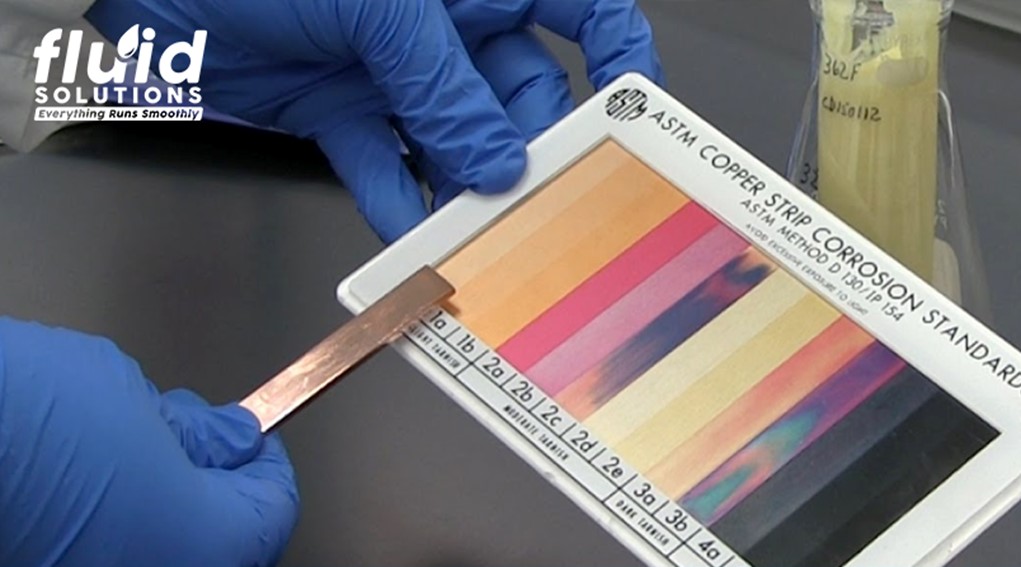
One crucial method employed to assess a lubricant’s ability to safeguard copper and non-ferrous metals is the copper corrosion testing. Let’s delve into the intricacies of this testing process, its significance, and the advantages offered by different types of lubricants and rust preventive oil.
Understanding the Copper Corrosion Testing
Definition and Purpose
A copper corrosion strip test is performed to determine a lubricant’s capability to protect copper and copper-containing alloys from corrosion or staining. The test results are also indicative of a lubricant’s corrosion protection properties with other non-ferrous metals such as aluminum.
Significance
This test holds immense significance in determining a lubricant’s suitability for use in machinery where copper corrosion could compromise performance and longevity. It provides valuable insights into a lubricant’s protective capabilities, guiding manufacturers and users in selecting the most appropriate lubrication solutions.
Navigating the Testing Process
Conducting the copper corrosion test involves immersing a cleansed copper strip in the test lubricant and subjecting it to elevated temperatures, typically around 100°C, for a specified duration, commonly 24 hours. The resulting appearance of the copper strip is then compared to an ASTM* copper strip corrosion standard, and the lubricant receives a rating based on its corrosion protection capability.
*ASTM – American Society for Testing and Materials
Deciphering the Results
The ASTM copper strip corrosion standard categorizes lubricants based on their corrosion protection capabilities, ranging from 1a and 1b denoting superior performance to successive numbers like 2, 3, and 4, indicating weaker capabilities. Understanding these ratings is crucial for selecting the most suitable lubricant for specific industrial applications.
Contrasting Lubricant Types
DID YOU KNOW? Compared to Mineral Oils and PAOs (Polyalphaolefin), Esters are known to run clean and resist oxidation and carbonization at elevated temperatures.
Several types offer distinct advantages in corrosion protection and resistance to oxidation. While mineral oils and PAOs have their merits, esters stand out for their exceptional cleanliness, oxidation resistance, and carbonization resistance at elevated temperatures. This makes them particularly well-suited for demanding industrial environments.
Partner with the Leading Industrial Lubricants Provider
In conclusion, the copper corrosion test serves as a cornerstone in evaluating lubricant performance and protecting critical machinery components from corrosion. By understanding the intricacies of this testing process and selecting the right lubricant type, industries can ensure optimal machinery operation and longevity. For expert guidance and access to high-quality industrial lubricants, look no further than Fluid Solutions. We offer various industrial lubrication products like Food Grade Oils and Greases, High Performance Greases, Specialty Lubrication, Maintenance Equipment, and Metalworking Fluids. Contact Fluid Solutions today at (02) 8370 5928 / (0917) 894 9156 or via email at inquiry@fluidsolutions.com.ph to elevate your lubrication practices and enhance machinery performance.