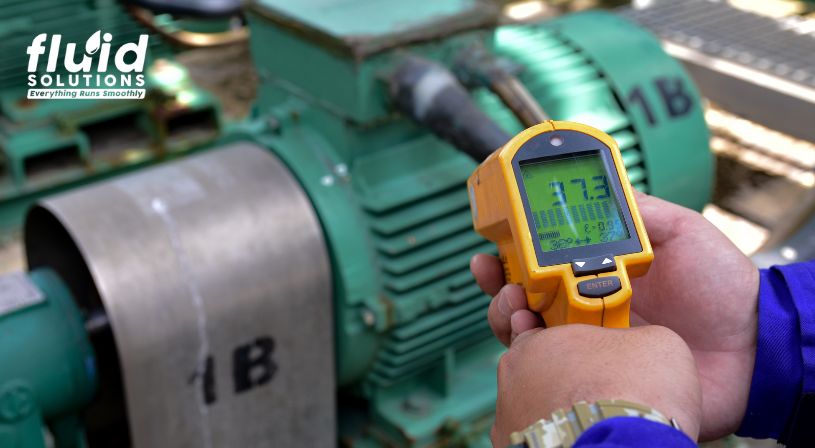
Temperature plays a crucial role in the performance and reliability of industrial lubricants. It directly affects viscosity, influencing how well lubricants reduce friction and wear in machinery. High temperatures accelerate oxidation, reducing the lubricants’ usage lifespan.
This blog explores how temperature variations impact lubricant performance, the risks of oxidation at elevated temperatures, and practical strategies—such as proper lubricant selection, temperature monitoring, and cooling solutions—to mitigate these challenges. Implementing these measures helps ensure consistent lubrication, minimize downtime, and maintain peak operational efficiency.
Key Takeaways:
- Temperature fluctuations impact lubricant viscosity, affecting machinery protection and efficiency.
- High temperatures accelerate oxidation
- Oxidation reduces lubricant usage lifespan
How Temperature Affects Lubricant Viscosity
Lubricant viscosity refers to the resistance of a lubricant to flow. It determines how well the lubricant can form a stable, protective film between moving machine components. Viscosity is highly sensitive to temperature changes; as temperatures fluctuate, so does the lubricant’s ability to maintain its protective layer.
Viscosity and Temperature Relationship Explained
Lubricant viscosity is inversely related to temperature. This means as the oil temperature increases, lubricant viscosity decreases, causing the lubricant to become thinner. Conversely, lower temperatures cause lubricants to thicken, increasing their viscosity.
When lubricant viscosity decreases due to rising temperatures, its film thickness diminishes. The lubricant can no longer adequately separate the machine component surfaces, leading to increased contact, accelerated wear, and overheating.
Conversely, when temperatures drop and viscosity increases excessively, lubricants become thicker. This heightened viscosity can lead to poor lubricant circulation, causing insufficient lubrication and increased friction, ultimately impairing machinery efficiency. Such conditions often cause additional energy to overcome increased resistance, substantially raising operational costs.
Temperature-induced viscosity fluctuations can complicate machinery startup, especially in colder environments. Thick lubricants can hinder machinery start-up processes by causing increased initial resistance, putting additional strain on motors and components, and potentially leading to premature failure.
How Temperature Affects Lubricant Usage Lifespan
Exposure to consistently high temperatures significantly impacts lubricant longevity and performance. Lubricants exposed to elevated temperatures are vulnerable to rapid degradation.
Accelerated Oxidation because of High Temperatures
Oxidation, a chemical reaction involving oxygen, is one of the primary ways lubricants degrade. While oxidation occurs naturally over time, elevated temperatures substantially speed up this process. As lubricants oxidize, their chemical composition breaks down, resulting in viscosity changes, acid formation, sludge build-up, and overall loss of lubrication properties.
Specifically, when lubricant temperatures exceed recommended operating limits, oxidation rates can double for every 10°C increase above typical operating temperatures. This rapid oxidation reduces lubricant lifespan, causing more frequent lubricant replacements and increased maintenance costs.
Other Effects of Oxidation on Lubricants
Oxidized lubricants lose their effectiveness in protecting machinery parts. Here are the other effects of oxidation:
- Viscosity Change: Oxidation causes lubricants to either thicken excessively, hindering flow, or thinning out, reducing their protective capabilities.
- Sludge Formation: Oxidation generates insoluble particles and sludge deposits. These deposits clog filters, disrupt lubricant flow, and cause abrasive wear.
- Corrosion: Oxidation by-products, such as acids, cause corrosion of machinery parts, significantly shortening equipment lifespan.
Oxidation can also negatively impact seal integrity. Lubricant degradation by-products can degrade rubber seals and gaskets, leading to leaks, contamination, and further speed up lubricant breakdown.
Fluid Solutions: Your Partner for Optimized Lubricant Performance
Understanding the critical relationship between temperature and lubricants is essential for machinery longevity and operational efficiency. At Fluid Solutions, we specialize in providing top-quality industrial lubricants and high-temperature grease designed to withstand extreme operating conditions. Our lubricants maintain optimal viscosity-temperature profiles, ensuring reliable protection against friction, wear, and corrosion.
Trust Fluid Solutions to deliver lubricants that perform consistently under varying temperature conditions, reducing downtime, maintenance costs, and enhancing overall productivity.
Contact Fluid Solutions today at (02) 8370 5928 / (0917) 894 9156 or via email at inquiry@fluidsolutions.com.ph to explore our complete range of lubricant solutions, tailored to your operational temperature requirements. Ensure peak performance and reliability—no matter the temperature.
Social Media Links:
Facebook: https://www.facebook.com/fluidsolutionsinc
LinkedIn: https://www.linkedin.com/company/fluid-solutions-inc