
Image Source: https://lacisoft.com/2016/12/28/industrial/
Fire hazards are a constant threat in the steel industry, where operations often involve extremely high temperatures, flammable materials such as mineral oil-based hydraulic fluids. These fluids, while commonly used, present significant fire risks. Fortunately, safer alternatives, such as fire-resistant hydraulic oils, can be utilized without compromising productivity or performance of steel production lines.
Key Takeaways
- Mineral oil-based fluids pose serious fire risks in high-temperature steel production environments.
- Fire-resistant hydraulic fluids greatly reduce fire severity and response time during incidents.
- Polyol ester-based fluids (HFD-U) offer the best balance of fire safety, performance, and environmental impact.
- Case studies show major improvements in safety and downtime reduction after switching to fire-resistant fluids.
- Use of FM Global-approved fluids can lower insurance costs and improve plant safety.
- Proper system compatibility checks are essential when transitioning to fire-resistant oils.
Fire Hazards in Steel Production
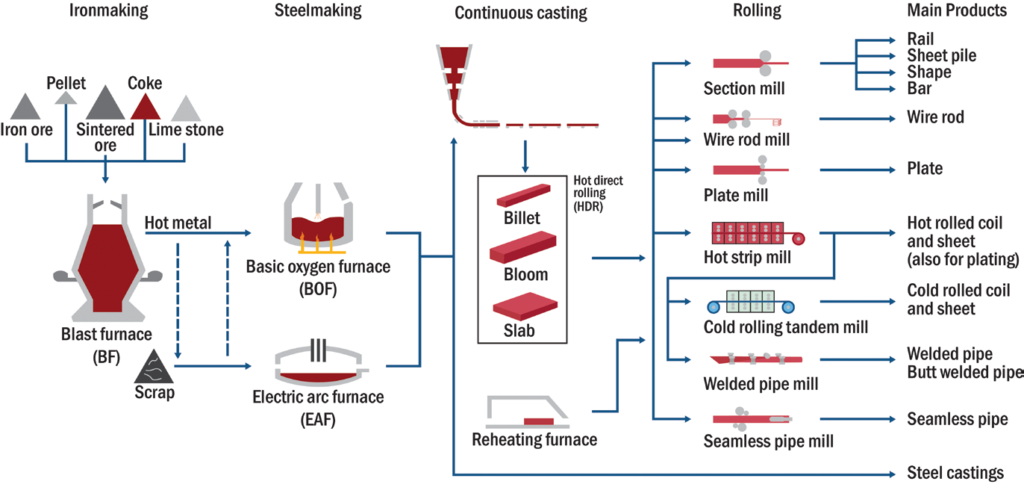
Using mineral oil-based hydraulic fluids in steel plants, where temperatures can exceed 2,732°F (1,500°C), poses a high fire risk. These fluids, when exposed to red-hot steel or sparks during stainless steel welding operations, can ignite rapidly, leading to dangerous fires.
Consequences of Fire in Steel Plants
A fire in a steel production facility can be catastrophic, threatening personnel safety and causing extensive damage to equipment and infrastructure. These incidents also result in long periods of production downtime, which can lead to severe financial losses. Beyond the initial damage, the additional costs include increased insurance premiums and potential capital losses. Switching to fire resistant fluids can mitigate these risks and reduce overall costs in the long run.
Case Studies: Transitioning to Fire-Resistant Hydraulic Fluids
Case Study 1: Billet Caster Operations
A customer ​operating their billet caster ​using a mineral oil-based ​hydraulic ​fluid experienced repeated​ hose​ ruptures, causing the oil to ignite on hot billets​ and form a massive fire with vapor clouds forming into fireballs​. ​After​ switching to fireproof hydraulic oil, while those ruptures persisted, the customer saw a dramatic reduction in fire severity and faster control over hazardous situations.
Case Study 2: Managing Leaks and Fire Risks
In another operation, leaks ​caused​ hydraulic fluid to ​form a ​pool on the floor, igniting when ​contacting​ liquid metal ​sparks​​, catching fire​. After ​a test using ​fire-resistant fluids, the customer found that flame resistant hydraulic oil extinguished in under 60 seconds, while the mineral oil burned for over an hour. They quickly switched to fire resistant fluids to enhance safety.
