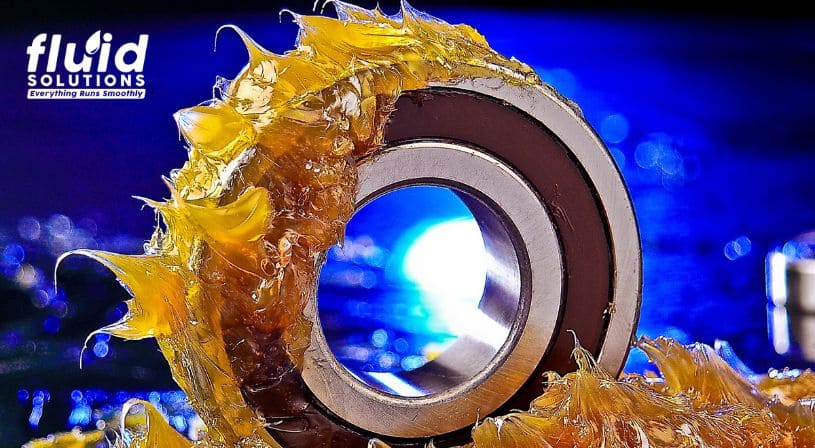
Greases play a crucial role in maintaining the performance and longevity of your bearings. However, not all lubrication issues are immediately visible, and one such hidden problem is grease bleeding.
Knowing about grease bleeding is key to keeping equipment running smoothly and reliably. Understanding the risks it poses protects your machines and benefits your business overall.
The Basics of Grease Bleeding
Grease bleeding, also known as grease separation, occurs when the base oil component separates from the thickener of the grease. This can result from factors such as extreme heat, vibrations, or improper storage. When this separation occurs, the grease can’t lubricate rotating components as effectively, which can lead to damage or even failure.
While some grease separation is natural over time, certain conditions—like high temperatures or excessive load—can accelerate the process. This makes it difficult for the grease to form a protective layer between moving components, increasing the risk of friction, wear, and eventual equipment breakdown.
Choosing the right grease, storing it correctly, and applying it properly can help prevent these issues. Regular checks on grease performance allow you to catch problems early and fix them before serious damage happens.
Why Grease Bleeding Occurs
Extreme temperatures can significantly affect grease structure. High temperatures can thin the grease, causing oil to separate and reducing its lubrication effectiveness. On the other hand, low temperatures can make the grease too thick, restricting its ability to flow and protect moving parts. Both scenarios can result in inadequate lubrication, heightening the risk of equipment damage.
Mechanical stress in high-pressure situations can also break down grease. When machines operate under heavy pressure, grease can be forced out of its protective barrier, leading to leaks and inadequate lubrication. This results in increased friction and wear on critical components.
Additionally, time and shelf life play a role in grease performance. Over time, grease tends to separate naturally, with oil rising to the surface and the thickener settling. This separation reduces the grease’s effectiveness, making it essential to regularly check its quality. Using grease within its shelf life and replacing it as needed helps ensure optimal performance and protection for machinery.
How to Prevent Grease Bleeding
By focusing on these three steps—selecting the right grease, applying it properly, and conducting regular maintenance—your businesses can effectively prevent grease bleeding and keep your machinery running smoothly.
1. Choosing the Right Grease: To prevent grease bleeding, start by choosing the right grease for your specific application and environment. Consider factors like temperature, load, and exposure to contaminants to ensure it performs well.
2. Routine Maintenance: Routine maintenance is equally important. Regularly check grease levels and assess performance to catch any signs of bleeding early. Adjust grease levels as needed and replace any old or degraded grease to maintain efficiency.
Understanding and controlling grease bleeding is critical for keeping machinery running efficiently and reliably.
Businesses may greatly improve performance and extend equipment life by selecting and using the proper grease lubricant. Choosing the right grease based on temperature, load, and environmental conditions gives maximum protection for moving parts.
Additionally, regularly monitoring and maintaining equipment allows for early detection of any grease bleeding issues, minimizing potential damage. By focusing on the right grease selection and proper grease lubricant application, businesses can protect their machinery and achieve more efficient operations, ultimately leading to lower maintenance costs over time.
Minimize Grease Bleeding with Fluid Solutions’ High-Performance Greases
Reduce grease bleeding with Fluid Solutions’ high-performance grease products, designed to enhance lubrication and protect your machinery. Our top-quality grease lubricants effectively eliminate grease separation effects, ensuring your equipment operates at its best and lasts longer.
With years of expertise in machinery lubrication systems, Fluid Solutions Inc. offers not only premium products, but also essential support services tailored to your specific needs. Our knowledgeable team is here to help you select the right grease for your requirements, ensuring optimal results.
Reach out to Fluid Solutions today to schedule a consultation or ask about our products. We’re here to help you keep your machinery running efficiently and reliably!
Contact us at (02) 8370 5928 / (0917) 894 9156 or via email at inquiry@fluidsolutions.com.ph.
Follow us on Facebook and LinkedIn for updates!    ​​Â