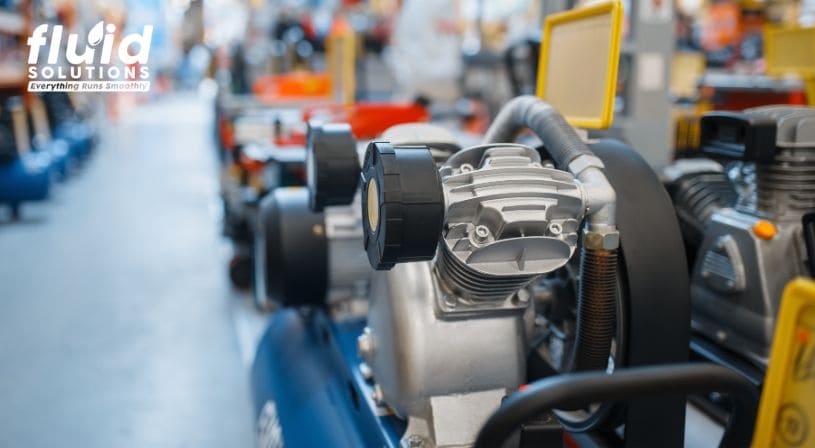
Source: https://www.arrowmaxcompressorandpumps.com/key-contributions-of-compressor-suppliers/
Air compressor applications are particularly demanding, especially for wet-type compressors where air compressor oil is injected directly into the compression chamber. These conditions necessitate specialized lubrication to ensure optimal performance and longevity of the equipment. Whether dealing with reciprocating air compressor oil or rotary screw compressor oil, selecting the right product is critical for maintaining the efficiency and durability of these systems. This blog will explore the specific lubrication needs for different types of compressors and the key properties that make an air compressor oil suitable for these demanding applications.
Functions of Air Compressor Oils
For Reciprocating Types:
- Lubrication of Crankshaft Bearings: The air compressor oil must effectively lubricate the bearings on the crankshaft, reducing friction and wear to ensure smooth operation and extend the life of the compressor. Â
- Lubrication of Piston and Cylinder Wall Contact: Proper lubrication between the piston and the cylinder wall is crucial for minimizing wear and maintaining the efficiency of the compression process, making reciprocating air compressor oil an essential component of these systems. Â
- Heat Absorption in the Compression Chamber: The oil plays a vital role in absorbing heat generated within the compression chamber, preventing overheating and ensuring consistent performance.
For Rotary (Screw) Types:
- Lubrication of Gears and Bearings: In rotary screw compressors, the oil lubricates the gears and bearings that drive the rotors, reducing wear and ensuring smooth operation. Selecting the right rotary screw compressor oil is essential for maintaining the integrity of these critical components. Â
- Heat Absorption in the Compression Chamber: Like reciprocating compressors, rotary screw compressor oil must absorb heat within the compression chamber, preventing excessive temperatures that can lead to equipment failure. Â
Key Properties of Air Compressor Oils​​
Compressor Oil Viscosity
Selecting the correct compressor oil viscosity, as specified by the Original Equipment Manufacturer (OEM), is essential for ensuring proper lubrication under the operating conditions of the compressor. The right viscosity helps maintain a protective oil film on all moving parts, reducing wear and tear and ensuring the efficient operation of the compressor.
Oxidation & Carbonization Resistance
Air compressor oils must exhibit high oxidation and carbonization resistance to ensure stability and long oil life. This reduces the frequency of oil changes, which is crucial for maintaining productivity and minimizing downtime.
Extreme Pressure & Anti-Wear Capabilities
The oil must provide extreme pressure and anti-wear protection to safeguard the mechanical components of the compressor, especially under high-stress conditions.
Demulsibility
Outstanding demulsibility is necessary for the oil to effectively separate moisture that inevitably mixes with it during operation. This property helps prevent corrosion and maintains the efficiency of the lubrication system.
Low Volatility
Low volatility is important for reducing oil consumption and improving overall efficiency. Oils with low volatility maintain their performance over a longer period, reducing the need for frequent top-ups and extending compressor oil change intervals.
The Importance of Oxidation Stability
Oxidation stability is a key factor in enhancing the life of air compressor oils, particularly in environments where the temperature in compression chambers can reach up to 100°C. Frequent oil changes hinder plant productivity, making oxidation stability a critical property. Mineral-based oils typically oxidize rapidly at 90°C, making synthetic-based lubricants a more favorable choice for industrial applications. Synthetics not only offer better oxidation stability but also provide longer compressor oil change intervals, ranging from 6,000 to 8,000 working hours, which significantly reduces maintenance frequency and associated costs. Â
Benefits of Synthetic Lubricants
Synthetic lubricants, including Polyalphaolefins (PAOs), esters, and polyglycols, offer several advantages over mineral-based oils. These lubricants have a higher viscosity index, providing excellent lubrication even under high-temperature conditions. Additionally, synthetic oils are less volatile, reducing oil consumption and extending the service life of the compressor. When selecting the appropriate synthetic base oil for your air compressor, consulting with the OEM is recommended to ensure compatibility and optimal performance.
Need Reliable Air Compressor Oil in the Philippines? Trust Fluid Solutions
Fluid Solutions is your trusted supplier of high-quality air compressor oils, tailored to meet the demanding needs of both reciprocating and rotary screw compressors. As a leading name among, we offer a comprehensive range of lubrication solutions, including hydraulic oils, slideways oils and gear oils. Fluid Solutions is committed to providing products that enhance the performance and longevity of your equipment. Contact Fluid Solutions today at (02) 8370 5928 / (0917) 894 9156 or via email at inquiry@fluidsolutions.com.ph for expert advice and to explore our product offerings. Â