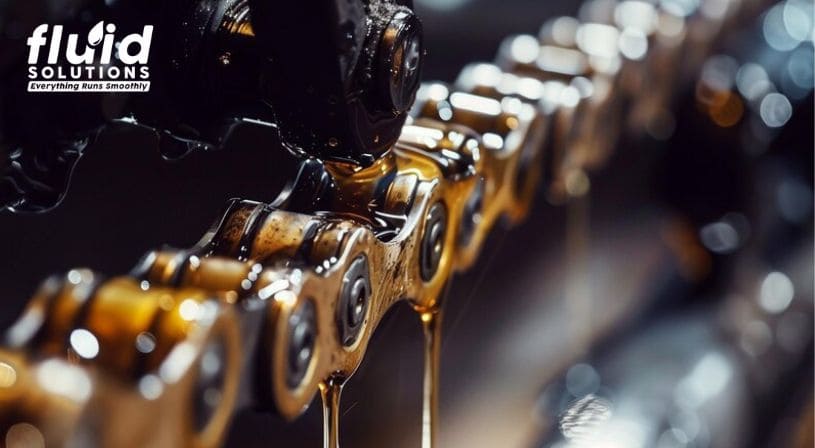
Source: https://www.freepik.com/premium-ai-image/pouring-oil-tank-car-selective-focus_225154468.htm#fromView=search&page=2&position=30&uuid=8638b054-94f6-4895-865f-45844ab06978
Chain lubrication is a critical aspect of maintenance that often gets overlooked by maintenance practitioners, leading to significant operational issues. The proper lubrication of chains is essential in ensuring smooth operation, preventing wear and tear, and extending the life of the chains. However, many common mistakes are made in chain lubrication practices, such as the use of inappropriate lubricants like used oils and greases. These errors can lead to a range of problems, including chain elongation, breakages, and unsmooth, jerky movements. Â
The Importance of Using the Correct Lubricant
Understanding the conditions under which chains operate is the first step in selecting the right lubricant. Chains function under boundary lubrication conditions, where there is minimal separation between metal surfaces.
Greases, for example, lack the creeping or penetrative capabilities needed to seep into the critical areas of the chain, such as the pin-roller-bushing interface. This inability to reach these areas leads to inadequate lubrication, which can cause chain elongation and eventually result in chain breakages. Similarly, used lubricants, which are often contaminated with sludge or carbon, can clog the entry points of oils into the chain’s moving parts. These contaminants reduce the lubricant’s effectiveness and increase the risk of mechanical failure. Â
Inappropriate lubricants also cannot provide the high viscosity and extreme pressure (EP) additives required for chains operating under boundary friction regimes. Hydraulic oils, which are sometimes mistakenly used, do not possess the viscosity levels—such as ISO VG 320—needed to protect the chain from the high pressures and temperatures encountered during operation. The absence of these critical properties in the lubricant can lead to increased wear, reduced efficiency, and ultimately, equipment failure. Â
The Role of Tackifiers in Chain Lubrication
Tackifiers are a crucial component of an effective chain lubricant, especially in the context of industrial chain lubrication. These additives enhance the lubricant’s ability to adhere to the metal surfaces of the chain, reducing the likelihood of drip-offs and ensuring that the lubricant remains in place even under heavy loads and at high temperatures.
In manufacturing environments where chains are often used to convey goods, the use of lubricants with tackifiers can prevent unwanted migration or contamination of the products being handled. This is especially critical in industries where cleanliness and product integrity are paramount, such as in the food and beverage sector or in precision manufacturing.
By ensuring that the lubricant remains in place, tackifiers help to protect the chain from environmental factors that could lead to degradation, such as moisture and contaminants.
Ensure Smooth Chain Operation with Fluid Solutions’ Chain Lubricants
In maintaining the performance and longevity of your chains, choosing the right lubricant is essential. Fluid Solutions is a trusted supplier of chain oils designed to meet the specific needs of industrial chains, ensuring optimal performance and protection. Our range of lubrication products includes high-quality chain oils with penetrative capabilities, high viscosity, EP additives, and tackifiers to keep your chains running smoothly and efficiently. Our Lubrication Consultants are available to help you select the right products for your specific needs, ensuring that your equipment operates at peak efficiency and reliability. Â
Contact Fluid Solutions today at (02) 8370 5928 / (0917) 894 9156 or via email at inquiry@fluidsolutions.com.ph to explore our full range of lubrication solutions and ensure the continued success of your operations. Â