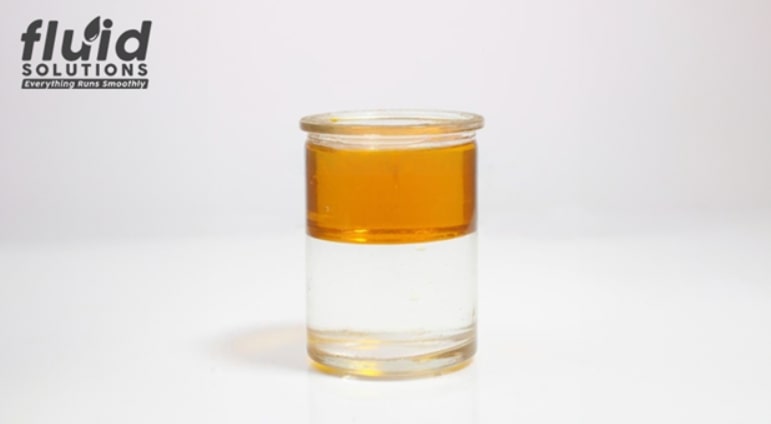
The ingress of water or moisture in lubricants is somehow unavoidable. From the drums, exposure to extreme hot-cold cycles can introduce water. Sometimes, water contamination may come from cooling system leaks; in metalworking fluids, prior processes using emulsions or alkaline cleaners can contribute to moisture content; with air compressors, the moisture content in the intake air can introduce water, too.
This blog delves into the causes and effects of water contamination in lubricants, explaining how it occurs, its impact on lubricant performance, and the crucial steps needed to prevent it.
Common Sources of Water Contamination
Water contamination can originate from several sources, each contributing to the degradation of lubricants and the efficiency of machinery. Understanding these sources is the first step in mitigating the problem.
Drum Exposure
One of the primary sources of water contamination is the exposure of lubricant drums to extreme temperature cycles. During hot-cold cycles, condensation can form inside the drums, introducing water into the lubricant.
Cooling System Leaks
Leaks in the cooling system are another significant source of water contamination in grease. When the cooling system malfunctions or wears down, water can seep into the lubricant, leading to compromised performance.
Metalworking Fluids
In metalworking operations, prior processes using emulsions or alkaline cleaners can contribute to moisture content in lubricants. This moisture can degrade the quality and effectiveness of the metalworking fluids.
Air Compressors
The intake air in air compressors often contains moisture, which can condense and mix with the lubricant. This is particularly problematic in environments with high humidity levels, leading to increased water contamination in oil.
Levels of Water Contamination
Water contamination in lubricants can be categorized based on the concentration of water present. Each level has distinct characteristics and impacts on the lubricant’s performance.
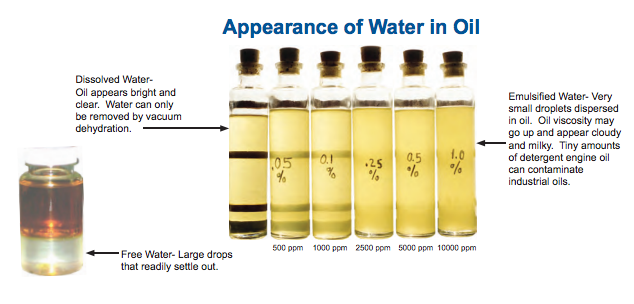
[Image Alt Text: Water Contamination Levels in Oil]
Low-Level Moisture Content
At levels of 0.02 to 0.06% (200 to 600 ppm), water contamination is at such a low level that it is dissolved in the oil and unnoticeable. Despite being dissolved, this moisture can still contribute to long-term issues if not addressed.
Emulsion Stage
When the water content exceeds the low-level threshold, the oil and water mix to form an emulsion, giving the lubricant a hazy appearance. This stage indicates that the lubricant is starting to struggle with the water content and is a precursor to more severe issues.
Saturation Point
Past the emulsion stage is the saturation point, where the lubricant can no longer hold the water as dissolved or as an emulsion. At this stage, a clear phase separation occurs between the oil and water, which is easily observed. The water, being denser, settles at the bottom of the container or system.
Effects of Water Contamination
Water contamination in lubricants can have several detrimental effects on both the lubricant and the machinery it is meant to protect. Understanding these impacts underscores the importance of preventing water contamination.
The utmost attention should be given to prevent or minimize water contamination, since it can contribute negatively to lubrication performance. Here are some of the common effects:
- Rust and Corrosion may be accelerated
- Wear on metal components will be evident
- Lubricant oxidation is hastened
- Acid and sludge formation
Accelerated Rust and Corrosion
Water promotes rust and corrosion of metal components. Even lesser amounts of water can cause considerable damage over time, leading to pitting and degradation of metal surfaces. This not only affects the performance but also reduces the lifespan of the machinery.
Increased Wear on Metal Components
Water contamination leads to inadequate lubrication, increasing friction between metal parts. This results in excessive wear and tear, which can cause premature failure of components. The presence of water can also lead to abrasive wear as water mixes with particulate matter to form a grinding paste.
Hastened Lubricant Oxidation
Water accelerates the oxidation process of lubricants. Oxidation leads to the formation of acids and sludge, which further degrade the lubricant’s properties. Oxidized lubricants lose their effectiveness, reducing their ability to protect and lubricate machinery components properly.
Formation of Acid and Sludge
As lubricants oxidize, they form acids and sludge. Acids can cause further corrosion of metal parts, while sludge can block oil passages and filters, leading to inadequate lubrication and potential machinery failure. This buildup can also increase the operating temperature, further degrading the lubricant and the machinery.
Protect Your Equipment Metalworking Fluids Manufacturers: Fluid Solutions
Water contamination in lubricants is a prevalent issue that can significantly impact the performance of the lubricant and the longevity of machinery. By understanding the sources and effects of water contamination, and implementing effective prevention strategies, you can ensure that your lubricants continue to protect and enhance the performance of your equipment.
At Fluid Solutions, we specialize in providing comprehensive lubrication solutions designed to prevent water contamination. Our extensive range of products includes Food Grade Oils and Greases, High Performance Greases, Specialty Lubrication, Maintenace Equipment, and Metalworking Fluids. Explore our blog for more insights into industrial lubricants and their applications. For expert advice and superior lubrication solutions, contact us at (02) 8370 5928 or via email at inquiry@fluidsolutions.com.ph.