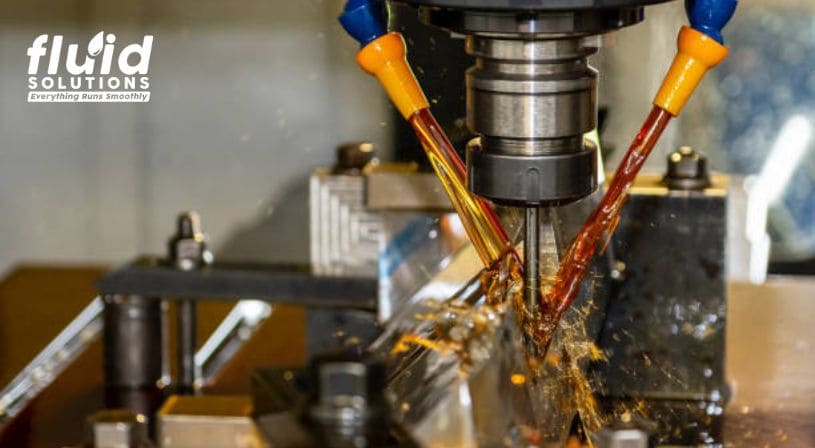
Source: https://www.istockphoto.com/photo/the-cnc-milling-machine-cutting-the-mold-parts-with-oil-coolant-method-gm1436138542-477260357?searchscope=image%2Cfilm
Unlike water-miscible cutting fluids or coolants, neat cutting oils are recommended for machining applications where lubrication takes priority over cooling. These oils are useful in operations where metal removal is relatively large, speeds are slow, or where extreme friction occurs.
When to Use Cutting Oils
Cutting oils excel in high-friction applications, commonly found in industries such as automotive manufacturing. Operations like gear hobbing, broaching, gear cutting, and thread rolling often require more lubrication because of the higher depth of cuts and the slower speeds involved. For such scenarios, a higher viscosity cutting oil, typically at 32 cSt at 40 °C, is recommended. These oils are usually fortified with sulfurized and/or chlorinated extreme-pressure additives, which help reduce wear and prolong tool life.Â
Where machining involves more difficult-to-cut metals like stainless steels, cutting oils also prove superior. For turning, milling, drilling, and tapping operations on stainless steel with smaller diameters, oils with viscosities between 10 – 15 cSt at 40 °C, again reinforced with extreme-pressure additives, are ideal for ensuring satisfactory tool life and part finish.
Low Viscosity Oils for Honing and Grinding

Source: https://www.istockphoto.com/photo/the-lathe-machine-finish-cut-metal-shaft-parts-with-liquid-coolant-method-gm1767003402-545430517?searchscope=image%2Cfilm
For high-speed processes like honing operations and grinding, low – viscosity cutting oils—between 2 – 5 cSt at 40 °C—are sometimes used. These low-viscosity oils provide enough lubrication while still allowing higher operational speeds. However, they may cause misting and smoking issues because of their lighter formulation, so it’s important for operators to maintain oil levels in the machine sump and monitor potential mist generation.
Selecting the Right Viscosity
As a rule, the machine operator should remember that:Â
- Higher viscosity oils (e.g., >32 cSt at 40 °C) are better suited for low-speed, high-friction applications such as gear hobbing and broaching.
- Mid-viscosity oils (10 – 15 cSt at 40 °C) work well for turning, drilling, and milling operations, particularly with tough materials like stainless steel.
- Low-viscosity oils (2 – 5 cSt at 40 °C) are best for high-speed processes like honing and grinding, but they come with some drawbacks, such as misting and smoking.
In summary, selecting the correct oil viscosity based on the specific application is crucial for optimizing both tool life and part quality.
The Importance of Extreme-Pressure Additives
For demanding machining operations, extreme-pressure additives are essential in reducing tool wear and ensuring smooth metal cutting. Neat cutting oils fortified with these additives provide an added layer of protection, particularly when dealing with tougher metals or higher friction scenarios. These additives also enhance the performance of industrial gear oil, providing lubrication for critical machine components under heavy loads.
Find the Best Metalworking Fluids and Lubrication Solutions at Fluid Solutions
Looking for a reliable cutting oil supplier in the Philippines? Choose Fluid Solutions! We are a trusted metalworking fluids manufacturer, offering a range of lubrication solutions tailored to your business needs. Our product portfolio includes neat cutting oils, hydraulic oils, industrial gear oil, slideway oils, synthetic lubricants, high-temperature greases, and anti-rust oils.Â
Contact Fluid Solutions today at (02) 8370 5928 / (0917) 894 9156 or via email at inquiry@fluidsolutions.com.ph to speak with our expert Lubrication Consultants and find the best solutions for your machining and lubrication needs.