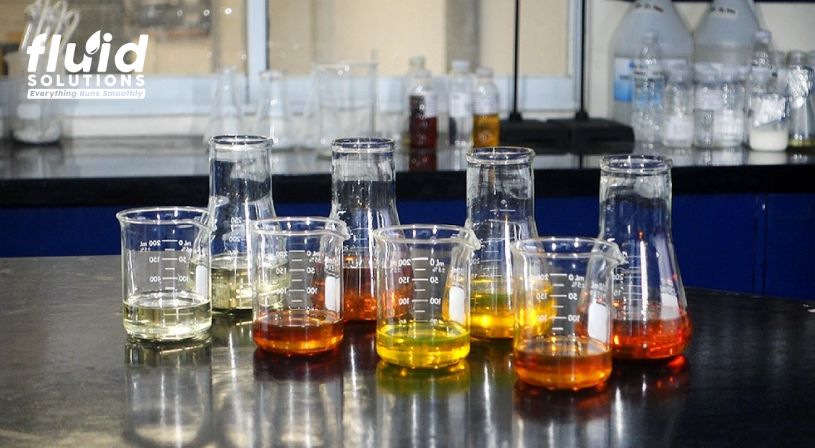
Water-soluble cutting fluids, commonly referred to as coolants, have become essential in modern machining and grinding processes. Selecting the right coolant for the specific job is crucial to maximize the benefits of these fluids. Among many options, there are three primary types of technologies available in the market today: emulsions, synthetics, and semi-synthetics. Understanding the differences between these types helps ensure selecting the best choice for your operations.
Emulsions: The Oldest Technology for Moderate to Severe Machining
Emulsions are one of the most traditional among water-soluble cutting fluids. These fluids typically contain a significant amount of mineral oil, and sometimes, esters are added to enhance boundary lubricity. Additives such as rust and corrosion inhibitors, extreme pressure performance enhancers, foam control agents, and biocides, are included to boost the performance of emulsions.
How Emulsions Work
Since mineral oils rarely mix with water, emulsions rely on emulsifiers to disperse the oil component homogeneously into the water-oil mixture. This process results in a milky-white fluid that is ready for machining operations.
Emulsions are commonly used in moderate-to-severe machining tasks like drilling, boring, and tapping. They are preferred for less machinable metals, such as stainless steel. Their high oil content provides excellent rust and corrosion protection, maximizing tool life. Affordability also makes emulsions an attractive option for industries prioritizing cost-efficiency.
Disadvantages of Emulsions
Despite their advantages, emulsions have several drawbacks, including:
- Poor bio-stability, which leads to bacterial growth and foul odors.
- Sticky residues that affect the appearance of workpieces and contribute to dirty machines.
- Instability, where the oil phase can separate from the emulsion over time, reducing its effectiveness as a coolant.
Maintaining proper monitoring and control is essential when using emulsions as they are more prone to breakdown than other coolant technologies.
Synthetics: Optimal for High-Speed Operations and Grinding
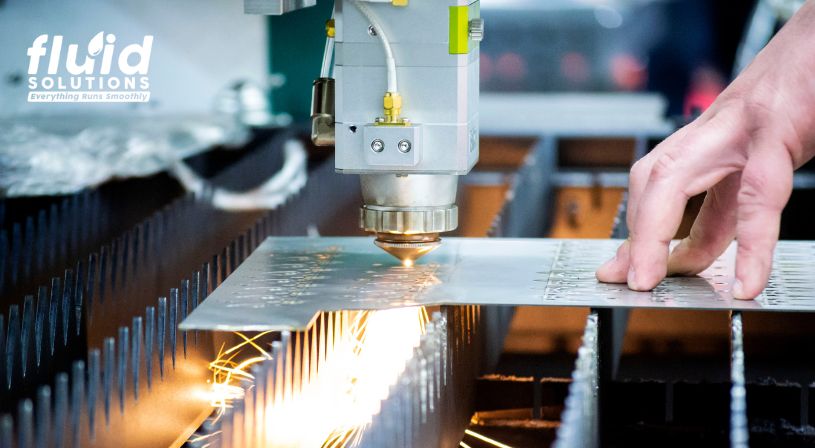
At the opposite end of the spectrum are synthetic coolants, which contain no mineral oils or esters. Synthetic cutting fluids are designed for high-speed operations, such as grinding, where maintaining a cooler temperature is critical.
Since synthetics are primarily water-based, they offer excellent cooling capabilities. Additives are included to enhance rust and corrosion protection, while polymers may be added for lubrication. Synthetic coolants also contain foam control agent and biocides, ensuring higher performance and stability. Unlike emulsions, synthetic coolants do not require emulsifiers because they contain no oils.
Why Use Synthetics?
Synthetic coolants are known for their stability as they won’t separate or degrade over time due to having no mineral oil, offering a longer service life compared to emulsions. Â
Synthetics are also less prone to bacterial attacks, making them ideal for processes where cleanliness and consistency are crucial. Additionally, synthetics are good flushing agents, particularly effective as coolants for grinding machines where small metal particles and grinding dust must be efficiently flushed away.
The typical recommended concentration for synthetics is 3-5%, and the mixture with water is either transparent or transparent with a bluish or greenish tint.
Limitations of Synthetics
While synthetic coolants excel in cooling and stability, they may not be the best choice for machining operations that require higher levels of lubrication, such as deep cuts or high-friction processes. Their rust and corrosion protection are also limited compared to emulsions, making them less suitable for applications where these factors are paramount.
Semi-Synthetics: A Versatile Option for Both Machining and Grinding
Semi-synthetics sit between emulsions and synthetics in terms of composition and performance. These coolants contain both an oil phase and a water phase, requiring emulsifiers to maintain a stable mixture. This hybrid approach offers some benefits from both emulsions and synthetics.
Benefits of Semi-Synthetics
Semi-synthetic coolants are less sticky and heavy than emulsions, making them easier to work with and less likely to leave residues on machines or workpieces. Although they don’t offer the same high levels of lubrication as emulsions for tough jobs, they excel in other areas, such as:
- Bio-stability, which leads to a longer sump life and a more pleasant, odor-free environment.
- Stability, ensuring the coolant remains effective over time without oil separation.
- Cleaner workpieces and machines, reducing the need for frequent cleaning and maintenance.
Semi-synthetics are increasingly popular in the market, particularly for smaller machine shops that want a synthetic coolant for machining that can handle both machining and grinding tasks. These fluids typically exhibit a pale-white, translucent appearance when mixed with water and are used in concentrations between 3-10%.
Choosing the Right Coolant for Your Needs
Choosing the right coolant involves considering the specific requirements of your machining or grinding process. Emulsions offer high lubrication and rust protection, making them ideal for moderate-to-severe operations, but they require diligent maintenance because of bio-stability issues. Synthetics provide superior cooling and stability, making them perfect for high-speed grinding operations, in exchange for their lack of lubrication performance. Semi-synthetics offer a balance between the two, making them versatile options for a wide range of applications.
Discover Our Range of Cutting Coolants and Lubrication Oils Today
If you need high-performance cutting coolants, look no further than Fluid Solutions. We offer a wide range of lubrication solutions, including synthetic coolants, semi-synthetics, and emulsions, as well as hydraulic oils, slideway oils, gear oils, high-temperature greases, and anti-rust oils.
Contact Fluid Solutions today at (02) 8370 5928 / (0917) 894 9156 or via email at inquiry@fluidsolutions.com.ph to speak with one of our Lubrication Consultants and find the best solutions for your business.