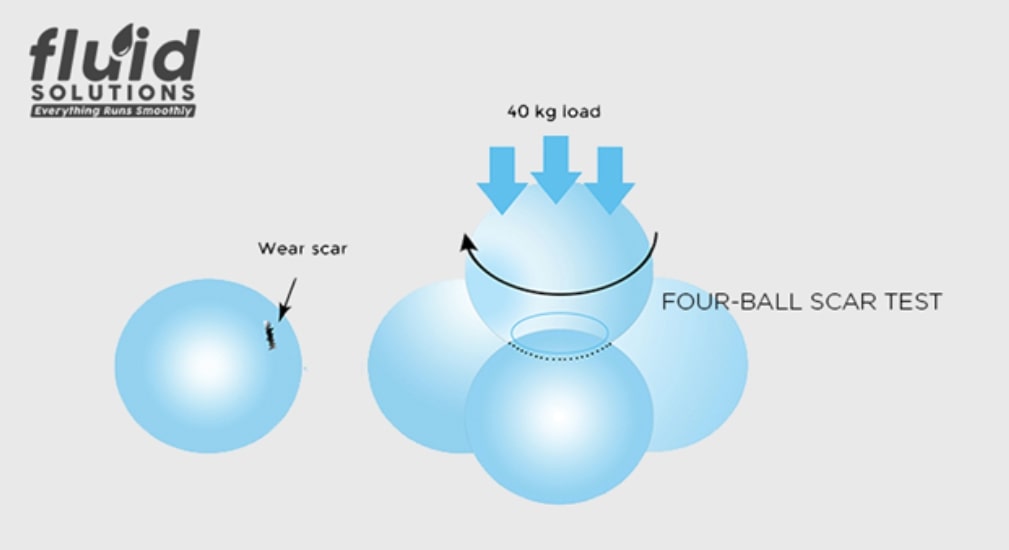
[Image Alt Text: Four Ball Scar Test]
What is the 4 Ball Scar Test?
A variation of the 4 Ball Weld Load Test, the 4 Ball Scar Test, aims to determine the wear reduction properties of lubricants and greases. Unlike its counterpart, which focuses on the load-carrying capacity of a lubricant, the 4 Ball Scar Test aims to evaluate the wear-reduction properties of lubricants and greases. This test is instrumental in determining how well a lubricant can minimize wear and tear on metal surfaces under consistent load conditions.
Purpose of the 4 Ball Scar Test
The primary purpose of the 4 Ball Scar Test is to provide a quantitative measure of a lubricant’s ability to​ withstand a fixed load under a given time and speed​. By simulating the operational conditions that lubricants will face in real-world applications, this test helps in comparing the effectiveness of different lubricants in protecting metal surfaces from damage.
How the 4 Ball Scar Test is Conducted
The 4 Ball Scar Test follows a standardized procedure to ensure consistency and reliability of results. The configuration of the 4 steel balls and lubricant (or grease) is the same as with the Weld Load test, but the load applied on the top ball is fixed at only 40 kgs., for 1 hour. Welding is not a typical occurrence in this test, yet a ‘scar’ is typically manifested on the steel balls after the test. Here’s a step-by-step explanation of how the test is conducted:
Configuration of the Steel Balls and Lubricant
- Setup: Three steel balls are secured in a cup, forming the stationary bottom layer.
- Lubricant Application: The lubricant or machine grease being tested is applied between these three stationary balls.
- Rotating Ball: A fourth steel ball is placed on top and rotated against the three stationary balls.
Fixed Load and Test Duration
The load applied on the rotating ball is fixed at 40 kgs. Unlike the Weld Load Test, where the load is incrementally increased until welding occurs, the 4 Ball Scar Test maintains this load for a continuous duration of one hour. This fixed load condition allows for the consistent assessment of wear reduction properties without the extreme conditions that cause welding.
Significance of Scar Diameter Measurement
The primary outcome of the 4 Ball Scar Test is the measurement of the scar diameter on the steel balls. This measurement is critical for determining the efficacy of the lubricant.
Measuring Scar Diameter
The scar diameter is measured in mm., and the values resulting from the tests of different lubricants may be compared to guide wear-reduction properties.
Comparing Scar Diameters
By comparing the scar diameters resulting from grease tests on different lubricants, one can gauge the relative effectiveness of each product. This comparison helps in selecting lubricants that offer superior wear protection, thereby extending the life of machinery components and reducing maintenance costs.
Benefits of Using High-Quality Lubricants
Investing in high-performance grease lubricant has numerous benefits. Here’s why ensuring the use of top-notch lubricants is crucial:
Enhanced Equipment Longevity
High-quality lubricants significantly reduce wear and tear, thereby prolonging the life of machinery components. This results in fewer replacements and repairs, leading to cost savings.
Improved Efficiency
Lubricants that excel in the 4 Ball Scar Test typically provide smoother operation of machinery, enhancing overall efficiency. Reduced friction means less energy is required to operate the equipment, translating to lower energy costs.
Reduced Downtime
Machinery breakdowns can be costly and disruptive. Using lubricants with proven wear-reduction properties minimizes the risk of unexpected failures, ensuring that operations run smoothly and without interruption.
Cost Savings
While high-quality lubricants might have a higher upfront cost, their long-term benefits far outweigh the initial investment. Reduced maintenance, fewer repairs, and extended equipment life contribute to significant cost savings over time.
The 4 Ball Scar Test is an essential tool in the arsenal of industrial maintenance professionals. It provides a reliable measure of a lubricant’s wear-reduction properties, helping in the selection of products that offer the best protection for machinery components.
Learn More About Industrial Lubricants with Fluid Solutions
By understanding and utilizing the insights provided by the 4 Ball Scar Test, you can ensure that your machinery operates at peak efficiency, with optimal protection against wear and tear. Partner with Fluid Solutions to achieve superior performance and reliability in your industrial operations.
At Fluid Solutions, we are committed to providing high-quality industrial lubricants that meet the stringent demands of various applications. Our extensive range of products includes  Food Grade Oils and Greases, High Performance Greases, Specialty Lubrication, Maintenace Equipment, and Metalworking Fluids. Explore our blog for more insights into industrial lubricants and their applications. For expert advice and superior lubrication solutions, contact us at (02) 8370 5928 or via email at inquiry@fluidsolutions.com.ph.