Case Study 3: Pickling Line Safety
On a pickling line, ruptures in ​hydraulic hoses containing mineral oil​ led to multiple fires. After transitioning to fireproof hydraulic oil, the plant saw a significant decrease in fire risks and downtime, protecting both equipment and personnel.
Case Study 4: Mobile Equipment Safety
A mobile unit transporting hot slag caught fire because of its mineral oil-based fluid. The equipment was destroyed, but all mobile units were subsequently converted to water-free, fire-resistant hydraulic fluids, eliminating further incidents.
Types of Fire-Resistant Hydraulic Fluids
There are several fire-resistant fluids that steel plants can switch to, each with varying pros and cons. These include:
1. ​​Phosphate Ester (HFD-R): While fire-resistant, these fluids contain CMR (carcinogenic, mutagenic, and reprotoxic) compounds, posing health and environmental risks. Combustion fumes are neurotoxic, and despite providing good pump lubrication, they can shorten servo valve lifespan. HFD-R fluids also form aggressive acids over time and are 10 to 15 times more expensive than mineral oils. Primarily used in power generation, they occasionally appear in steel plants.
2. Water Glycol (HFC): Widely used in steel plants, HFCs account for about 50% of the fire-resistant hydraulic fluid market due to their high-water content, which provides excellent fire resistance. They are comparable in price to mineral oils but fall short in performance. HFC fluids require more frequent maintenance, reduce component service life, and increase energy consumption by 10 to 20% compared to mineral oils or polyol ester-based fluids, driving up the total cost of operation (TCO).
3. Polyol Ester-Based Fluids (HFD-U): These fluids offer the best balance of fire resistance, performance, and environmental friendliness, though they are more expensive
Benefits of Using Polyol Ester-Based Fluids (HFD-U)
Polyol ester-based fluids offer significant safety benefits, producing about 10-15% less heat during combustion compared to mineral oil. The heat of combustion for mineral oil-based hydraulic fluids is typically around 43-44 kJ/g, whereas HFD-U, polyol ester fire-resistant fluids have a heat of combustion of about 38 kJ/g. Additionally, these fluids don’t vaporize as easily, preventing the formation of fireballs.
Fire Resistance Testing for Hydraulic Fluids
Hydraulic fluids can undergo various tests to determine their fire resistance. The most widely recognized and accepted tests are conducted by Factory Mutual (FM Global), the testing and approval division of a leading industrial insurance provider (www.fmglobal.com). Using an FM Global-approved hydraulic fluid can often help manufacturers lower their insurance premiums. In addition to FM Global, many other organizations and companies have developed fire resistance tests, typically designed to simulate specific real-world accidents.
Best Practices for Switching to Fire-Resistant Hydraulic Fluids
Switching from mineral oil to fire-resistant fluids like QUINTOLUBRIC® 888, Quaker’s premier ester-based synthetic, water-free hydraulic fluid (HFD-U), is a relatively simple process but requires careful attention. QUINTOLUBRIC® 888 is used in over 60 presses worldwide and is backed by leading hydraulic component OEMs and hydraulic press manufacturers. However, ensuring compatibility with key system components, such as tank coatings, seals, and pumps, is essential. Moreover, with varying grades and qualities of polyol ester (HFD-U) fluids available, choosing the right option is crucial. Maintaining fire resistance requires a residual mineral oil content of less than 5%.
Conclusion
Steel production is an industry where dangerous situations can arise daily. Switching to water-free, polyol ester-based fire-resistant hydraulic fluids can significantly improve plant safety without compromising the productivity or performance of the production line.
Switch to Safer Hydraulic Solutions Today
Reduce fire risks in your steel production facilities by switching to fireproof hydraulic oil– and fire-resistant fluids like QUINTOLUBRIC® 888. Explore safer alternatives to enhance workplace safety without compromising performance. Contact Fluid Solutions at (02) 8370 5928 / (0917) 894 9156, or via email at inquiry@fluidsolutions.com.ph for customized hydraulic solutions and expert advice on switching to fire-resistant fluids.